Hi everyone
I just joined the forum today after checking out some other builds on here and found some really impressive stuff!
I also started building an EV conversion recently using a 1981 KZ440 LTD cafe racer donor and have made some decent progress over the last few weeks. The drive system is now together and on the bench and I’m about to start the 12v wiring and the battery box fabrication. Just wanted to share what I’ve done so far as I’ve gone through a bit of pain in some areas and it may help other builders… plus I’ll have more questions as well.
Overview for the conversion:
1981 kz440 ltd with ktm duke 390 front end
Custom adapted duke 390 brakes
17” 8kw QS hub motor driven by a Kelly Controller
24s NMC lipo pack @ 7.4kWh
Thunderstruck tsm2500 charger with dilithium MCU, BMS and SOC meter
Vicor 400W switch mode dc-dc converter
8Ah antigravity 12v battery
Motogadget mo.unit blue
Motogadget motoscope pro
EST weight ~140kg
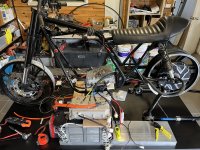
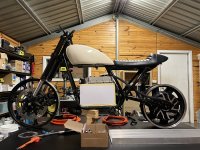
I put some videos together for the build if anyone is interested in checking them out. I ended up doing something a bit different with the drivetrain power so it may be of interest to some. It’s a bit cringy as it’s my first attempt at doing videos so excuse the bad acting and terrible voiceover
KZ 440 EV Restomod - Episode 1: KTM 390 front end conversion
KZ 440 EV Restomod - Episode 2: KTM front brake and rear disc conversion
KZ 440 EV Restomod - Episode 3: Electric drivetrain build and bench test
I just joined the forum today after checking out some other builds on here and found some really impressive stuff!
I also started building an EV conversion recently using a 1981 KZ440 LTD cafe racer donor and have made some decent progress over the last few weeks. The drive system is now together and on the bench and I’m about to start the 12v wiring and the battery box fabrication. Just wanted to share what I’ve done so far as I’ve gone through a bit of pain in some areas and it may help other builders… plus I’ll have more questions as well.
Overview for the conversion:
1981 kz440 ltd with ktm duke 390 front end
Custom adapted duke 390 brakes
17” 8kw QS hub motor driven by a Kelly Controller
24s NMC lipo pack @ 7.4kWh
Thunderstruck tsm2500 charger with dilithium MCU, BMS and SOC meter
Vicor 400W switch mode dc-dc converter
8Ah antigravity 12v battery
Motogadget mo.unit blue
Motogadget motoscope pro
EST weight ~140kg
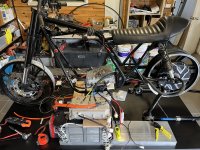
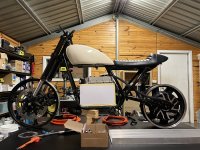
I put some videos together for the build if anyone is interested in checking them out. I ended up doing something a bit different with the drivetrain power so it may be of interest to some. It’s a bit cringy as it’s my first attempt at doing videos so excuse the bad acting and terrible voiceover
KZ 440 EV Restomod - Episode 1: KTM 390 front end conversion
KZ 440 EV Restomod - Episode 2: KTM front brake and rear disc conversion
KZ 440 EV Restomod - Episode 3: Electric drivetrain build and bench test
Last edited: