Dui ni shuo de dui
10 kW
Had to open the motor again , now that I have an easy method to open and close the motor I kinda enjoy doing it. :lol:
This time I wanted to do the following things:
-install fresh bearings
-replace the seals
-install different temperature sensors
Getting the new seals wasn't an easy task and it ended up to be disappointing. My motor has been produced about 10 years ago and it seems like at that time QS was using MUCH better quality seals than the ones thay are using now....
I couldn't find the old seals anywhere so I had to go for the new ones, unfortunately.
The outside thickness of the seals is 7mm and that never changed, but the inside part of the seals, which is in contact with the axle and is the actual part that prevents water from getting in went from 12.5mm thick to only 7mm. The old seals were custom made for QS apparently, the new ones are standard that can be found anywhere.
Sure it is nice to be able to find seals anywhere, but I fear it will come at the price of long term reliability. The old seals obviously worked really, really well, as the pictures from the openend motor showed up. Well, anyway, nothing I can do but to use the new seals, the old ones were damaged and had to be replaced.
Old seal:
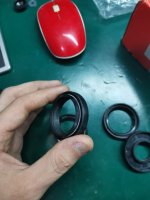
New seals:
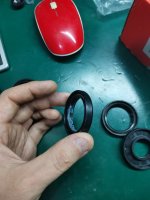
Hopefully you can see the difference on the pics
Next was to install new bearings. No particular difficulty, went smoothly. I went for hopefully good quality bearings made in France:
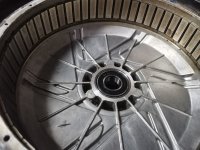
Last but not least was to install new temp sensors. I installed one last time, but it wasn't working properly. It gave me some weirdly high readings, I suppose it wasn't compatible with the Fardriver controller, I don't know.
This time I decided to use not ony one, not only two, but 3 different temperature sensors! Because why not?
This way I could make sure to get consistent results and also have redundancy.
Two of those 3 sensors are intended to be used with the controller. I can only plug one at a time of course, but this way I can compare and use the one that works best for me.
I installed a KTY84-130 and a NTC 230.
The last sensor is a lot more interesting perhaps: I bought a super cheap barbecue thermometer for a dollar:
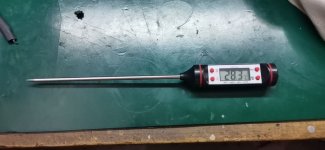
The idea was to dismantle it, install the sensor inside the motor and the display on the dash.
It has a range of -50 to 300 degee C (hopefully it will never see these temps anytime soon!!! :lol: ), a digital display and it also has a very interesting feature because it can record the lowest and highest temperatures it sees over a time period. That means I can ride for a while, then press a button and see what was the maximum temperature, no need to watch it all the time. Pretty cool!
Anyay, I had to pass two new wires for it through the motor axle, then I sticked the 3 sensors inside the coils:
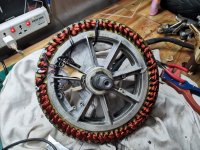
Then I had to extend the wires in order to go from the display to the rear wheel:
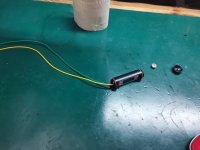
Last but not least, I had to design and print a little bracket system to hold the screen:

Finally painted it black so it wouldn't be too visible:
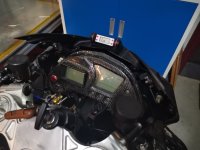
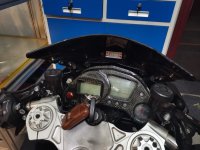
And voila, Just had to re assemble the motor and reinstall in back in place on the bike. Done.
So far from my tests everything works really well! The temperatures in the Fardriver app are very consistent to the ones I get on the dash, so that's very good news, the dash screen works well and it is indeed very practical.
I haven't got the opportunity to push the motor too much these days but after my daily trip to work it did reach a maximum of about 95 degree C. The good thing is that this goes back down very quickly once releasing the throttle, the statorade seems to work pretty well. The casing gets hot to the touch pretty much instantly, it used to be remain cold for a few minutes before.
I'm very happy with these little mods, it has been interesting to make and so far it works great!
Now I finally have a good way to monitor what's happening inside my motor and it will be possible to effectively protect it against high temperatures!
Not sure I can put a lot more amps through the phases though, it seems to get pretty hot already. I'll wait for the rain to stop to see how hot it gets during more spirited rides. :wink:
This time I wanted to do the following things:
-install fresh bearings
-replace the seals
-install different temperature sensors
Getting the new seals wasn't an easy task and it ended up to be disappointing. My motor has been produced about 10 years ago and it seems like at that time QS was using MUCH better quality seals than the ones thay are using now....
I couldn't find the old seals anywhere so I had to go for the new ones, unfortunately.
The outside thickness of the seals is 7mm and that never changed, but the inside part of the seals, which is in contact with the axle and is the actual part that prevents water from getting in went from 12.5mm thick to only 7mm. The old seals were custom made for QS apparently, the new ones are standard that can be found anywhere.
Sure it is nice to be able to find seals anywhere, but I fear it will come at the price of long term reliability. The old seals obviously worked really, really well, as the pictures from the openend motor showed up. Well, anyway, nothing I can do but to use the new seals, the old ones were damaged and had to be replaced.
Old seal:
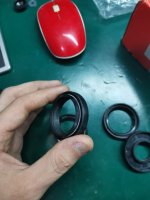
New seals:
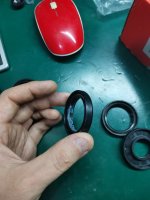
Hopefully you can see the difference on the pics
Next was to install new bearings. No particular difficulty, went smoothly. I went for hopefully good quality bearings made in France:
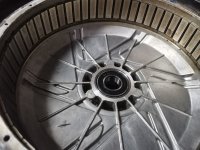
Last but not least was to install new temp sensors. I installed one last time, but it wasn't working properly. It gave me some weirdly high readings, I suppose it wasn't compatible with the Fardriver controller, I don't know.
This time I decided to use not ony one, not only two, but 3 different temperature sensors! Because why not?
This way I could make sure to get consistent results and also have redundancy.
Two of those 3 sensors are intended to be used with the controller. I can only plug one at a time of course, but this way I can compare and use the one that works best for me.
I installed a KTY84-130 and a NTC 230.
The last sensor is a lot more interesting perhaps: I bought a super cheap barbecue thermometer for a dollar:
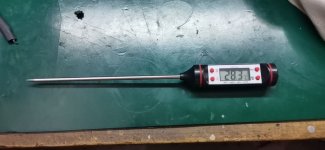
The idea was to dismantle it, install the sensor inside the motor and the display on the dash.
It has a range of -50 to 300 degee C (hopefully it will never see these temps anytime soon!!! :lol: ), a digital display and it also has a very interesting feature because it can record the lowest and highest temperatures it sees over a time period. That means I can ride for a while, then press a button and see what was the maximum temperature, no need to watch it all the time. Pretty cool!
Anyay, I had to pass two new wires for it through the motor axle, then I sticked the 3 sensors inside the coils:
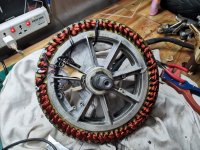
Then I had to extend the wires in order to go from the display to the rear wheel:
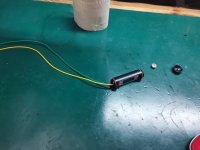
Last but not least, I had to design and print a little bracket system to hold the screen:

Finally painted it black so it wouldn't be too visible:
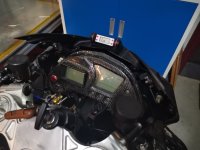
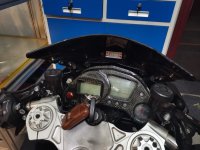
And voila, Just had to re assemble the motor and reinstall in back in place on the bike. Done.
So far from my tests everything works really well! The temperatures in the Fardriver app are very consistent to the ones I get on the dash, so that's very good news, the dash screen works well and it is indeed very practical.
I haven't got the opportunity to push the motor too much these days but after my daily trip to work it did reach a maximum of about 95 degree C. The good thing is that this goes back down very quickly once releasing the throttle, the statorade seems to work pretty well. The casing gets hot to the touch pretty much instantly, it used to be remain cold for a few minutes before.
I'm very happy with these little mods, it has been interesting to make and so far it works great!
Now I finally have a good way to monitor what's happening inside my motor and it will be possible to effectively protect it against high temperatures!
Not sure I can put a lot more amps through the phases though, it seems to get pretty hot already. I'll wait for the rain to stop to see how hot it gets during more spirited rides. :wink: