StudEbiker
100 kW
Well, I had some time today to play around with getting the plates mounted and I am happy to say that things went well today! I am never comfortable drilling into frames and I knew I only had one shot to get this right so I went extra careful and sloooooooow and tripled checked everything and was as careful as I could be. It paid off.
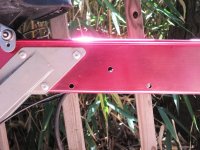
Then to fit the plates and see how things are looking. It's really starting to look like the idea I had in my head. I am very happy to see this project finally coming together.
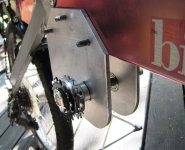
I could do a little more today, but I think I'm going call it a day. Clean my place up and enjoy the awesome weather we're having.
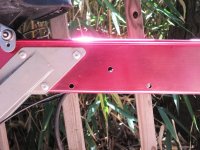
Then to fit the plates and see how things are looking. It's really starting to look like the idea I had in my head. I am very happy to see this project finally coming together.
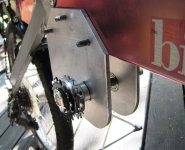
I could do a little more today, but I think I'm going call it a day. Clean my place up and enjoy the awesome weather we're having.