Ok this pretty much ends the I leave stuff alone part of the review. After 500 miles of riding to work and back and a few torture tests, it's time to open er up and see the damage. What? no damage? Sure enough, none I can see. This is one sturdy little motor.
The last couple miles of the 500, I took it over the mountain to a road that has several miles of 10-13 % grade. I had put a thermometer on the axle stub, and in 95 F weather started riding up the grade. It was pretty hard to get up this grade, but in the low speed high torqe mode, the Fusin was able to go up it at about 7 mph with pedaling. On the steepest parts, it could not keep going unless you helped with pedaling, but I never had to pedal very hard to maintain 7-10 mph. The temperature though, was another story. Just like all the other motors I've heat tested, a steady climb in temperature resulted from the steep climb in altitude. In warm weather, I quickly reached the danger zone, which I consider to be about 170F. I kept riding, and soon had temps of 170 measured on the axle, outside the hub. I stopped then, and touching the hub, scorched my hand pretty good. So, unfortunately, this motor has the same achilles heel as all the other smaller motors I've ridden. In hot weather, or any weather if ridden long enough, a really steep hill will cause them to overheat pretty quick. I would say that this motor, at peak wattage, overheats just as fast as a typical direct drive motor. Of course I was doing my best to melt the sucker down, but still, I wouldn't want to try to go crosscountry through the mountains on one of these, or ride into stiff wind for hours.
The bottom line is, the smaller motors just can't radiate the heat as fast as the make it in some conditions, such as hot days up steep hills. So you have to monitor temperature somehow, and stop if the motor overheats if you want to go further than 10 miles in hot weather, or up steep hills in any weather.
Back to the good news though, and that is the kind of torture I just put the motor through, did no visible damage. I was particularly expecting to see some wear or indications of the gears not liking all that heat. But the gears look brand new to me. Overvolting of course is another story, and I ran this motor at 36v, but still, I never babyied it, I rode in the dirt some, and never tried to ease on the throttle to save the gears. I just flipped in on and off any way I wanted, creating all kinds of extra torque on things. As you can see in the pics, the gears look cherry.
The only thing I found inside was a tiny bit of surface rust on the outside of the motor housing, which is steel. Not that water ever got inside it, but just some humidity in there from time to time.
The only dissapointment was there is not enough space for me to cram two more wires into the axle, so I can have a thermometer inside the hub. I'll have to settle for monitoring axle temps, and then adding 20-30 F to that number to guess at the temps inside.
Here is a pic of the motor apart. Dissasembling it is easy, at least as far as getting the motor can out. Just remove the screws on the wires side, and lift out the can. No problems like with direct drive motors, since you remove the motor, but don't take the motor apart.
Here is a closeup of the gears
And now the other side, with the magnets and halls visible,
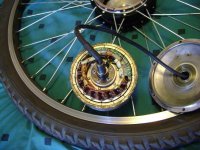