Lenk42602
10 kW
fellas,
I am exploring doing a stokemonkey/hanebrink type mid drive using a mac 500 watt geared hub motor.
Still in conceptual phase, and coming from a purely FROCK background, I am stumbling a bit on the correlations between gear reduction and final drive ratios, considering:
1.) the MAC is geared
2.) double front chainring setup at the crank and its affect on final drive ratio
3.) 9 speeed rear cassette and its affect on the final drive ratio
4.) rear whell diameter and its affect on the final drive ratio.
I am sifting through a bunch of past posts, and still trying to grasp a better sense of the way this stuff all shakes out. The goal here is to determine if this is a better route to take than a DD in a small diameter rear wheel.
Parameters/considerations:
1. need to keep the mac @ ~ 400 rpm to avoid heat
2. associated grades w/ Pike's peak
3. minimum amount of battery capacity - ($$$$ broke from my last project, now complete)
4. optimum "wind" scenarios
5. i plan on pedaling my ASS off, still fairly good power generation as I ride a good bit
Anyways, if anyone can point me to some good discussions/links/input/etc that can help me gain a better grasp on this stuff, I would appreciate it.
By the way, here is the platform - I am basically planning on separating the swingarm from the main triangle, relocating it behind the seat post, and welding it rigid (no rear suspension) with sufficient space for the hub motor to fit. Nice elevated chain stays, and the whole thing is steel....
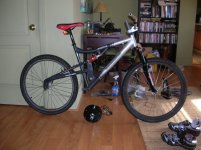
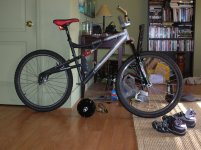
Rather than 11 months, this looks like it might take just a few weeks to get the frame together
Thanks,,
len
I am exploring doing a stokemonkey/hanebrink type mid drive using a mac 500 watt geared hub motor.
Still in conceptual phase, and coming from a purely FROCK background, I am stumbling a bit on the correlations between gear reduction and final drive ratios, considering:
1.) the MAC is geared
2.) double front chainring setup at the crank and its affect on final drive ratio
3.) 9 speeed rear cassette and its affect on the final drive ratio
4.) rear whell diameter and its affect on the final drive ratio.
I am sifting through a bunch of past posts, and still trying to grasp a better sense of the way this stuff all shakes out. The goal here is to determine if this is a better route to take than a DD in a small diameter rear wheel.
Parameters/considerations:
1. need to keep the mac @ ~ 400 rpm to avoid heat
2. associated grades w/ Pike's peak
3. minimum amount of battery capacity - ($$$$ broke from my last project, now complete)
4. optimum "wind" scenarios
5. i plan on pedaling my ASS off, still fairly good power generation as I ride a good bit
Anyways, if anyone can point me to some good discussions/links/input/etc that can help me gain a better grasp on this stuff, I would appreciate it.
By the way, here is the platform - I am basically planning on separating the swingarm from the main triangle, relocating it behind the seat post, and welding it rigid (no rear suspension) with sufficient space for the hub motor to fit. Nice elevated chain stays, and the whole thing is steel....
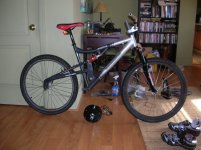
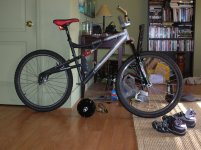
Rather than 11 months, this looks like it might take just a few weeks to get the frame together
Thanks,,
len