icerider
100 W
So here is the story of my Ranch Dolomite “e-build”.
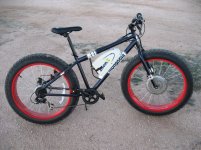
First, what is the purpose of the bike?
Simply put, it is a cheap “alternative” golf cart. We live on 20+ acres scattered across a small rural paved road East of Tucson, AZ. It is a LONG walk from corner to corner of the property and for some reason, problems with the water system or the fencing NEVER happen anywhere near the houses or the garage. My wife and daughter have personal golf carts to move around the property with hay, feed, horses, etc. When they are available, those golf carts are just PERFECT for moving tools and etc. from job to job around the property. But they are not always available and they won’t go everywhere they need to go.
While I would love to have a golf cart, a good used one runs ~$2000 and that is just more than I want to pay for the privilege of not having to carry tools around on foot. I tried my bikes but many of the golf cart paths around the property are 4 inch deep sand. My Terratrike Cruiser does pretty well but bogs down in the sand and my Trek Valencia+ is simply a death trap on sand deeper than half an inch. So the list of requirements for the bike begins to take shape: able to go anywhere on the property, be workable for me, an old fat e-bike kinda guy and be CHEAP.
A couple of years ago I started seeing the fat bikes here and there and read that they were MUCH better at sand and snow (snow is NOT my problem). I resisted for two years but finally succumbed to the urge to buy a cheap fat bike and see whether that would work around the property. I ordered the Mongoose Dolomite from Amazon for $234 delivered.
So, first, the bike. The first Dolomite arrived within 36 hours of my order. It came in one HEAVY cardboard box, but the box looked pretty good – hope springs eternal. I unpacked it and tried to fit the front wheel --- not a chance in hell that wheel was going onto the bike. The front brake disc was wildly out of line with the caliper installed on the front fork. Not a problem, just took the caliper off and mounted the wheel. With the wheel properly mounted it should be a simple task to remount and adjust the front caliper and off we go. This was not to be. With the caliper adjustment screws full loose so that the caliper can float in the mount, it is not even nearly possible to mount the caliper to the provided mounting lug. It is so misaligned that the mount itself, with NO caliper attached cannot be mounted because it interferes with the disc. Convinced that the mounting lug is in the wrong place on the fork, or that the mounting lug is badly bent, I stand in front of the bike and look at the symmetry or rather asymmetry of the front fork. The problem turns out to be that the front fork is bent. The right side angles slightly in and the left side angles slightly out. If I had to pay return shipping on the bike I would probably have straightened the fork, but I am annoyed and I don’t have to pay shipping so I order a replacement from Amazon. It arrives within 24 hours (it is just coming from Phoenix, but that is still FAST free shipping – I LOVE Amazon).
I unpack the replacement bike and assemble it. At least it fits together. I leave it upside down and check out the rotation of the wheels and the function of the low-end Shimano derailleur. The wheels are stiff even with the brake calipers backed all the way out. Shockingly, the derailleur is properly adjusted, but the rear wheel is more than half an inch out of true. Not a problem, at this point I have two Dolomites in the garage and I simply swap the rear wheels. This wheel is stiff too, but it does run true. So I check over the rest of the bike. Front sprocket is true and the chain line is good, the various cables are relatively low quality, but not kinked anywhere, the brake levers are low end but sort of OK, the headset turns smoothly and is properly adjusted, the bottom bracket turns smoothly and is also apparently properly adjusted … OK, it’s a bike. I pack up the other bike and call Amazon who arrange a UPS pickup for the returned bike (at no cost).
So now I have a Mongoose Dolomite. I inflate the tires to 15psi and try it out on the road. It rolls along OK, it is HEAVY to pedal and would be tiring to ride for more than a couple of miles even on level ground, sort of like riding upwind all the time in a good 20 knot wind. And the brakes are TERRIBLE – OH well, I can adjust those. Back to the garage to pull the wheels, grease the wheel bearings and readjust the bearing tension. That makes the wheels run much more freely. On to the brakes. They are low end by ANY definition, but they can be adjusted. The rear brake needs two flat washers on each mounting screw to get it properly aligned with the disc, but the adjustment of the stationary pad is simple and easy and with a minimal gap, I lock the brakes and tighten the 6mm adjusting screws. The disk is almost true and some thumb pressure fixes that. Now the brakes run true without contact with the disc and pull tight with less than one third of the total lever movement. The front brake needs no washers and comes into adjustment quickly, again running freely and coming hard closed with less than a third of the travel of the lever.
