tostino
10 kW
I have been trying to think of the best way to increase my hub cooling.
I have a Bafang, so even if I were to make my side cover swiss cheese, the whole side is covered by my freewheel anyways. I don't think there is any benefit of cutting holes. I know on the 9C and X5, there is room for them, and it seems like they make a huge difference.
So my second train of thought went to computer cooling methods. My video card memory has little heat sinks on them to keep cool.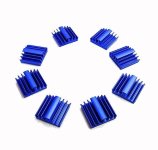
I am thinking that lining the outside of the hub with these little heat sinks using thermal glue like this. I would use enough heat sinks so most of the top of the hub is completely covered, and even possibly some on the side covers.
In addition to this, I also think using thermal paste to help the flow of heat from windings to stator/axle. I would put thermal paste in the black area of this picture but on every one:
.
The reason I am wanting to do this in the first place is I am pushing the little Bafang to 35mph. Where I am is completely flat so heat buildup from hills isn't an issue, however, I am worried I will eventually fry it if going full throttle against a headwind, or even just riding a long time. The temp here just hit 99 today (it's really not much cooler until we get into late december).
Do you guys think this is a worth-while effort, or am I wasting my time?
Thanks for what ever insight you guys may provide!
I have a Bafang, so even if I were to make my side cover swiss cheese, the whole side is covered by my freewheel anyways. I don't think there is any benefit of cutting holes. I know on the 9C and X5, there is room for them, and it seems like they make a huge difference.
So my second train of thought went to computer cooling methods. My video card memory has little heat sinks on them to keep cool.
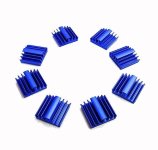
I am thinking that lining the outside of the hub with these little heat sinks using thermal glue like this. I would use enough heat sinks so most of the top of the hub is completely covered, and even possibly some on the side covers.
In addition to this, I also think using thermal paste to help the flow of heat from windings to stator/axle. I would put thermal paste in the black area of this picture but on every one:
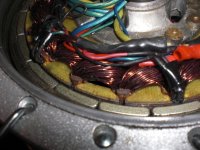
The reason I am wanting to do this in the first place is I am pushing the little Bafang to 35mph. Where I am is completely flat so heat buildup from hills isn't an issue, however, I am worried I will eventually fry it if going full throttle against a headwind, or even just riding a long time. The temp here just hit 99 today (it's really not much cooler until we get into late december).
Do you guys think this is a worth-while effort, or am I wasting my time?
Thanks for what ever insight you guys may provide!