ferias77
10 W
I would like to try a friction drive on my recumbent.
At the moment, I use a Q100 36V 328RPM with a KU63 controler and a 48V 10Ah battery. But I would like to try something different and lighter.
My recumbent with the Q100 :
I made 30 000 km with this motor. The controler is under the seat and the battery in the tail box.
For my Friction drive, I will use :
- Motor : Turnigy G110 Brushless Outrunner 210kv : http://hobbyking.com/hobbyking/store/__19039__turnigy_g110_brushless_outrunner_210kv_1_10_glow_.html
- Controler : S06P 250W Torque Simulation Square Wave Controller : https://bmsbattery.com/ebike-kit/545-s06p-250w-torque-simulation-square-wave-controller-ebike-kit.html
- Battery : 25,9V 10Ah (7S)
- Roller : 40mm diameter :

- aluminium bracket and swing arm
I will install the friction drive on the front wheel.
The friction drive working :

The drive out of the tire :

The drive in the tire :

What do you think about this design ?
I will add lower and upper dead stops.
I machined the roller and tried it no load on the tire : 37W and 43,3 km/h with 25,9V.
Now I am waiting for the aluminium to make the bracket and swing arm.
Edit : 26/07/2015
I began machining the parts of the friction drive :

Edit : 16/08/2015
The bracket is mounted on the bike :


All is very rigid.
Edit : 28/08/2015
The system is assembled :


And mounted on the bike :
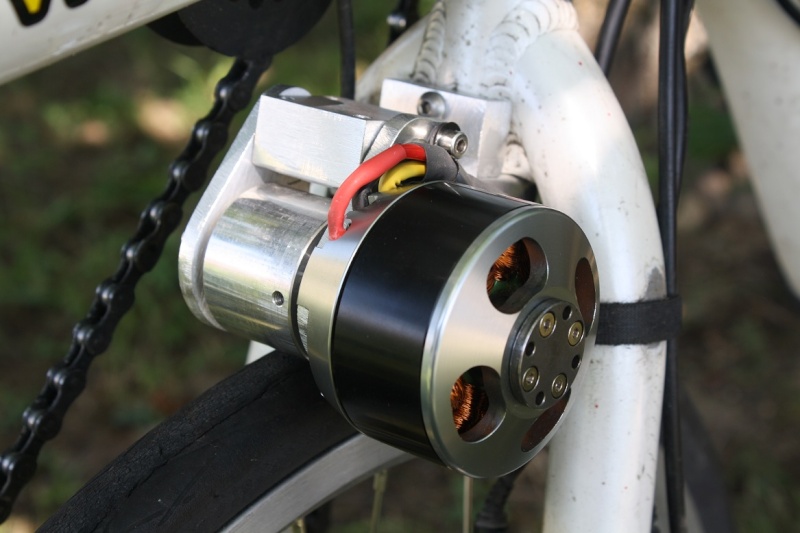

Now, I have to add a spring loading the roller off the tire in the off position, and a endstop for the off position. And finally, to test it !!!!!
Edit : 04/09/2015
I made 207 km with my friction drive : 30.5 km/h average and 6.4 Wh/km. Motor and controler stay barely warm..
I have modified my S06P controler : 23A max instead of 14...
Before modifying the controler :


After modifying :

Edit : 23/09/2015
802km with the friction drive !
A photo of the complete system :

Mounted on the bike :

It works perfectly when it's dry. But it slips when it's wet.
I have to make a knurled roller, like EVTodd...
I replaced the friction drive with my Q100 hub motor, waiting for this knurled roller.
At the moment, I use a Q100 36V 328RPM with a KU63 controler and a 48V 10Ah battery. But I would like to try something different and lighter.
My recumbent with the Q100 :

I made 30 000 km with this motor. The controler is under the seat and the battery in the tail box.
For my Friction drive, I will use :
- Motor : Turnigy G110 Brushless Outrunner 210kv : http://hobbyking.com/hobbyking/store/__19039__turnigy_g110_brushless_outrunner_210kv_1_10_glow_.html
- Controler : S06P 250W Torque Simulation Square Wave Controller : https://bmsbattery.com/ebike-kit/545-s06p-250w-torque-simulation-square-wave-controller-ebike-kit.html
- Battery : 25,9V 10Ah (7S)
- Roller : 40mm diameter :

- aluminium bracket and swing arm
I will install the friction drive on the front wheel.
The friction drive working :

The drive out of the tire :

The drive in the tire :

What do you think about this design ?
I will add lower and upper dead stops.
I machined the roller and tried it no load on the tire : 37W and 43,3 km/h with 25,9V.
Now I am waiting for the aluminium to make the bracket and swing arm.
Edit : 26/07/2015
I began machining the parts of the friction drive :

Edit : 16/08/2015
The bracket is mounted on the bike :


All is very rigid.
Edit : 28/08/2015
The system is assembled :


And mounted on the bike :
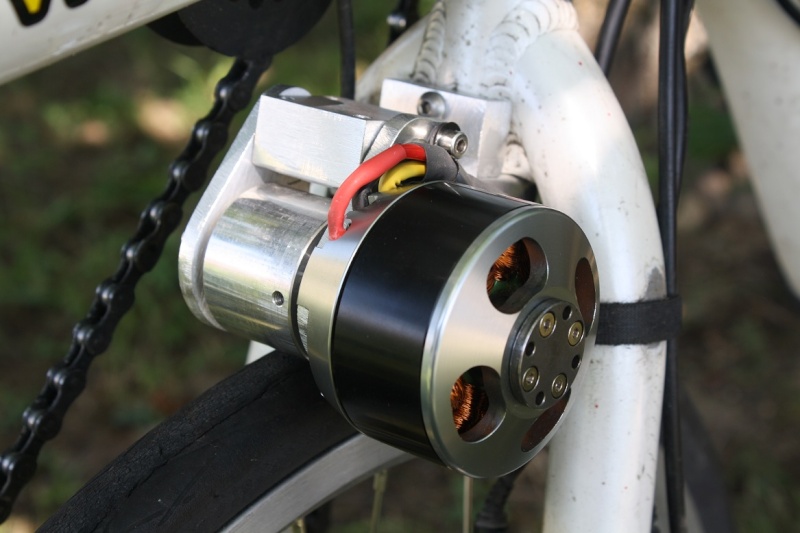

Now, I have to add a spring loading the roller off the tire in the off position, and a endstop for the off position. And finally, to test it !!!!!
Edit : 04/09/2015
I made 207 km with my friction drive : 30.5 km/h average and 6.4 Wh/km. Motor and controler stay barely warm..
I have modified my S06P controler : 23A max instead of 14...
Before modifying the controler :


After modifying :

Edit : 23/09/2015
802km with the friction drive !
A photo of the complete system :

Mounted on the bike :

It works perfectly when it's dry. But it slips when it's wet.
I have to make a knurled roller, like EVTodd...
I replaced the friction drive with my Q100 hub motor, waiting for this knurled roller.