Back out on the road, I ride the bike for 4 miles or so. It rolls MUCH better and I could ride this around the neighborhood if I had to, but it certainly wouldn’t be my first choice. But then again, it wasn’t bought to run on the road, it was bought to run down in the sand and weeds. So I take the bike down in the sand and weeds. It rolls through deep loose sand without much trouble. It gets harder to peddle, but the wheels stay on track and there is no feeling of imminent death from having the front wheel wander off in some unexpected direction. This is kind of fun. A sort-of off-road bike … a no-track ride through the weeds and grass on a gently sloping downgrade to the back of the property down by I-10. And therein is the problem. The return trip through sand, grass, weeds, etc. is not a lot of fun even in the lowest gear. Either I need a lower gear, OR A MOTOR.
A little while on Google nets me a few alternatives for motorizing a Fat bike but It is going to be a $500 adventure when the cost of a battery is included and now I am getting into junk golf cart territory.
But as it happens, I have an old retired 2009 vintage I2C Bionx G1 SL350 system in the garage. The battery and control system have gotten “eccentric” over time but this system has the advantage that it is FREE. Now, of course there is little or no chance of putting it on the rear wheel, at least not quickly. The rear dropouts on the Dolomite are reported to be 175mm. 40mm is a LONG way to bend the frame and it will certainly screw up the chain line. But the front is 135mm and the Bionx could fit there … and the old G1 (I2C) system has a throttle. So I can put this on as a front wheel throttle only system … maybe. The mounting of the battery and the wiring to the front wheel are going to be a sticky problem but a quick dry fit says I can probably make it work. What a sad use for a Bionx system, but it is free and maybe later the back wheel, we’ll see.
I need the old Bionx motor moved from a 20 inch wheel into the 26x4 inch rim from the Dolomite. I might even spring for a better rim and I will need a shop to lace it up – That is gonna run ~$100 with the better rim and it is the week before the Tour de Tucson. I know better than to show up in a bike shop the week before the Tour, everybody and his brother are in the bike shop trying to get the bike they ride once a year tuned up for the Tour.
So maybe I could lace it myself if I had the spokes. Well ebikes.ca has a spoke calculator. We don’t say it nearly often enough, but thank you guys for all you do for our community. So I sit down at the spoke calculator and discover to my delight that it has the Bionx PL350 as one of the hub choices. The calculator then wants something called ERD – back to Google and out to measure the Dolomite rim. Back to the calculator and a 1-cross pattern is going to need 176mm spokes. Wait, don’t I have a set of spokes from the Bionx that moved from a 26 inch rim to a 20 inch rim for the Terratrike ??? But that was a double walled rim, there is NO way they are going to fit. But with a no-cross pattern … maybe. That would take a 166mm spoke. Back out to search the garage for those spokes … and they are 170mm … so close but …
So I am sitting at the spoke calculator dejectedly looking at the no-cross pattern when I realize there is no spoke angle AT ALL because the Dolomite rims have two offset rows of spoke holes. That pattern would be DEAD SOFT side to side in the front fork … not good, especially on broken ground even riding slowly. Then I see there is an option to “swap” the spokes (that is, the spokes from the left side of the hub go to the spoke holes on the right side of the rim). What the hell, can’t hurt to try… the required spoke is 169mm and there is some spoke angle to firm up the wheel side to side, and with the errors I have certainly made in measuring/calculating ERD, 169mm is close enough to 170mm that it might be worth trying. And besides, even if I fail miserably, I still needed to take the two wheels apart to show up at the bike shop with motor and rim the week AFTER the Tour de Tucson is over. So, let me be honest, I have never actually considered building a wheel. I have tried with some success to true a slightly warped wheel and that is the sum total of my wheel building experience.
