jordanjozsef
1 W
- Joined
- Oct 3, 2018
- Messages
- 53
I was having a few experiences with the same hub motor with different rim sizes and I found out the smaller the wheel, the higher the torque, but correct me at any statement if I'm wrong, I'm not an engineer or electrician, it's just my hobby. The efficiency should be better too, because at higher rpms, more power can be delivered without heating up the motor. My first try was a 28 inch wheel, 48V 30A controller with a 300W rated DD hub motor, top speed was 50 km/h with great acceleration. That's what I thought, because I've never tried an ebike before. My second ebike I tried was a 36V 14A one with 18" wheels, it was slower, only 25 km/h, but the torque was way better with less power. So I thought its the way to go, I just need to increase the voltage to increase the speed and power, so I will have insane torque and speed too. I bought a high speed 3kW rated hub motor and laced in a 20" rim. 120V 54A and that thing was both fast and powerful, but the current was too low to reach it's top speed. The 10 AWG phase cables were still warm during hard acceleration at low rpms, so either the voltage is too high or the wheel is still too large. It's a spoked hub motor, but it's impossible to lace in a rim smaller that 20", but I didn't want to decrease the voltage to get better efficiency, because it also decrease the power. I had a 16 inch brushed hub motor wheel, so I cut out the motor and put my 3kW motor without spokes. It looks weird, but it works. And oh my God, the torque. Even 72V 90A beats my pervious 120V 54A 20 inch config, but the power is the same. Top speed was still 68 km/h, so it's fast and very powerful. I applied 120V again and the rear fork didn't like it, the axle twisted, so the cables and my cables and fork are damaged so I have to make a stronger fork plus I have to open up the motor, because the controller throws me hall fault. 120V would give me around 110 km/h top speed, which is still very fast, but I can't put the motor in a smaller wheel.
I know, high speed motor and high voltage is not a good combo a high torque motor in a large wheel could do the same, couldn't it?
There are some pictures and videos.
https://youtu.be/qIYIvo2FHEo
https://youtu.be/9iO7I3zGIlE

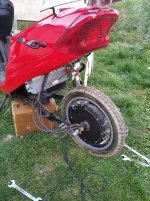
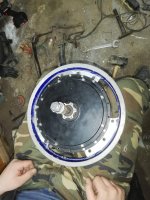
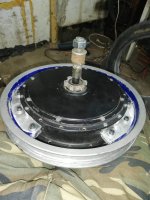
There's only one question: is the axle connected strong enough to handle all this torque? I'm not worried about smoking the motor, but I'm worried about the axle. It's steel of course, but the stator is aluminium, so they can't be welded together, so they can come loose over time and possibly break the stator. Can that happen?
I know, high speed motor and high voltage is not a good combo a high torque motor in a large wheel could do the same, couldn't it?
There are some pictures and videos.
https://youtu.be/qIYIvo2FHEo
https://youtu.be/9iO7I3zGIlE

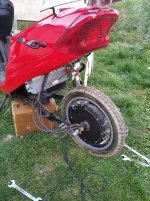
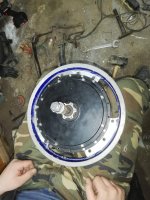
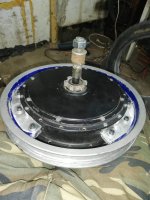
There's only one question: is the axle connected strong enough to handle all this torque? I'm not worried about smoking the motor, but I'm worried about the axle. It's steel of course, but the stator is aluminium, so they can't be welded together, so they can come loose over time and possibly break the stator. Can that happen?