Thanks, I kept both windings, I figured the thicker wire winding is the one I needed.
Do I have to pay attention to the way the windings wrap? and do the same with the added welding cable wrap?
At Princess Auto (Like USA's Harbor Freight) all they had was 0, 00, 1, 2, 4, 6. Ideally I wanted 3awg, I was 50/50 whether to buy 2 or 4awg. I ended up buying 2awg and its huge. I think I made a mistake, hopefully I can return the welding cable and buy 4awg, but only if its necessary to get more wraps. The only other wire I got on hand is 8AWG.
What do you guys think?
I can only get about two turns, I think ideally I need 3 turns, from what I gather
from this website
Use a flexible 3AWG / 25mm2 welding cable with a length of 140cm, this allows 3 windings. I have examined if a thicker cable give a higher weld current, this was not the case. The weld current is limited by the transformer itself.
but if your 1.5 tuns works then my 2 should be fine.
I am using a timer, from the avdweb.nl website. Its all ready to go.
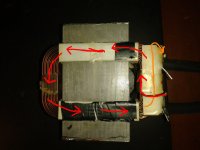
I will epoxy on the top and clamp it over-night.