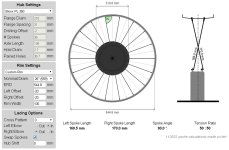
So, back to Google and friends for a lesson in building a wheel. So I find a tutorial at http://www.ebikes.ca/learn/wheel-build.html and a step by step at http://www.electricbike.com/lace-hub-motor . Thank all you folks again for helping our community. With these references in hand I start to take apart the Dolomite front wheel. The tire and tube come off easily but the rubber rim band is glued down tightly enough that it is a PIG to take off. If I weren’t rebuilding the wheel this would probably please me. In any case, I get it off intact. The Bionx motor comes right out of the 20 inch wheel and I move on to building the Bionx motor into the Dolomite rim.
I put each spoke in with 4 initial turns of the nipple and when the pattern is complete, the wheel is VERY loose. Now I am a little worried, but I go around tightening each spoke one full turn. I do this several times and it is amazing how quickly the wheel tightens up. When the wheel begins to look and feel sort of like a wheel I put it in the front fork to true it up. Low and behold it is pretty much true – actually a little better than it was before I took it apart. Now I am pretty sure this is because the Dolomite rim is so wide that it is pretty darn rigid and is just ignoring whatever wheel-building mistakes I have made. I expect that those mistakes will become obvious over time, hopefully with non-fatal results. The spokes still feel too loose and I make two more rounds tightening each spoke one half turn. At that point, the wheel is still pretty darn true and the spokes are getting to be pretty much flush with the top of the nipple. I decide that the spokes are probably more uniform than my wheel building and tighten each spoke once again until it is just flush with the top of the nipple. Once again the wheel is true within a sixteenth of an inch or so, and the spokes seem adequately tight (but not by much). This is working out well enough to make me nervous (whom the Gods would destroy they first make proud).
View attachment 2
So, I mount the wheel (with disc) to the front fork, but I have to remove the disc brake caliper to do this. I tie the caliper out of the way and make a mental note to go VERY slowly until I have that problem fixed. I sit back and decide how to mount the battery bracket and the controller. If I mount the battery bracket with the output wiring facing forward, the big end of the battery faces the small end of my triangle. It fits but JUST barely, in fact, with the battery mounted like that, the battery is VERY difficult to put in and take out and every bounce in the road will be trying to remove the battery from the bracket and connector … NOT a good solution, but good enough for 1am. I plan to put the controller (with throttle paddle) on the right hand side but that interferes with the Shimano twist shifter. I refuse to put the throttle on the left hand side. Both my other bikes have the throttle on the right and so is this one going to. Off come the grips, the brake levers and the Shimano twist shifter. Mongoose has left me enough slack in the cables that all of this works and it makes the bike controls the same as the Prodeco Phantom that my son now rides. That was my first e-bike and I always liked having the twist shifter on the left and the thumb throttle on the right. So at 2am, everything is in place and it is time for a test drive.
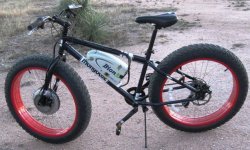
Now I know that a test drive at 2am with no lights except the moon, on broken ground, is a dumb idea but still. I sit back and look at each connection and control to make sure I haven’t done anything incredibly dumb, I remind myself that I have only one brake and not a good one at that. I turn the system on, watch it initialize, mount, and set off for a half mile loop around the upper end of the property. Some good hard pedaling to get it moving and then on throttle at a speed of only 7-8 mph around the property and back to the garage. I have survived, shut everything down, set it on the charger, and off to bed.
In school, when we had a tough problem, a couple of us used to use a simple technique. We would study the hell out of the problem and then go to bed and wake up with the answer. It worked consistently enough to be useful. I woke up the next morning remembering that I had a 20 inch extension cable for the Bionx Battery to Motor cable. Putting that on allowed me to turn the battery around and put it into its “proper” orientation. I can install and remove the battery safely and relatively conveniently and each bounce in the road will tend to tighten the battery in the mount and connector. The cable routing is a little awkward, but workable and it keeps the cabling away from the ground and weeds, water, mud, sticks, cactus, and horse manure. So, with the configuration more or less settled, it is time to take this out on the nice flat rural paved road and see how it does. The first leg is upwind against a 20 knot wind. With good pedal effort and max throttle I run 10 or so mph, a little disappointing. A turn at the far end and I start back. When I think wow, this is pretty fast I look down and the controller and it reads 21mph downwind, not pedaling, and max throttle. But it seems faster, and I realize the motor and controller are set for a 20 inch wheel and I am actually going about 30mph. That also means the upwind leg was at about 15mph which makes me feel better. It is also MUCH too fast on a bike with a single VERY poor disc brake.
Since that first real ride I have swapped the rear disc caliper for a Unique caliper that came on the Terratrike Cruiser in 2009 (long since swapped out for BB7s. Sadly Terratrike used two “rear” calipers so I had to leave the front caliper from Mongoose on the bike. It took 4 flat washers to bring the disc attached to the motor into alignment, but the caliper is aligned and goes hard with about one third of the lever travel. With this arrangement, I have one adequate brake on the rear (Unique) and one VERY marginal brake on the front (Mongoose). They are adequate for around the property at 7-15 mph but would be pretty marginal for any place with any traffic at all. We will see it they get better with time.
Future plans: The handlebar on the Dolomite is too low, I will get an extension but that will probably mean new brake cables as well – not a bad thing. I need a good strong rear rack – recommendations compatible with Dolomite (no lugs for a rack) are solicited. I would really like to move the motor to the back wheel, it is a steel frame. Does anyone know if it is REALLY safe to bend the rear end from 175mm down to 135mm ? Maybe someday I will put a small geared motor on the rear and get better performance at the low speeds I tend to run around the property. The battery seems adequate for the moment, but it is fall and I am pedaling pretty hard. High summer may be different when I REALLY don’t want to pedal hard in the AZ sunshine. This Bionx battery is already tapped and I can add 10s RC LIPO for the cost of the batteries.
Summary. The Mongoose Dolomite is a lot of bike for the money. Other than getting a bike by mail and the associated problems I have been well pleased with the bike with the exception of the brakes which, on my bike, are bad enough to warrant immediate replacement. The other components are serviceable and despite being low end components, they seem to work well. I am particularly pleased that the low end derailleur is working very competently.
The bike, as is, is doing the job I wanted done. I can run around the property quickly and efficiently and without having to borrow a golf cart. I am carrying tools, etc in a junk backpack until I choose a rear rack and paniers. That needs to be done soon, before I take a spill with a backpack with pipe wrench hammer, hacksaw and assorted pliers and screwdrivers.
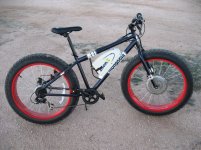
First, what is the purpose of the bike?
Simply put, it is a cheap “alternative” golf cart. We live on 20+ acres scattered across a small rural paved road East of Tucson, AZ. It is a LONG walk from corner to corner of the property and for some reason, problems with the water system or the fencing NEVER happen anywhere near the houses or the garage. My wife and daughter have personal golf carts to move around the property with hay, feed, horses, etc. When they are available, those golf carts are just PERFECT for moving tools and etc. from job to job around the property. But they are not always available and they won’t go everywhere they need to go.
While I would love to have a golf cart, a good used one runs ~$2000 and that is just more than I want to pay for the privilege of not having to carry tools around on foot. I tried my bikes but many of the golf cart paths around the property are 4 inch deep sand. My Terratrike Cruiser does pretty well but bogs down in the sand and my Trek Valencia+ is simply a death trap on sand deeper than half an inch. So the list of requirements for the bike begins to take shape: able to go anywhere on the property, be workable for me, an old fat e-bike kinda guy and be CHEAP.
A couple of years ago I started seeing the fat bikes here and there and read that they were MUCH better at sand and snow (snow is NOT my problem). I resisted for two years but finally succumbed to the urge to buy a cheap fat bike and see whether that would work around the property. I ordered the Mongoose Dolomite from Amazon for $234 delivered.
So, first, the bike. The first Dolomite arrived within 36 hours of my order. It came in one HEAVY cardboard box, but the box looked pretty good – hope springs eternal. I unpacked it and tried to fit the front wheel --- not a chance in hell that wheel was going onto the bike. The front brake disc was wildly out of line with the caliper installed on the front fork. Not a problem, just took the caliper off and mounted the wheel. With the wheel properly mounted it should be a simple task to remount and adjust the front caliper and off we go. This was not to be. With the caliper adjustment screws full loose so that the caliper can float in the mount, it is not even nearly possible to mount the caliper to the provided mounting lug. It is so misaligned that the mount itself, with NO caliper attached cannot be mounted because it interferes with the disc. Convinced that the mounting lug is in the wrong place on the fork, or that the mounting lug is badly bent, I stand in front of the bike and look at the symmetry or rather asymmetry of the front fork. The problem turns out to be that the front fork is bent. The right side angles slightly in and the left side angles slightly out. If I had to pay return shipping on the bike I would probably have straightened the fork, but I am annoyed and I don’t have to pay shipping so I order a replacement from Amazon. It arrives within 24 hours (it is just coming from Phoenix, but that is still FAST free shipping – I LOVE Amazon).
