itchynackers
100 kW
Background:
I purchased a 9c 8x8 rear motor with the group buy a few months ago. I've ridden about 900 miles on it thus far with zero problems. Wednesday I was 10 miles into my casual ride when the motor just shut down. There wasn't any warning, shuddering, nothing. Sooo, after pedaling my arse back home (oh the agony).
Bike specs when fault occured:
100.1V, 12ah lipo battery
3-speed switch on #1 which is 42% speed, however I was at part throttle cruising on the sidewalk at about 12mph, level surface.
18 fet lyen controller (4115 fets)
9c 8x8 rear disc motor upgraded with 12awg teflon phase wires.
I began to troubleshoot.
LVC in controller?
I had just reprogrammed my controller, so I thought maybe I had a wrong setting. I charged the batts back up. Still no response.
Conclusion: not the LVC.
Bad throttle?
I hooked up the throttle from my other ebike to the faulty bike. Same result...no power.
Conclusion: Probably not the throttle.
Bad controller?
I hooked up the controller to my other ebike. Bike works.
Conclusion: Not the controller.
Bad wiring connection?
I tested wiring connections with an l.e.d. light to see if there was a break somewhere. Lights worked fine.
Conclusion: Probably not a bad connection.
Motor?
I tested each wire (halls and phase) for breaks with the l.e.d. light. Couldn't find any problems. In fact, when I pulled both covers off, the motor looked, and smelled, brand-new. On the hall side of the motor, I noticed something strange. There is a little circuit board connected to the 3 halls. On that board there appears to be some scorch marks (see pics below). Hopefully that is my problem. Now, what to do next to fix it?
Scorched board with blackened zip tie...
Zip tie removed...
Close-up of board...
Help!!! What to do?
I purchased a 9c 8x8 rear motor with the group buy a few months ago. I've ridden about 900 miles on it thus far with zero problems. Wednesday I was 10 miles into my casual ride when the motor just shut down. There wasn't any warning, shuddering, nothing. Sooo, after pedaling my arse back home (oh the agony).
Bike specs when fault occured:
100.1V, 12ah lipo battery
3-speed switch on #1 which is 42% speed, however I was at part throttle cruising on the sidewalk at about 12mph, level surface.
18 fet lyen controller (4115 fets)
9c 8x8 rear disc motor upgraded with 12awg teflon phase wires.
I began to troubleshoot.
LVC in controller?
I had just reprogrammed my controller, so I thought maybe I had a wrong setting. I charged the batts back up. Still no response.
Conclusion: not the LVC.
Bad throttle?
I hooked up the throttle from my other ebike to the faulty bike. Same result...no power.
Conclusion: Probably not the throttle.
Bad controller?
I hooked up the controller to my other ebike. Bike works.
Conclusion: Not the controller.
Bad wiring connection?
I tested wiring connections with an l.e.d. light to see if there was a break somewhere. Lights worked fine.
Conclusion: Probably not a bad connection.
Motor?
I tested each wire (halls and phase) for breaks with the l.e.d. light. Couldn't find any problems. In fact, when I pulled both covers off, the motor looked, and smelled, brand-new. On the hall side of the motor, I noticed something strange. There is a little circuit board connected to the 3 halls. On that board there appears to be some scorch marks (see pics below). Hopefully that is my problem. Now, what to do next to fix it?
Scorched board with blackened zip tie...
