molybdenum
1 kW
Silly of me to select the wrong motor in the sim
Definitely apples and oranges...
Here's the sim comparing the two MG310 motors under my anticipated running parameters.
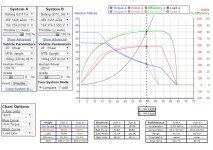
I am wondering about the differences in predicted final temps. Is this the slight difference in efficiency? Ideally I would have a motor which spins at 9 RPM/V; as the STD is a bit too slow and the FST is a bit too quick.
Also, for the purposes of the sim, I set wheel size to 26". I am running a 700c wheel, but with 35c tires. My wheel circumference works out to 2205 mm, which is nearly identical to that of a 26" wheel with 2.25" mountain bike tire. I'm assuming that the 26" wheel best fits my actual wheel size and hope this is correct. I would like to see the option of setting actual wheel circumferences in the sim, as this detail is very important and impossible to get right otherwise.

Here's the sim comparing the two MG310 motors under my anticipated running parameters.
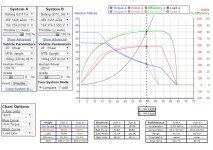
I am wondering about the differences in predicted final temps. Is this the slight difference in efficiency? Ideally I would have a motor which spins at 9 RPM/V; as the STD is a bit too slow and the FST is a bit too quick.
Also, for the purposes of the sim, I set wheel size to 26". I am running a 700c wheel, but with 35c tires. My wheel circumference works out to 2205 mm, which is nearly identical to that of a 26" wheel with 2.25" mountain bike tire. I'm assuming that the 26" wheel best fits my actual wheel size and hope this is correct. I would like to see the option of setting actual wheel circumferences in the sim, as this detail is very important and impossible to get right otherwise.