I unpack the replacement bike and assemble it. At least it fits together. I leave it upside down and check out the rotation of the wheels and the function of the low-end Shimano derailleur. The wheels are stiff even with the brake calipers backed all the way out. Shockingly, the derailleur is properly adjusted, but the rear wheel is more than half an inch out of true. Not a problem, at this point I have two Dolomites in the garage and I simply swap the rear wheels. This wheel is stiff too, but it does run true. So I check over the rest of the bike. Front sprocket is true and the chain line is good, the various cables are relatively low quality, but not kinked anywhere, the brake levers are low end but sort of OK, the headset turns smoothly and is properly adjusted, the bottom bracket turns smoothly and is also apparently properly adjusted … OK, it’s a bike. I pack up the other bike and call Amazon who arrange a UPS pickup for the returned bike (at no cost).
So now I have a Mongoose Dolomite. I inflate the tires to 15psi and try it out on the road. It rolls along OK, it is HEAVY to pedal and would be tiring to ride for more than a couple of miles even on level ground, sort of like riding upwind all the time in a good 20 knot wind. And the brakes are TERRIBLE – OH well, I can adjust those. Back to the garage to pull the wheels, grease the wheel bearings and readjust the bearing tension. That makes the wheels run much more freely. On to the brakes. They are low end by ANY definition, but they can be adjusted. The rear brake needs two flat washers on each mounting screw to get it properly aligned with the disc, but the adjustment of the stationary pad is simple and easy and with a minimal gap, I lock the brakes and tighten the 6mm adjusting screws. The disk is almost true and some thumb pressure fixes that. Now the brakes run true without contact with the disc and pull tight with less than one third of the total lever movement. The front brake needs no washers and comes into adjustment quickly, again running freely and coming hard closed with less than a third of the travel of the lever.
Back out on the road, I ride the bike for 4 miles or so. It rolls MUCH better and I could ride this around the neighborhood if I had to, but it certainly wouldn’t be my first choice. But then again, it wasn’t bought to run on the road, it was bought to run down in the sand and weeds. So I take the bike down in the sand and weeds. It rolls through deep loose sand without much trouble. It gets harder to peddle, but the wheels stay on track and there is no feeling of imminent death from having the front wheel wander off in some unexpected direction. This is kind of fun. A sort-of off-road bike … a no-track ride through the weeds and grass on a gently sloping downgrade to the back of the property down by I-10. And therein is the problem. The return trip through sand, grass, weeds, etc. is not a lot of fun even in the lowest gear. Either I need a lower gear, OR A MOTOR.
A little while on Google nets me a few alternatives for motorizing a Fat bike but It is going to be a $500 adventure when the cost of a battery is included and now I am getting into junk golf cart territory.
But as it happens, I have an old retired 2009 vintage I2C Bionx G1 SL350 system in the garage. The battery and control system have gotten “eccentric” over time but this system has the advantage that it is FREE. Now, of course there is little or no chance of putting it on the rear wheel, at least not quickly. The rear dropouts on the Dolomite are reported to be 175mm. 40mm is a LONG way to bend the frame and it will certainly screw up the chain line. But the front is 135mm and the Bionx could fit there … and the old G1 (I2C) system has a throttle. So I can put this on as a front wheel throttle only system … maybe. The mounting of the battery and the wiring to the front wheel are going to be a sticky problem but a quick dry fit says I can probably make it work. What a sad use for a Bionx system, but it is free and maybe later the back wheel, we’ll see.
I need the old Bionx motor moved from a 20 inch wheel into the 26x4 inch rim from the Dolomite. I might even spring for a better rim and I will need a shop to lace it up – That is gonna run ~$100 with the better rim and it is the week before the Tour de Tucson. I know better than to show up in a bike shop the week before the Tour, everybody and his brother are in the bike shop trying to get the bike they ride once a year tuned up for the Tour.
