bikesnobyyc
100 µW
- Joined
- Apr 17, 2020
- Messages
- 7
casainho said:I updated the wiki on how to install TSDZ2 on cargo bike -- now I am looking for notes and pictures of installation on a fat bike, I think this is the last category left - anyone available to share his own notes and pictures?
![]()
I've done a very detailed fat bike build this year and it turned out great. Here are a couple of pictures. I'll send you several detailed pictures and notes on the build by email for your Wiki.
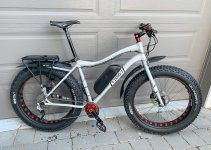
