John in CR
100 TW
If you had this much balsa wood, what would you do with it ebike wise? I've got some ideas, especially using the portions of logs with gentle and uniform curves...like aero side covers to enclose batteries. Maybe some of you guys have ideas I can use. Note that the gallon milk jug is for scale.
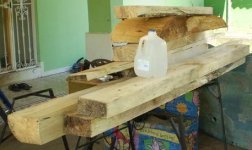
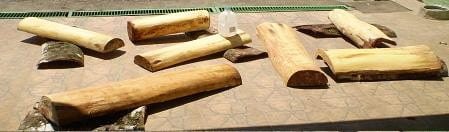
Not that I kept the bark that is peeled off. It's about 1/2" thick and is a bit denser than the wood itself, but the inside of the bark is very smooth.
Some of the pieces made into lumber will have to go to something like a chair made with 4"x6" lumber for a super heavy and strong look that weighs just a few pounds, but that's a separate topic.
Whatever I make with the wood will get a coating of clear epoxy to seal it from water, as well as strengthen and harden the exterior. I'll hollow out the inside to get it down to a thin and light unit.
Any ideas?
John
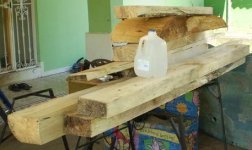
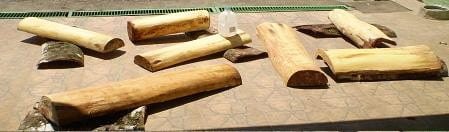
Not that I kept the bark that is peeled off. It's about 1/2" thick and is a bit denser than the wood itself, but the inside of the bark is very smooth.
Some of the pieces made into lumber will have to go to something like a chair made with 4"x6" lumber for a super heavy and strong look that weighs just a few pounds, but that's a separate topic.
Whatever I make with the wood will get a coating of clear epoxy to seal it from water, as well as strengthen and harden the exterior. I'll hollow out the inside to get it down to a thin and light unit.
Any ideas?
John