So maybe I could lace it myself if I had the spokes. Well ebikes.ca has a spoke calculator. We don’t say it nearly often enough, but thank you guys for all you do for our community. So I sit down at the spoke calculator and discover to my delight that it has the Bionx PL350 as one of the hub choices. The calculator then wants something called ERD – back to Google and out to measure the Dolomite rim. Back to the calculator and a 1-cross pattern is going to need 176mm spokes. Wait, don’t I have a set of spokes from the Bionx that moved from a 26 inch rim to a 20 inch rim for the Terratrike ??? But that was a double walled rim, there is NO way they are going to fit. But with a no-cross pattern … maybe. That would take a 166mm spoke. Back out to search the garage for those spokes … and they are 170mm … so close but …
So I am sitting at the spoke calculator dejectedly looking at the no-cross pattern when I realize there is no spoke angle AT ALL because the Dolomite rims have two offset rows of spoke holes. That pattern would be DEAD SOFT side to side in the front fork … not good, especially on broken ground even riding slowly. Then I see there is an option to “swap” the spokes (that is, the spokes from the left side of the hub go to the spoke holes on the right side of the rim). What the hell, can’t hurt to try… the required spoke is 169mm and there is some spoke angle to firm up the wheel side to side, and with the errors I have certainly made in measuring/calculating ERD, 169mm is close enough to 170mm that it might be worth trying. And besides, even if I fail miserably, I still needed to take the two wheels apart to show up at the bike shop with motor and rim the week AFTER the Tour de Tucson is over. So, let me be honest, I have never actually considered building a wheel. I have tried with some success to true a slightly warped wheel and that is the sum total of my wheel building experience.
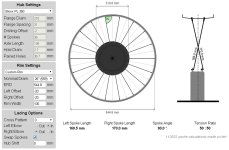
So, back to Google and friends for a lesson in building a wheel. So I find a tutorial at http://www.ebikes.ca/learn/wheel-build.html and a step by step at http://www.electricbike.com/lace-hub-motor . Thank all you folks again for helping our community. With these references in hand I start to take apart the Dolomite front wheel. The tire and tube come off easily but the rubber rim band is glued down tightly enough that it is a PIG to take off. If I weren’t rebuilding the wheel this would probably please me. In any case, I get it off intact. The Bionx motor comes right out of the 20 inch wheel and I move on to building the Bionx motor into the Dolomite rim.
I put each spoke in with 4 initial turns of the nipple and when the pattern is complete, the wheel is VERY loose. Now I am a little worried, but I go around tightening each spoke one full turn. I do this several times and it is amazing how quickly the wheel tightens up. When the wheel begins to look and feel sort of like a wheel I put it in the front fork to true it up. Low and behold it is pretty much true – actually a little better than it was before I took it apart. Now I am pretty sure this is because the Dolomite rim is so wide that it is pretty darn rigid and is just ignoring whatever wheel-building mistakes I have made. I expect that those mistakes will become obvious over time, hopefully with non-fatal results. The spokes still feel too loose and I make two more rounds tightening each spoke one half turn. At that point, the wheel is still pretty darn true and the spokes are getting to be pretty much flush with the top of the nipple. I decide that the spokes are probably more uniform than my wheel building and tighten each spoke once again until it is just flush with the top of the nipple. Once again the wheel is true within a sixteenth of an inch or so, and the spokes seem adequately tight (but not by much). This is working out well enough to make me nervous (whom the Gods would destroy they first make proud).
View attachment 2
So, I mount the wheel (with disc) to the front fork, but I have to remove the disc brake caliper to do this. I tie the caliper out of the way and make a mental note to go VERY slowly until I have that problem fixed. I sit back and decide how to mount the battery bracket and the controller. If I mount the battery bracket with the output wiring facing forward, the big end of the battery faces the small end of my triangle. It fits but JUST barely, in fact, with the battery mounted like that, the battery is VERY difficult to put in and take out and every bounce in the road will be trying to remove the battery from the bracket and connector … NOT a good solution, but good enough for 1am. I plan to put the controller (with throttle paddle) on the right hand side but that interferes with the Shimano twist shifter. I refuse to put the throttle on the left hand side. Both my other bikes have the throttle on the right and so is this one going to. Off come the grips, the brake levers and the Shimano twist shifter. Mongoose has left me enough slack in the cables that all of this works and it makes the bike controls the same as the Prodeco Phantom that my son now rides. That was my first e-bike and I always liked having the twist shifter on the left and the thumb throttle on the right. So at 2am, everything is in place and it is time for a test drive.
