Sunder
10 MW
Guys,
I followed izeman's build thread with quite a bit of interest, since I found my controller doesn't support the hidden wire brake sensor, especially his part about his reed switch brake. Not quite sure I understood how it worked, but he asked me to start a new thread with photos of my own brake assembly.
The only reed switches which I can find that are small enough to fit on brake, are closed when the magnet is near, and open when no magnet is near - The opposite of what I thought we would need for a switch based ebrake. On my controller, when the circuit is open, it allows power...
So, here's the photo of my brake assembly. Any suggestions on how to build in a reed switch to kill power when I pull the brake lever?
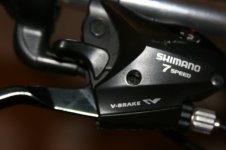
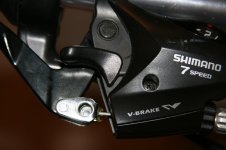
Thanks.
I followed izeman's build thread with quite a bit of interest, since I found my controller doesn't support the hidden wire brake sensor, especially his part about his reed switch brake. Not quite sure I understood how it worked, but he asked me to start a new thread with photos of my own brake assembly.
The only reed switches which I can find that are small enough to fit on brake, are closed when the magnet is near, and open when no magnet is near - The opposite of what I thought we would need for a switch based ebrake. On my controller, when the circuit is open, it allows power...
So, here's the photo of my brake assembly. Any suggestions on how to build in a reed switch to kill power when I pull the brake lever?
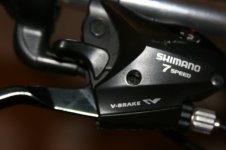
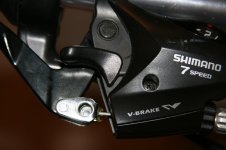
Thanks.