whereswally606
100 kW
In an effort to create safer and quality connectors I have been toying with the idea of ganging together some 4mm bullets with the plastic cases into a parallelogram formation and connecting up all the +ve together and all the -ves together with a single rod of copper.
here is the first piece in the puzzle
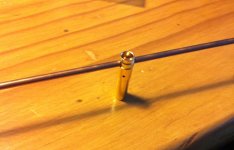
4mm female with a 2.5mm hole drilled through inserted 2.4mm copper welding rod apparently 98% copper. Gonna parallel through the balance taps too but this should make for a more even strain on the cells. I can then more easily break the sub packs down for para charging too using a similar idea.
wish i had a plastic printer cause id make some really nice custom plastic covers for them, as it is i will make do with binding together the red plastic jackets they have.
a bonus to making the sheathing would be that the cost would come right down and the build time.
Nechaus fancy having a go?
The reason I am not just clipping the connector on the batteries is to maintain warranty and help reduce loss on resale value.
when I've done a full connector I'll post it, but I've got to finish my thesis first so could be a couple of weeks
here is the first piece in the puzzle
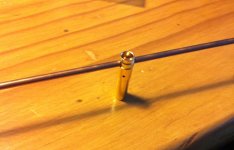
4mm female with a 2.5mm hole drilled through inserted 2.4mm copper welding rod apparently 98% copper. Gonna parallel through the balance taps too but this should make for a more even strain on the cells. I can then more easily break the sub packs down for para charging too using a similar idea.
wish i had a plastic printer cause id make some really nice custom plastic covers for them, as it is i will make do with binding together the red plastic jackets they have.
a bonus to making the sheathing would be that the cost would come right down and the build time.
Nechaus fancy having a go?
The reason I am not just clipping the connector on the batteries is to maintain warranty and help reduce loss on resale value.
when I've done a full connector I'll post it, but I've got to finish my thesis first so could be a couple of weeks