jkbrigman
10 kW
This thread documents the conversion of a Short Wheelbase - Above Seat Steering recumbent bicycle.
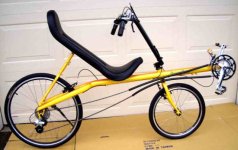
Mission Objective:
30mi/56km range with less than 80% pack discharge or,
70mi/112km range with 80% pack discharge.
Cruise speed 18-25mph/32-40kph with 30mph/48kph burst capable if needed.
Bike Upgrades:
Planet Bike fenders
Schwalbe Marathon tires front and back
Tube liners for puncture protection
Rear rack
Cateye Mini-8 cyclocomputer
Headlight and taillight
The Build Kit (from methods/ebikes.ca):
9c 2810 motor in a 26" rim
36-72V controller
8 speed freewheel w/11T minimum
Direct-connect cycle analyst
Thumb throttle
Torque arms
Advantage and Motivation:
Using this bike for daily commute to pass stopped traffic in the bike lane on the commute route. Traffic backs up for over 5mi/8km, traveling less than 30mph/48kph, stop-and-go. At cruise speed, this bike may be able to achieve a commute time equivalent to an automobile over the same route at the same time.
Energy Budget:
At an estimated energy budget of 15Wh/mi or 10Wh/km this bike will require a minimum of 450Wh to go 30mi/48km. The plan is to build or buy a battery capable of at least 800Wh of energy storage for an 80% utilization. The design calls for a 1000Wh battery. This is possible on 72V, 15Ah. (18S-3P LiPo or 20S-1P A123 flat packs - oversized at 20Ah).
Bike Selection:
The chosen bike has a steel frame, huge sprockets on the front (up to a 52T) and tiny (down to 11T) on the back. The bike came stock with Kenda Kwest 1.25" 100PSI/6.8bar tires, which are being used successfully for ebike uses by some on the forum. Those tires will stay on the stock rims, using Schwalbe Marathon on the new rims for durability and puncture resistance while in use as an ebike.
This bike has no suspension components and uses V-brakes, therefore speeds over 30mph/48kph are not planned. Gearing on the bike (52T front, 11T rear) is intended to provide some power assist at cruise speed. Regen is planned and will come into play on 4 significant hill points in the commute - 2mi/3km of regen is estimated possible in either direction.
Through pre-project polling, members of the E-S forum rightly pointed out two key concepts: 1) That the commute will take upwards of an hour or more each way. A recumbent would make the 2-3 hours in the saddle each day easier and more comfortable. 2) Wind resistance of the recumbent is lower, therefore contributing to the potential for a lower energy cost, higher speed ride. I agreed with these points and switched focus from converting an ill-equipped upright bike to converting a moderately-well-equipped recumbent.
This bike uses a 26 inch rim in the rear and a 20 inch rim in the front. Electric drive using the front 20 inch wheel would be simple and lower-cost: no modifications to the chain drive whatsoever and the stock rear tire/wheel would be reused for ebike use. However, with the smaller diameter 20 inch wheel, rotational speed is slower than the 26" wheel, so more than 72 volts is required to reach the desired maximum speed. This voltage exceeds the intended voltage range for the controller. Furthermore, stresses and wear on the front forks and steering column would be out of spec for the design of the bike. Therefore a conversion of the 20" wheel was ruled out in favor of a 26" rear drive. Potential is there for a future dual-drive upgrade, particularly if research shows dual-drive could save energy on hill climbs.
Open Issues as-of this posting:
Still trying to figure out what battery to use. Advantage to the A123 packs is simplicity, completeness (cell_man includes a BMS with his batteries) and reliability. "000's of cycles" are what the A123's are advertised for, which provides a lifetime measured in years with good battery care. Charger purpose-built for the battery can be purchased from cell_man. Charging is simple and direct: buy two chargers, one for home, one for work, for daytime charging to make the return trip home. Disadvantage is cost. A pack for my required mission runs around $1k before adding in charger and shipping.
LiPo has a cost advantage and incredible current capability. It is also a flexible battery choice - you can change your pack to other voltages or trivially add Ah capabilities by paralleling-in more packs. This can be important if you have no clue how much current you will consume on your desired travel route. However, the disadvantage for LiPo is BMS (LiPo "hobby style" packs do not come with a BMS), cabling and expensive charging equipment. There are solutions to these problems available on E-S, allowing LiPo packs to be charged simply and reliably, but to get there is a "mini-project" with added time and expense upwards of $200.
The cost difference of the A123 vs. LiPo bricks may be little-to-nothing in the end. However, the ability to change the battery configuration (adding Ah) could become important. I do not know the answer to this question at this time, because there is no quantitative answer. Everyone's riding environment is different.
A project goal is to add fairings - particularly a front fairing and a tailbox. Front fairings are painfully expensive - a Zzipper product with hardware would run somewhere around $500US.
Ultimate goal of this project is to reach a minimal Wh/mile or Wh/km number, thereby opening the possibility for doing some long trips on the bike before having to swap out the battery or recharge - would like to exceed 100mi/160km on a charge if possible.
Open Questions on Batteries:
- do you "bulk charge" first at high voltage, then balance the pack, later, or intermittently?
- do you use a BMS of any kind permanently built into your batteries?
- if you DON'T have a BMS integrated into the battery, then how do you balance your cells?
- if you are using mean wells, do you have to mod the meanwells or do you just hook 'em up in series and go?
- if there is anyone charging 18S3P LiPo inexpensively, I seek your comment with data and pictures if possible
- suggesting I look at an existing thread is A-OK: there's an amazing amount of data here and my search-fu isn't so good
Questions and experienced comments solicited!
