Drum
100 W
Ok, I have found ( or manufactured) another hour of usually non-existant spare time, so the real build has begun. Real life is demanding, and does not leave me many minutes per week of project time, so this build may not be the quickest on record!
This is one of the reasons I have decided that things will be done in the quickest reasonable way rather than the best way, if the best way would take significantly longer. The other reason is that so often when a project is finished, you realise that there was a better way of doing part of it, or that it would have been better if one thing was longer / shorter / different to how you did it the first time. If you have invested a lot of time and effort making something beautifully, you don't tend to change it, but if you have put something together "quick & easy", it is easier to convince yourself to put in the effort to improve it.
If it turns out great anyway, then you have more time to put into other things, and you are riding it sooner..
1) Cut and machined the ends of the four pieces of 304 stainless steel box section that make up the main rails of the new swingarm, 40 x 20 x 1.5mm wall thickness. Machining the ends in the mill may seem like overkill, but is in fact quick and easy, and there is no doubt that the ends are square and straight.
Why stainless? Most people avoid stainless because they believe that it is expensive, and that it is hard to work with.
Well, it is not as cheap as mild steel, but if you add the cost of the steel and the paint together on a project this size, it comes to more than the cost of the stainless, and the stainless item is made quicker because there is no "painting time". Yes, it is a bit harder to work with if you only have "home handyman" tools, but with good equipment available there is not much difference.
The "best practice" swingarm would be triangulated and made of chrome-moly steel DOM tube. It would cost more and take ten times as long to make, and modifying it later would be much more difficult.
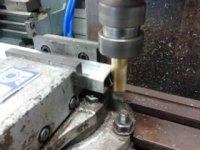
2) Clamped the pieces to the side of a larger piece of SS box section as a welding jig. You can see that the entire weld area is accessible while still clamped to the bigger box, and it is easy and quick to reposition the box in the vise so all welds can be done in the easiest position.
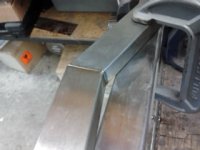
3) There was nobody around to take a photo while I was applying the electric hot-melt, but it was done with a DC TIG welder on about 55 amps and pure Argon shielding gas. With a sharp tungsten, 55 amps gets good penetration and requires you to move quickly to avoid blowing a hole, but gives a smooth surface finish and (in my experience anyway) less distortion than welding on lower current and taking longer.
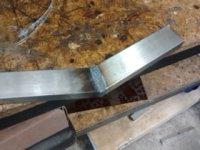
4) Back axle brackets were started. Two pieces of 40 x 40 x 3 stainless angle were cut at 41mm long. One leg was cut off at 21mm width and the long faces tack welded together. They were squared off and sized to 40 x 20 in the mill, and the 12mm hole (for the 12mm through axle of the back wheel) was drilled. In this way I know that even if the hole position is not perfect, at least both sides will be perfectly aligned to each other. Angle braces top and bottom are still to be welded on before these are welded to the box section.
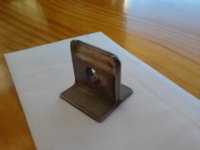
I will update again when I have found a bit more time to make more progress...
This is one of the reasons I have decided that things will be done in the quickest reasonable way rather than the best way, if the best way would take significantly longer. The other reason is that so often when a project is finished, you realise that there was a better way of doing part of it, or that it would have been better if one thing was longer / shorter / different to how you did it the first time. If you have invested a lot of time and effort making something beautifully, you don't tend to change it, but if you have put something together "quick & easy", it is easier to convince yourself to put in the effort to improve it.
If it turns out great anyway, then you have more time to put into other things, and you are riding it sooner..
1) Cut and machined the ends of the four pieces of 304 stainless steel box section that make up the main rails of the new swingarm, 40 x 20 x 1.5mm wall thickness. Machining the ends in the mill may seem like overkill, but is in fact quick and easy, and there is no doubt that the ends are square and straight.
Why stainless? Most people avoid stainless because they believe that it is expensive, and that it is hard to work with.
Well, it is not as cheap as mild steel, but if you add the cost of the steel and the paint together on a project this size, it comes to more than the cost of the stainless, and the stainless item is made quicker because there is no "painting time". Yes, it is a bit harder to work with if you only have "home handyman" tools, but with good equipment available there is not much difference.
The "best practice" swingarm would be triangulated and made of chrome-moly steel DOM tube. It would cost more and take ten times as long to make, and modifying it later would be much more difficult.
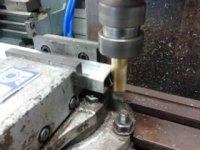
2) Clamped the pieces to the side of a larger piece of SS box section as a welding jig. You can see that the entire weld area is accessible while still clamped to the bigger box, and it is easy and quick to reposition the box in the vise so all welds can be done in the easiest position.
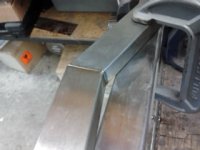
3) There was nobody around to take a photo while I was applying the electric hot-melt, but it was done with a DC TIG welder on about 55 amps and pure Argon shielding gas. With a sharp tungsten, 55 amps gets good penetration and requires you to move quickly to avoid blowing a hole, but gives a smooth surface finish and (in my experience anyway) less distortion than welding on lower current and taking longer.
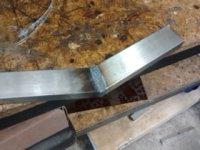
4) Back axle brackets were started. Two pieces of 40 x 40 x 3 stainless angle were cut at 41mm long. One leg was cut off at 21mm width and the long faces tack welded together. They were squared off and sized to 40 x 20 in the mill, and the 12mm hole (for the 12mm through axle of the back wheel) was drilled. In this way I know that even if the hole position is not perfect, at least both sides will be perfectly aligned to each other. Angle braces top and bottom are still to be welded on before these are welded to the box section.
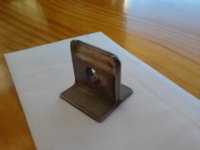
I will update again when I have found a bit more time to make more progress...