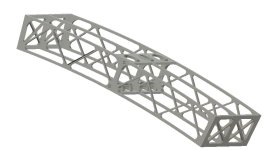
I was bored yesterday, old roll of carbon impregnated petg was screaming use me.
So v1 was 323g of material.
3mm square tubes 75mm tall 'joist', that's a 10mm arch on 500mm span. (8mm arrow shafts for interconnection at center). Not shown outer walls were included at .25mm
Printed with 1mm walls, 4 top and bottom layers at .25mm so 1mm all around the tubes. 10% infill just because I failed to turn it off.
That worked - supported my 240lbs. But bouncing - not so much :lol: broke along the top of the joists surprisingly (point load? Didn't have a top or bottom cover)
So pictured above now moves the open web joists out to 5mm square As usual printed carbon fiber filament there's not a lot of data useful for fusion's FEA module (probably not bad thing, that's probably way outside my skillset anyway)
Curious with all the minds around here - anyone put some thought into this style construction? With the 1mm nozzle on I printed the first test off last night - can make for quick iteration designs.
In some ways I know its a terrible idea. But it is so much cleaner and less smell than laying up true composites... If a redneck engineer like me can support my not insignificant weight - I do wonder if this couldn't be improved on.
Thoughts?