Thanks for reading! - James
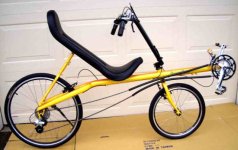
Mission Objective:
30mi/56km range with less than 80% pack discharge or,
70mi/112km range with 80% pack discharge.
Cruise speed 18-25mph/32-40kph with 30mph/48kph burst capable if needed.
Bike Upgrades:
Planet Bike fenders
Schwalbe Marathon tires front and back
Tube liners for puncture protection
Rear rack
Cateye Mini-8 cyclocomputer
Headlight and taillight
The Build Kit (from methods/ebikes.ca):
9c 2810 motor in a 26" rim
36-72V controller
8 speed freewheel w/11T minimum
Direct-connect cycle analyst
Thumb throttle
Torque arms
Advantage and Motivation:
Using this bike for daily commute to pass stopped traffic in the bike lane on the commute route. Traffic backs up for over 5mi/8km, traveling less than 30mph/48kph, stop-and-go. At cruise speed, this bike may be able to achieve a commute time equivalent to an automobile over the same route at the same time.
Energy Budget:
At an estimated energy budget of 15Wh/mi or 10Wh/km this bike will require a minimum of 450Wh to go 30mi/48km. The plan is to build or buy a battery capable of at least 800Wh of energy storage for an 80% utilization. The design calls for a 1000Wh battery. This is possible on 72V, 15Ah. (18S-3P LiPo or 20S-1P A123 flat packs - oversized at 20Ah).
Bike Selection:
The chosen bike has a steel frame, huge sprockets on the front (up to a 52T) and tiny (down to 11T) on the back. The bike came stock with Kenda Kwest 1.25" 100PSI/6.8bar tires, which are being used successfully for ebike uses by some on the forum. Those tires will stay on the stock rims, using Schwalbe Marathon on the new rims for durability and puncture resistance while in use as an ebike.
This bike has no suspension components and uses V-brakes, therefore speeds over 30mph/48kph are not planned. Gearing on the bike (52T front, 11T rear) is intended to provide some power assist at cruise speed. Regen is planned and will come into play on 4 significant hill points in the commute - 2mi/3km of regen is estimated possible in either direction.
Through pre-project polling, members of the E-S forum rightly pointed out two key concepts: 1) That the commute will take upwards of an hour or more each way. A recumbent would make the 2-3 hours in the saddle each day easier and more comfortable. 2) Wind resistance of the recumbent is lower, therefore contributing to the potential for a lower energy cost, higher speed ride. I agreed with these points and switched focus from converting an ill-equipped upright bike to converting a moderately-well-equipped recumbent.
This bike uses a 26 inch rim in the rear and a 20 inch rim in the front. Electric drive using the front 20 inch wheel would be simple and lower-cost: no modifications to the chain drive whatsoever and the stock rear tire/wheel would be reused for ebike use. However, with the smaller diameter 20 inch wheel, rotational speed is slower than the 26" wheel, so more than 72 volts is required to reach the desired maximum speed. This voltage exceeds the intended voltage range for the controller. Furthermore, stresses and wear on the front forks and steering column would be out of spec for the design of the bike. Therefore a conversion of the 20" wheel was ruled out in favor of a 26" rear drive. Potential is there for a future dual-drive upgrade, particularly if research shows dual-drive could save energy on hill climbs.
Open Issues as-of this posting:
Still trying to figure out what battery to use. Advantage to the A123 packs is simplicity, completeness (cell_man includes a BMS with his batteries) and reliability. "000's of cycles" are what the A123's are advertised for, which provides a lifetime measured in years with good battery care. Charger purpose-built for the battery can be purchased from cell_man. Charging is simple and direct: buy two chargers, one for home, one for work, for daytime charging to make the return trip home. Disadvantage is cost. A pack for my required mission runs around $1k before adding in charger and shipping.
LiPo has a cost advantage and incredible current capability. It is also a flexible battery choice - you can change your pack to other voltages or trivially add Ah capabilities by paralleling-in more packs. This can be important if you have no clue how much current you will consume on your desired travel route. However, the disadvantage for LiPo is BMS (LiPo "hobby style" packs do not come with a BMS), cabling and expensive charging equipment. There are solutions to these problems available on E-S, allowing LiPo packs to be charged simply and reliably, but to get there is a "mini-project" with added time and expense upwards of $200.
The cost difference of the A123 vs. LiPo bricks may be little-to-nothing in the end. However, the ability to change the battery configuration (adding Ah) could become important. I do not know the answer to this question at this time, because there is no quantitative answer. Everyone's riding environment is different.
A project goal is to add fairings - particularly a front fairing and a tailbox. Front fairings are painfully expensive - a Zzipper product with hardware would run somewhere around $500US.
Ultimate goal of this project is to reach a minimal Wh/mile or Wh/km number, thereby opening the possibility for doing some long trips on the bike before having to swap out the battery or recharge - would like to exceed 100mi/160km on a charge if possible.
Open Questions on Batteries:
- do you "bulk charge" first at high voltage, then balance the pack, later, or intermittently?
- do you use a BMS of any kind permanently built into your batteries?
- if you DON'T have a BMS integrated into the battery, then how do you balance your cells?
- if you are using mean wells, do you have to mod the meanwells or do you just hook 'em up in series and go?
- if there is anyone charging 18S3P LiPo inexpensively, I seek your comment with data and pictures if possible
- suggesting I look at an existing thread is A-OK: there's an amazing amount of data here and my search-fu isn't so good
Questions and experienced comments solicited!
Thanks for reading! - James