Kepler
10 MW
Recent experience's with the some nice quality commercial e-bikes got me fired up to look at building a low powered but high speed commuter / flatbar road bike that would be hard pressed to even be recognized as an e-bike by the general public using the local bike paths.
As a bit of back ground, after having a quick test of an e-motion Jumper just around a car park, it felt so impressive that I seriously considered purchasing one. So the next move was to go visit the suppliers and take the bike for a proper test ride. First impressions were very good with some nice assist. However, the bike was limited to 25kph assisted as per Aust / Euro regs. So to ride the bike at a decent speed, you needed to work twice as hard because effectively the motor assist was doing nothing for you and you were now trying to push a 20kg bike at a decent speed.
In addition to e-biking, I have to admit I am a closet Lycra
and average about 100km a week on my carbon road bike. Every time I get on this bike I am always blown away by the efficiency of these modern high performance road bikes. I have no doubt I could average a better speed on my road bike then I could on Aust. reg compliant e-bike.
So with this in mind, I figured it was time to blend the best of both worlds and build a e-bike that free rides as well as a high spec road bike but at the same time had e-assist capable of a sustained 50kph under favorable road conditions.
The process of gathering components has now started. Cornerstone of this build is a full carbon 29er frame complete with rigid carbon forks. I decided to go down the path of a 29er because of my height and the fact that it is a mountain bike frame and as such provides a bit of extra strength. Total weight of frame and forks comes to 1.8kg. Nice start. 8)
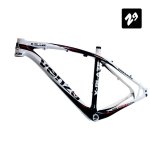
View attachment 1
White Industries disc brake compatible hubs have been laced into 36 spoke 700C rims for strength and fitted with some nice 203mm floating discs back and front. Magura M2 Hydros will be used for some serious stopping power.

More detail on how this bike will be powered to come.
As a bit of back ground, after having a quick test of an e-motion Jumper just around a car park, it felt so impressive that I seriously considered purchasing one. So the next move was to go visit the suppliers and take the bike for a proper test ride. First impressions were very good with some nice assist. However, the bike was limited to 25kph assisted as per Aust / Euro regs. So to ride the bike at a decent speed, you needed to work twice as hard because effectively the motor assist was doing nothing for you and you were now trying to push a 20kg bike at a decent speed.
In addition to e-biking, I have to admit I am a closet Lycra

So with this in mind, I figured it was time to blend the best of both worlds and build a e-bike that free rides as well as a high spec road bike but at the same time had e-assist capable of a sustained 50kph under favorable road conditions.
The process of gathering components has now started. Cornerstone of this build is a full carbon 29er frame complete with rigid carbon forks. I decided to go down the path of a 29er because of my height and the fact that it is a mountain bike frame and as such provides a bit of extra strength. Total weight of frame and forks comes to 1.8kg. Nice start. 8)
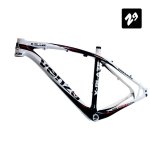
View attachment 1
White Industries disc brake compatible hubs have been laced into 36 spoke 700C rims for strength and fitted with some nice 203mm floating discs back and front. Magura M2 Hydros will be used for some serious stopping power.

More detail on how this bike will be powered to come.