A few people have been asking about output connectors on the satiator. We have each unit come with a 1m cable that terminates into a 3-pin male XLR, which is relatively common with turn-key ebike battery packs but significantly less so with DIY batteries. So with each of these beta units we'll also add an XRL->Anderson adapter into the same adapter as the programming cable, like so:
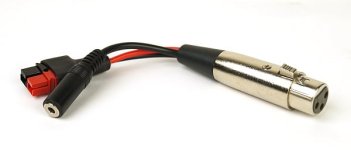
That should be more convenient for a lot of people. It also in principle allows us to do realtime data logging of the charger from the communications port. It's not something that we've implemented in the user firmware yet, but we do have a debug output stream that could be useful for any diagnostics recording during the beta process.
If you have your own custom charger wiring, it's worth noting that the satiator estimates the losses from the cable lead resistance to the pack and compensates for that on the output. So if at 8 amps it assumes there is 0.4V lost on the charger output leads, then it will put out an extra 0.4V at the source so that at the battery proper it has the desired voltage. In the final firmware this lead resistance will be programmable so you can change it to match any custom lead wiring, but at the moment it is fixed in code.
-Justin
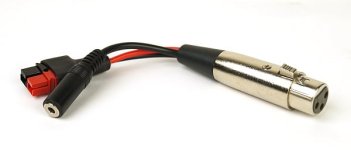
That should be more convenient for a lot of people. It also in principle allows us to do realtime data logging of the charger from the communications port. It's not something that we've implemented in the user firmware yet, but we do have a debug output stream that could be useful for any diagnostics recording during the beta process.
If you have your own custom charger wiring, it's worth noting that the satiator estimates the losses from the cable lead resistance to the pack and compensates for that on the output. So if at 8 amps it assumes there is 0.4V lost on the charger output leads, then it will put out an extra 0.4V at the source so that at the battery proper it has the desired voltage. In the final firmware this lead resistance will be programmable so you can change it to match any custom lead wiring, but at the moment it is fixed in code.
-Justin