Mr Mik, Your suggestion sounds good but I don't actually have any batteries yet. Well, none that need soldering. I've never before built a battery pack so this whole exercise is a shot in the dark.
The brushes came out of a dead grinder last night but I resisted testing them until this morning. I attached wires and clamped them to a copper strip in close proximity to each other and turned on the power. Nuthin'. Un clamped one and turned on the power again. The fan spun up and I touched the other brush to the copper. Sparks! This is good. A few more sparks cleaned the schmutz off the brush.
Testing with solder I had a nice shinney puddle in about five seconds. Cool!
This phone pic shows the brushes setting in a blob of JB Weld on the ends of bamboo battens taped to coroplast. The strip in the center is the 0.025" copper test piece.

The select pile contained a piece of brass channel stock that has the same inside width as the soapstone refills thickness and almost the same size as the width of the carpenters lead refill.
If that wasn't enough, a square section of the soapstone slips into the split end of a plastic plumbing supply line for sinks. Instant handle.

The pieces are held together with thread in this pic.
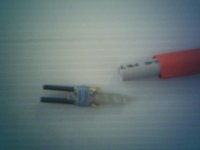
It's going to be encapsulated in JB Weld. The lead refills will be replaceable by sliding them in between the soap stone and brass.
Placing the battery tabs between the tines and twisting the fork brings them into contact with each other completing the circuit.
It should work. Can clearance might be an issue. We'll see.