winzEracer
10 mW
- Joined
- Jun 1, 2012
- Messages
- 32
Hello,
I have been building a modular battery box for my eKart, and as the design has progressed I feel that it is something that is easily replicated by others for karts, atvs, and motorcycles. A bit over kill for an ebike though.
A little about the pack, I am building a 36s5p pack with Turnigy Nano-tech 6s 35-70C bricks. Two of the below described modules make up the 36s5p pack. My first design I tried to use bullet connectors and I made bussbars like the one that Jozzer sells on his site with the bullet connectors sticking out of a block of copper. I found that this was hard to electrically insulate (without making it look like a pile of scat!) and due to the mechanical configuartion of the pack was hard to service. So I did a major redesign from the ground up and came up with this modular scalable design.
Here is a screen shot of the design, describes its basic shape and configuration.
View attachment 7
After the model, I decided to use Blue Sea Systems 150 amp continuous bus bars which cost about $20 each ( I used 3 per module) http://www.bluesea.com/products/2722/DualBus_Plus_150A_BusBar_-_1_4in-20_Stud_5_Gang, which fit well and retained a professional quality, although they are technically only rated (or tested) at 48vdc, I attached them with .125" Polypropylene "L" brackets, as seen it pics below, to make sure they were isolated well.
This change will also affect how the Anderson Connectors attach, I will most likely leave a pigtail with an Anderson connector on it.
I also cut off all bullet connectors (What a happy moment that was!) and crimped ring terminals on each of the leads from the 6s Bricks which then lands on the Blue Sea bus bars. Each bank of 6s5p will wire up to one of the dual bus bar units and I will then place series jumpers between each of the Blue Sea units, one of the series jumpers will have a fuse inline for short circuit protection inside the module, a friend of mine does this in his electric drag racing car and recommended it. And since I watched a very expensive pack start on fire because of a dead short (and this fuse would have saved the pack) last week I think I will add this feature.
I designed the delrin spacers and had them laser cut which is really affordable these days. I had 6 pcs cut for $95.00 at Serra Laser in Anahiem CA. Delrin (Acetal Resin) was purchased from McMaster-Carr and was about $50 or so. Attached are the DXF files it anyone wants them, be sure to check all dimensions yourself as they may be different from your battery of choice.
The Aluminium Box is made out of 5052 Aluminium and welded up at a local welding shop. Total cost for 2 boxes with material was about $220, nothing to special here.
BMS is Methods HVC/LVC as shown it Pics, to bad he is out of the scene now, I wish someone would copy the design and sell 'em around here...
I am not finished with construction however here are up to date pics, I will post again when the pack is further along.
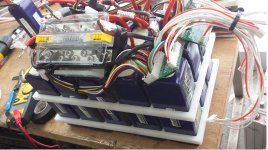
View attachment 4
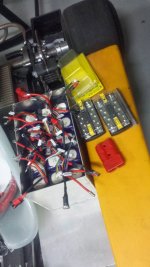
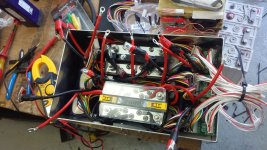
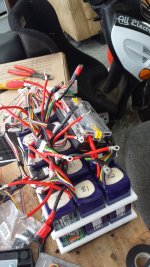
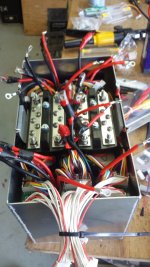
More Pics here http://winzeracer.com/photos.html
Thanks,
Brock
I have been building a modular battery box for my eKart, and as the design has progressed I feel that it is something that is easily replicated by others for karts, atvs, and motorcycles. A bit over kill for an ebike though.
A little about the pack, I am building a 36s5p pack with Turnigy Nano-tech 6s 35-70C bricks. Two of the below described modules make up the 36s5p pack. My first design I tried to use bullet connectors and I made bussbars like the one that Jozzer sells on his site with the bullet connectors sticking out of a block of copper. I found that this was hard to electrically insulate (without making it look like a pile of scat!) and due to the mechanical configuartion of the pack was hard to service. So I did a major redesign from the ground up and came up with this modular scalable design.
Here is a screen shot of the design, describes its basic shape and configuration.
View attachment 7
After the model, I decided to use Blue Sea Systems 150 amp continuous bus bars which cost about $20 each ( I used 3 per module) http://www.bluesea.com/products/2722/DualBus_Plus_150A_BusBar_-_1_4in-20_Stud_5_Gang, which fit well and retained a professional quality, although they are technically only rated (or tested) at 48vdc, I attached them with .125" Polypropylene "L" brackets, as seen it pics below, to make sure they were isolated well.
This change will also affect how the Anderson Connectors attach, I will most likely leave a pigtail with an Anderson connector on it.
I also cut off all bullet connectors (What a happy moment that was!) and crimped ring terminals on each of the leads from the 6s Bricks which then lands on the Blue Sea bus bars. Each bank of 6s5p will wire up to one of the dual bus bar units and I will then place series jumpers between each of the Blue Sea units, one of the series jumpers will have a fuse inline for short circuit protection inside the module, a friend of mine does this in his electric drag racing car and recommended it. And since I watched a very expensive pack start on fire because of a dead short (and this fuse would have saved the pack) last week I think I will add this feature.
I designed the delrin spacers and had them laser cut which is really affordable these days. I had 6 pcs cut for $95.00 at Serra Laser in Anahiem CA. Delrin (Acetal Resin) was purchased from McMaster-Carr and was about $50 or so. Attached are the DXF files it anyone wants them, be sure to check all dimensions yourself as they may be different from your battery of choice.
The Aluminium Box is made out of 5052 Aluminium and welded up at a local welding shop. Total cost for 2 boxes with material was about $220, nothing to special here.
BMS is Methods HVC/LVC as shown it Pics, to bad he is out of the scene now, I wish someone would copy the design and sell 'em around here...
I am not finished with construction however here are up to date pics, I will post again when the pack is further along.
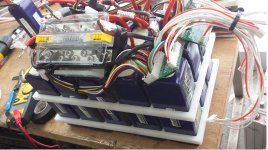
View attachment 4
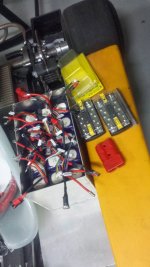
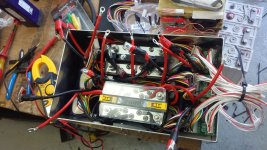
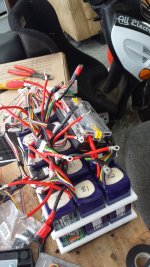
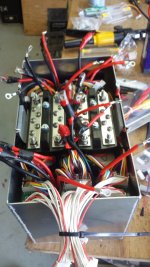
More Pics here http://winzeracer.com/photos.html
Thanks,
Brock