Grinhill
10 kW
As many on this forum will agree, it's never too early to start your next build. For those that aren't familiar with my first RC build, check out the link in my signature below.
Not an entire bike, this will be an evolutionary development, using the same bike. Unbolt one, bolt on the next. It will be able to use the same electrics, they can be upgraded separately. It's basically a combination of a few ideas I've had since finishing my first RC project.
I'll still try to meet the same starting specification as the Grinhill Mk1:
What do I like in my first build? The simple belt drive system. The lightweight battery. The easy-to-disassemble design. The low overall weight. The ability to freewheel.
What don't I like in my first build? The ESC losing sync. Being worried that the one-way bearing will fail. The mounting could be improved a little, a bit more stealth and more refined. Maybe a little more power wouldn't hurt.
What started this process? Two main things:
1. Wanting to mount the system within the frame triangle.
2. Wanting to use a larger one-way bearing.
Looking at the first point, when I did a mockup in my first design a location inside the triangle was my first choice, but it wouldn't be able to use the V-brake posts as they are on the wrong side to allow this. It's important to have a strong, flat plate to mount the system to. Here's a sketch incorporating a few ideas:
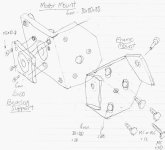
Not an entire bike, this will be an evolutionary development, using the same bike. Unbolt one, bolt on the next. It will be able to use the same electrics, they can be upgraded separately. It's basically a combination of a few ideas I've had since finishing my first RC project.
I'll still try to meet the same starting specification as the Grinhill Mk1:
It will weigh a little more, and will accommodate a larger motor so it will be slighly more powerful (say, 1500W if electrics upgraded).Here's my quick specs:
- weight less than 4kg (8 pounds) including batteries
- power in the range of 600W to 1200W
- bolt on with no mods to the frame, no mods to cranks, no mods to hubs
What do I like in my first build? The simple belt drive system. The lightweight battery. The easy-to-disassemble design. The low overall weight. The ability to freewheel.
What don't I like in my first build? The ESC losing sync. Being worried that the one-way bearing will fail. The mounting could be improved a little, a bit more stealth and more refined. Maybe a little more power wouldn't hurt.
What started this process? Two main things:
1. Wanting to mount the system within the frame triangle.
2. Wanting to use a larger one-way bearing.
Looking at the first point, when I did a mockup in my first design a location inside the triangle was my first choice, but it wouldn't be able to use the V-brake posts as they are on the wrong side to allow this. It's important to have a strong, flat plate to mount the system to. Here's a sketch incorporating a few ideas:
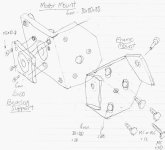