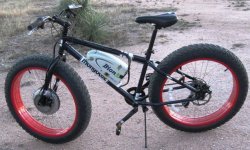
Now I know that a test drive at 2am with no lights except the moon, on broken ground, is a dumb idea but still. I sit back and look at each connection and control to make sure I haven’t done anything incredibly dumb, I remind myself that I have only one brake and not a good one at that. I turn the system on, watch it initialize, mount, and set off for a half mile loop around the upper end of the property. Some good hard pedaling to get it moving and then on throttle at a speed of only 7-8 mph around the property and back to the garage. I have survived, shut everything down, set it on the charger, and off to bed.
In school, when we had a tough problem, a couple of us used to use a simple technique. We would study the hell out of the problem and then go to bed and wake up with the answer. It worked consistently enough to be useful. I woke up the next morning remembering that I had a 20 inch extension cable for the Bionx Battery to Motor cable. Putting that on allowed me to turn the battery around and put it into its “proper” orientation. I can install and remove the battery safely and relatively conveniently and each bounce in the road will tend to tighten the battery in the mount and connector. The cable routing is a little awkward, but workable and it keeps the cabling away from the ground and weeds, water, mud, sticks, cactus, and horse manure. So, with the configuration more or less settled, it is time to take this out on the nice flat rural paved road and see how it does. The first leg is upwind against a 20 knot wind. With good pedal effort and max throttle I run 10 or so mph, a little disappointing. A turn at the far end and I start back. When I think wow, this is pretty fast I look down and the controller and it reads 21mph downwind, not pedaling, and max throttle. But it seems faster, and I realize the motor and controller are set for a 20 inch wheel and I am actually going about 30mph. That also means the upwind leg was at about 15mph which makes me feel better. It is also MUCH too fast on a bike with a single VERY poor disc brake.
Since that first real ride I have swapped the rear disc caliper for a Unique caliper that came on the Terratrike Cruiser in 2009 (long since swapped out for BB7s. Sadly Terratrike used two “rear” calipers so I had to leave the front caliper from Mongoose on the bike. It took 4 flat washers to bring the disc attached to the motor into alignment, but the caliper is aligned and goes hard with about one third of the lever travel. With this arrangement, I have one adequate brake on the rear (Unique) and one VERY marginal brake on the front (Mongoose). They are adequate for around the property at 7-15 mph but would be pretty marginal for any place with any traffic at all. We will see it they get better with time.
Future plans: The handlebar on the Dolomite is too low, I will get an extension but that will probably mean new brake cables as well – not a bad thing. I need a good strong rear rack – recommendations compatible with Dolomite (no lugs for a rack) are solicited. I would really like to move the motor to the back wheel, it is a steel frame. Does anyone know if it is REALLY safe to bend the rear end from 175mm down to 135mm ? Maybe someday I will put a small geared motor on the rear and get better performance at the low speeds I tend to run around the property. The battery seems adequate for the moment, but it is fall and I am pedaling pretty hard. High summer may be different when I REALLY don’t want to pedal hard in the AZ sunshine. This Bionx battery is already tapped and I can add 10s RC LIPO for the cost of the batteries.
Summary. The Mongoose Dolomite is a lot of bike for the money. Other than getting a bike by mail and the associated problems I have been well pleased with the bike with the exception of the brakes which, on my bike, are bad enough to warrant immediate replacement. The other components are serviceable and despite being low end components, they seem to work well. I am particularly pleased that the low end derailleur is working very competently.
The bike, as is, is doing the job I wanted done. I can run around the property quickly and efficiently and without having to borrow a golf cart. I am carrying tools, etc in a junk backpack until I choose a rear rack and paniers. That needs to be done soon, before I take a spill with a backpack with pipe wrench hammer, hacksaw and assorted pliers and screwdrivers.