stator
1 W
I went with a 1.2K resistor for R1. I measured 47V on the input to the LM317 with the battery fresh off the charger.
Here is the result of the no-load test on a X5304 motor. The top CA is plugged in to the controller. The bottom one is stand alone and is set up to display RPM (multiply by 10).
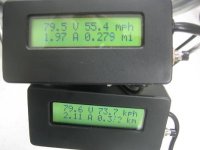
I took it out for a short ride. The throttle response is good (it definitely is not soft start). I noticed the controller cutting out if I gave it full throttle too quickly (when the current reached about 40A). I think this is because the input to the LM317 is dropping too low. I have to release the throttle to recover. It seemed to get worse as the battery wore down.
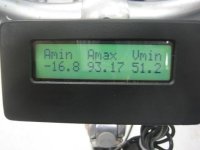
I don't really believe that max current reading.
I recharged the battery and moved it and the controller to a different bike. This one has a 9C rear hub. The CA is standalone. I reset it and went for a four mile ride with some hills. I blew by a couple of cyclist climbing the hills
.

I reset the CA before the trip.
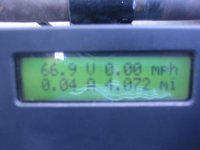
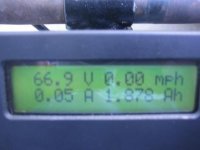
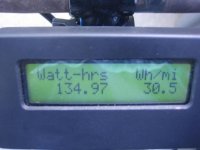
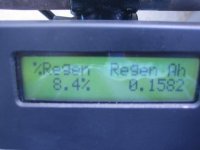
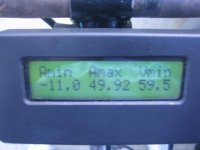
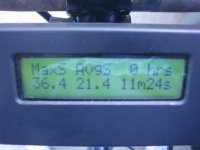
I put my hand on the controller a few times throughout the ride and it was barely warm. The battery was heating up though.
After the ride I measured the battery temperature at 146F. The controller case was 95F.
I need to do something about the controller cutting out. It is annoying.
Here is the result of the no-load test on a X5304 motor. The top CA is plugged in to the controller. The bottom one is stand alone and is set up to display RPM (multiply by 10).
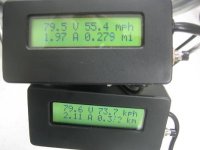
I took it out for a short ride. The throttle response is good (it definitely is not soft start). I noticed the controller cutting out if I gave it full throttle too quickly (when the current reached about 40A). I think this is because the input to the LM317 is dropping too low. I have to release the throttle to recover. It seemed to get worse as the battery wore down.
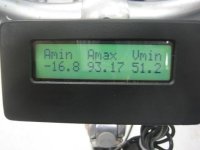
I don't really believe that max current reading.
I recharged the battery and moved it and the controller to a different bike. This one has a 9C rear hub. The CA is standalone. I reset it and went for a four mile ride with some hills. I blew by a couple of cyclist climbing the hills


I reset the CA before the trip.
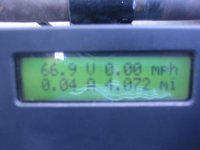
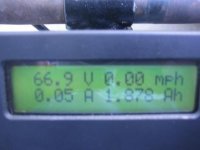
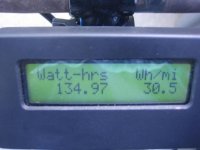
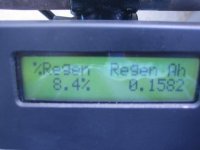
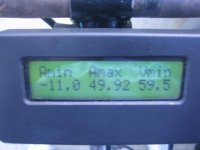
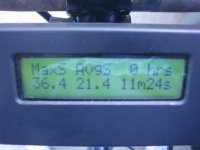
I put my hand on the controller a few times throughout the ride and it was barely warm. The battery was heating up though.
After the ride I measured the battery temperature at 146F. The controller case was 95F.
I need to do something about the controller cutting out. It is annoying.