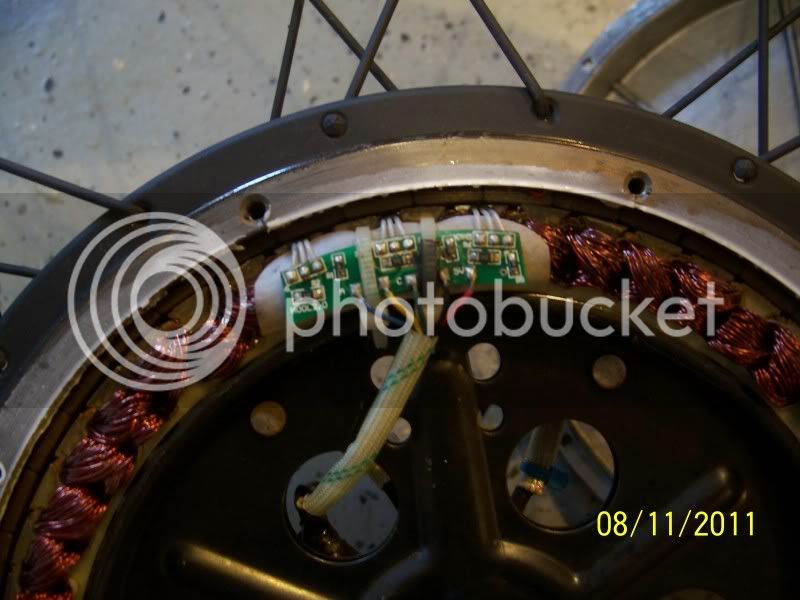
Zip tie removed...
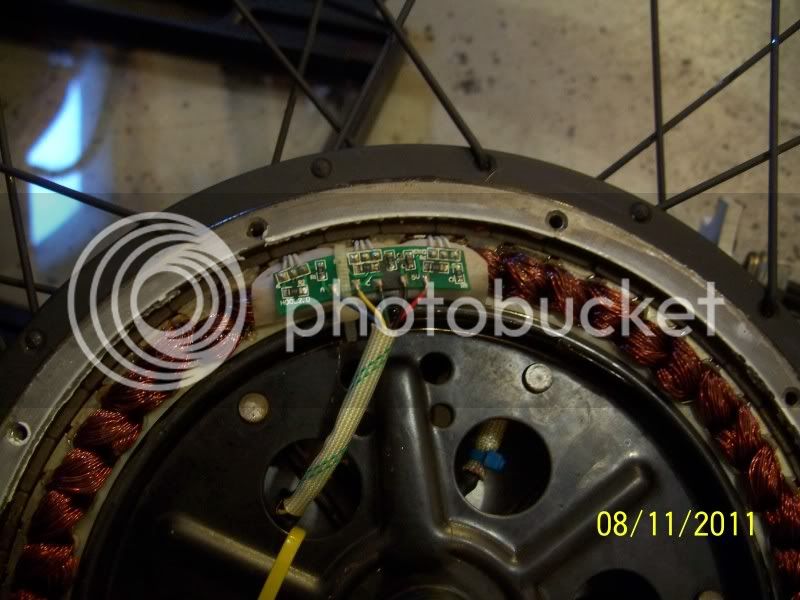
Close-up of board...
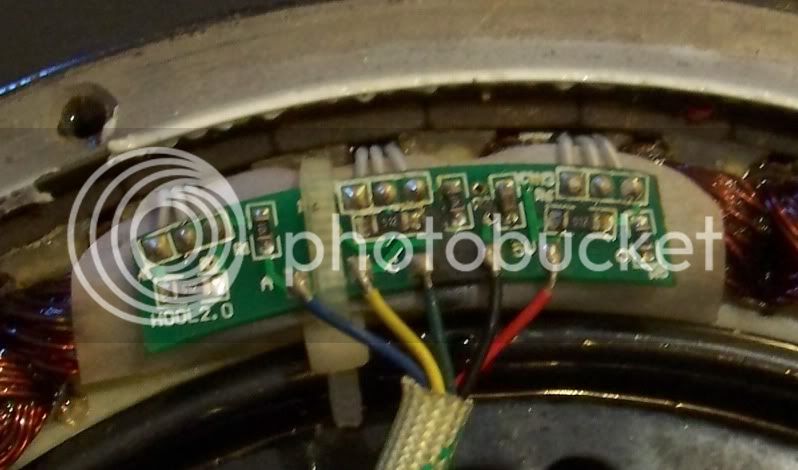
Help!!! What to do?