mxlemming
100 kW
- Joined
- Jul 17, 2020
- Messages
- 1,122
thepronghorn said:Cool update. How does the sliding part for the extra needle bearing work? Do the slotted holes work well enough for belt tension? Are you running an idler for extra tooth engagement on the motor pulley? What's the thickness of the bracket?
Not all is well in the world of ebike.
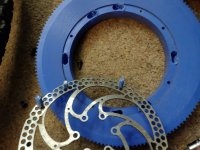
Didn't put all 12 screws in, boosted the power... Dead pulley. This many screws was fine with the little red motor.
Unfortunately I don't have the big 3d printer to use any more so I'm back to the yellow htd8m pulley which is far noisier.
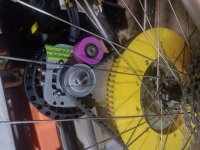
Hopefully this explains a bit better how the tensioner and idler works.
Bracket is 8mm 6082-t6 water jet cut. The slotted holes seen to be fine for belt tension.