SplinterOz
1 kW
sparkvark, thanks.
There is a noise from the bearings at about 3000rpm, even with the motor free. You can hear this more as the motor winds down due to the fact I accelerated through this range quickly so as it wouldn't stay that way under load.
I agree that these bearings may not be the best and I am going to replace all 5 in the motor over the next week or so.
Here is the internal setup of the motor: note the two sets of two bearings on the shaft and the one bearing for the skirt.
I am thinking of roller bearings for the shaft (maybe even one to replace each pair) if I can get them the right size.
Opinions welcome.
There is a noise from the bearings at about 3000rpm, even with the motor free. You can hear this more as the motor winds down due to the fact I accelerated through this range quickly so as it wouldn't stay that way under load.
I agree that these bearings may not be the best and I am going to replace all 5 in the motor over the next week or so.
Here is the internal setup of the motor: note the two sets of two bearings on the shaft and the one bearing for the skirt.
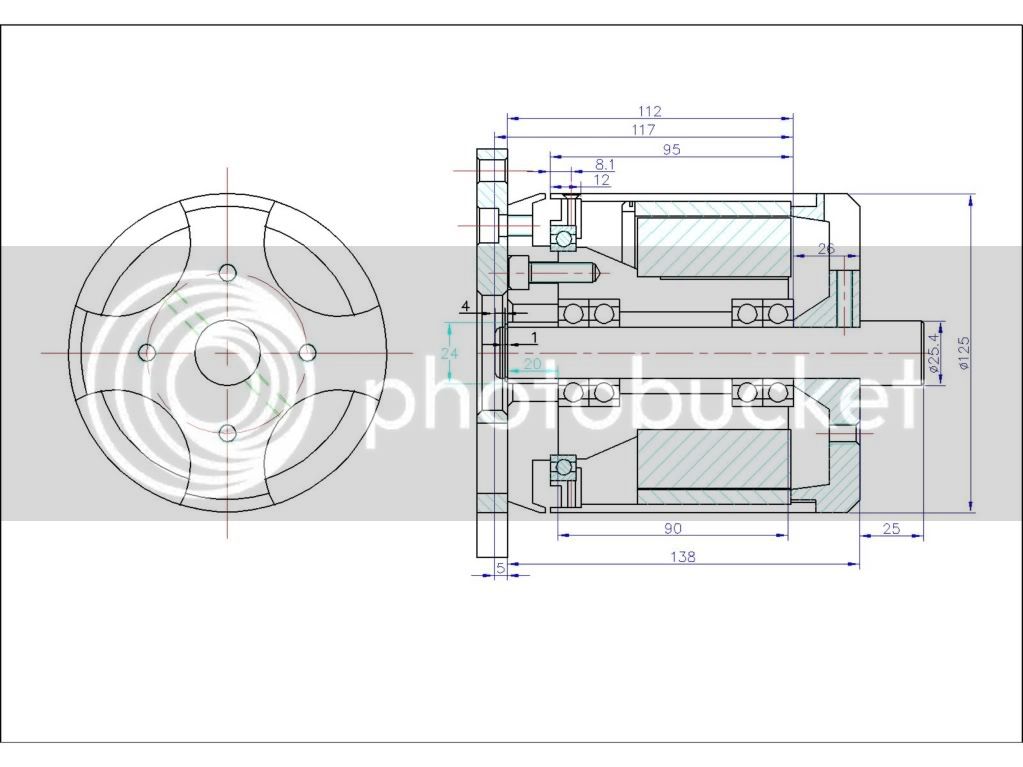
I am thinking of roller bearings for the shaft (maybe even one to replace each pair) if I can get them the right size.
Opinions welcome.