Matt, thanks for the kudos, Stay tuned
Triton, that is a great product. Apparently they are not readily available in the US for some reason, but I am thinking about importing a bunch. BTW, if anyone cares, I bought my "WenteQ lead weight clamps" from ebay seller "4raceparts" who offers them in 1.25" (32mm), 1.5" and and 1.75" flavors.
http://cgi.ebay.com/ebaymotors/ws/eBayISAPI.dll?ViewItem&item=360266264657
John, I liked the idea of that location but my crude attempts were knee banging agony and awkwardness. With your skills, I am sure you crafted something much better.
OTOH, I like the feel of having the weight on the fork, the mass it acts as a steering damper. I expected to feel it exaggerating my motions, but it really just feels solid. I'd be unhappy if it felt like a basketful of loose groceries, I don't think I would like it if the mass could move around, and "bump steer". This just feels solid, like a nice german car. The pack gets the softest ride up there, plus I like to tell myself that with the stanchions taking the weight of the batts there is less pressure on the head tube (whether or not its true

).
The 15s3p a123 pack I originally built for this bike ended up on the back of a bike I built for my wife, which is featuring a rear Bafang you (John) built for me long ago. That motor left for Australia, never made it, and at long last ended up on this bike. Anyhow this bike is going to get the same treatment, using the smallest of the three ammo boxes below. I am also going to bolt the controller to her ammo box, and just run big phase wires and halls back to the motor. Everything else is local to the new controller location, throttle, CA, brake wires. I haven't figured out the best position for it though, it would be sweet if I could mount it between the box and the head tube but I don't think it will fit. I got a matched set of wheels using the DX-32 rim, 32 holes like, and put the front one on her bike. I had to get a centerlock Disk for it, 1st time on that hardware, I was glad to see it worked fit OK with my Avid BB-7 brakes.
View attachment 3
The middle ammo box is the same size as the one on the bike from this thread, and the large one is going to hold the (28s)100v/16ah pack of the a123 prisimatics. That one will have 6 clamps though.
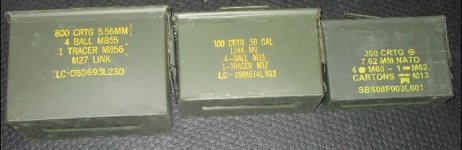
The front wheel on the BMC V3 bike is also a JohnRobHolmes creation. Hey John can you source that DX32 rim? I am thinking about getting another front wheel made...