Thanks for the help and kind words. Everybody here is very generous and knowledgeable.
Here's a link to what this thing is supposed to be:
http://www.madeinchina.com/2775653/P6092985/electric-bike-Load-E-bike.shtml
I've attached some pictures of the rewiring. Between that and the built up traces and soldered shunt I got another 5mph out of her from stock. The torque for climbing hills is better too (it's not throwing anybody into 'hyper-space', but I can pass a bus or 2 now, whereas before they'd try to squash me like an irritating little bug).
The inspiration behind this, beside blowing around 'zombie' traffic (most fun ya know) is one day the Missus and I were climbing up a steep street to one of the classrooms we teach at. Somebody did something to make me slow to a crawl at the first part of that hill so I lost momentum. When I got back on the throttle, after about a block, I smelled and touched melting phase wire insulation. Nothing shorted fortunately and the insulation cooled itself back to a fairly normal consistency after. But that was when I said OK! Out with the stupid 'telephone type' phase wire, we're going to put some real wire in this thing! The other good indicator was that the motor and controller were only ambient temp while the phase wires were frying. 'Now' the motor and the controller are only slightly warm and the phase wires are running ambient temps when I load the hell out of it.
The nice thing is that none of this has appeared to negatively effect my range that I can see. I have never had to 'opportunity charge' during the day ('though I put the charger on it 'most every night). I'm at full throttle most of the time running unless I'm caught in a 'cluster f*ck' in an intersection somewhere. On account of the windings in this motor and programming in the controller, I'm getting hellacious regen in this thing and it's weird subtle about it too. Most of the time I never feel it unless I lose like 1 light on the 4 led 'idiot light' volt meter in the instrument panel, then I feel it pulling me gently down when I back off the throttle. I've never hit the 'lvc' limit. One night I drove this sucker for almost 2 hours straight (after putting around 16km during the day), lights on and all, limped it home on 1 remaining 'idiot light, pedaling intermittently for the last 15-20 minutes only.
The only place I've really got to add anything component wise is to the seat post on back. Everything back from there is for hauling Wifey legs or butt or some sort of cargo or other (I've hauled 3 sets of small school desks and chairs, at one shot on the back of this little girl . . . looked like the 'Beverly Hillbillies' were coming to China). That space between the seat post and the rear fender is kinda reserved for future use . . . I'm thinking of playing around with a Hall signal conditioner/adjustable timing box to see if there's anything to be gained from that (that's if I can source somebody here that will actually order something or 'act' like they know what I'm talking about to get the components . . . like flip flops, buffers and such). Oh! and the seat cushions on the back fold open to make another cargo platform in addition to the ones that fold out from the rear axle area(they also act as torque arms, they're slotted onto the axle and tab around the frame).
The battery box is 'stuffed' with the 5 12v 10ah sla's (the bike was advertised as 12ah or 14ah, but when I opened it up . . .'guess what Boo-Boo'! This is China remember!). I'd have to wait for other technology to come down in price and size to bump it up to 72 or 84v. The space down low, between the down tube and the seat post contains the controller, connectors and wiring, a big ol' frame tube and the pedal and sprocket guts (I could 'maybe' fit another controller in there if I got some 'dosh' and inspiration to make it a 2wd someday).
My next little project is to add a 1.0uf 250v mylar or ceramic cap(because I have one laying around) right about center of the pcb, between the main + and - traces for the FET's in the controller to peck at spikes. I may install a fairly hefty diode inverted (stripe to positive) between those traces to help with the same issue (as with the caps on the Hall's, I haven't blown anything up yet, I'm just trying to be proactive based on experiences I've read about here). The main caps in the Controller are too close to peak volts for my liking too, rated at 80v, and if I remember correctly they're only like 890uf each @ 2 of them. I've got a couple of 330uf 200v electrolytic's in parallel on the main battery connector to the controller to help take the load off for now.
Mark
View attachment 5
View attachment 1
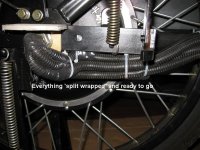