Russell
1 MW
My original 36V Bafang lasted 3,000 miles before a hall sensor failure and the replacement 24V GM Mini Motor core hall wiring melted after one ride and while I was able to repair the Mini I still missed the torque of the 36V motor. I thought about running it sensorless but my experiment with another GM Mini and a dual-mode controller proved to me that a freewheeling geared motor does not work well sensorless. The problem as I understand it is that for a sensorless controller to pulse the phases at the right time it first needs to see back EMF to determine where the motor is. Unfortunately a freewheeling geared motor won’t turn until power is applied to it. In practice this meant it took a very light throttle to get the Mini to launch without the halls hooked up, a little too much throttle or load and the motor would make a hammering sound. Once under way the motor would run ok unless the throttle was fully released which caused the controller to lose its position. Once again then too much throttle too quickly and the hammering returned; it was very frustrating.
The solution to running the freewheeling geared motor without hall sensors was then obvious, don’t let it freewheel! Now I know what some of you are thinking, a big advantage of a geared motor is that it freewheels…well not really. The big advantages of geared motors is that they are small and light and have excellent torque for their small size but I have found especially after I switched to 48V that I use the throttle at least 90% of the time meaning the front wheel is freewheeling maybe 10% of the time at best.
Once I was determined to make the Bafang non-freewheeling I had to figure out how it freewheeled in the first place and how to disable it. I drilled out the 3 pins holding the top cover of the gear assembly to find this;
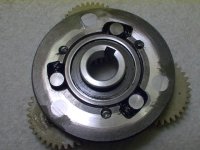
Inside the three pockets are cylindrical bearings which slide over the inner bearing with little friction and allow the wheel to freewheel. When power is applied those same hardened steel bearings are forced against the hardened steel inner bearing surface providing a strong positive lock-up. At this point the solution would have been simple if I had a welder, unfortunately I don’t nor do I know how to use one for that matter. I had never used the JB Weld products but the “cold weld†formula sounded like a solution to my problem. Perhaps my expectations were a little high but it doesn’t come close to real welding, it’s basically just a 2-part epoxy that feels like plastic when cured. Still I had little to lose. I roughed up the surfaces with a stone wheel on a dremel tool (the sparks really flew!) then applied the product to the inner bearing surfaces and slathered it on top of the assembly.
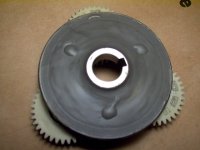
After it set-up I re-assembled the motor which was stripped of the hall wiring.
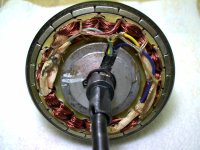
I mounted the sensored/sensorless controller from ecitypower on the seatpost, a departure from my usual handlebar mounted location. (You can check out my review of the controller here; http://endless-sphere.com/forums/viewtopic.php?f=4&t=13659 )
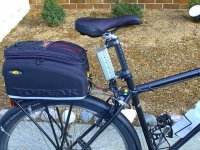
I have just three connections now; the 3-wire cable to the motor, the throttle and battery.
I didn’t have high hopes for the JB Weld kluge fix when I took the bike out today for a short 18 mile ride. The controller requires the wheel to roll forward just a bit to sync-up and it works very well. The auto-cruise function also works great. The only thing is with the Watts-Up meter in the rear bag I didn’t have the ability to monitor the current so combined with the higher controller current limit of 21A (spec’d at 22A) and the cruise control I managed to use more power than I ever have before, 16.1 Wh/mile. It was a successful experiment however I feel uneasy about relying on the epoxied gear assembly.
-R
The solution to running the freewheeling geared motor without hall sensors was then obvious, don’t let it freewheel! Now I know what some of you are thinking, a big advantage of a geared motor is that it freewheels…well not really. The big advantages of geared motors is that they are small and light and have excellent torque for their small size but I have found especially after I switched to 48V that I use the throttle at least 90% of the time meaning the front wheel is freewheeling maybe 10% of the time at best.
Once I was determined to make the Bafang non-freewheeling I had to figure out how it freewheeled in the first place and how to disable it. I drilled out the 3 pins holding the top cover of the gear assembly to find this;
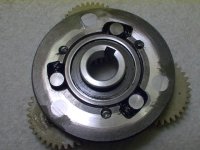
Inside the three pockets are cylindrical bearings which slide over the inner bearing with little friction and allow the wheel to freewheel. When power is applied those same hardened steel bearings are forced against the hardened steel inner bearing surface providing a strong positive lock-up. At this point the solution would have been simple if I had a welder, unfortunately I don’t nor do I know how to use one for that matter. I had never used the JB Weld products but the “cold weld†formula sounded like a solution to my problem. Perhaps my expectations were a little high but it doesn’t come close to real welding, it’s basically just a 2-part epoxy that feels like plastic when cured. Still I had little to lose. I roughed up the surfaces with a stone wheel on a dremel tool (the sparks really flew!) then applied the product to the inner bearing surfaces and slathered it on top of the assembly.
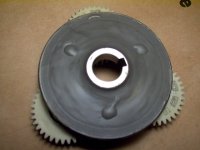
After it set-up I re-assembled the motor which was stripped of the hall wiring.
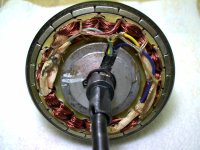
I mounted the sensored/sensorless controller from ecitypower on the seatpost, a departure from my usual handlebar mounted location. (You can check out my review of the controller here; http://endless-sphere.com/forums/viewtopic.php?f=4&t=13659 )
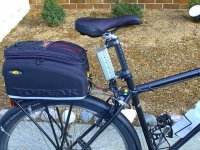
I have just three connections now; the 3-wire cable to the motor, the throttle and battery.
I didn’t have high hopes for the JB Weld kluge fix when I took the bike out today for a short 18 mile ride. The controller requires the wheel to roll forward just a bit to sync-up and it works very well. The auto-cruise function also works great. The only thing is with the Watts-Up meter in the rear bag I didn’t have the ability to monitor the current so combined with the higher controller current limit of 21A (spec’d at 22A) and the cruise control I managed to use more power than I ever have before, 16.1 Wh/mile. It was a successful experiment however I feel uneasy about relying on the epoxied gear assembly.
-R