Cold-E-Commuter
100 W
Hi all,
Just wanted to share info on my installation of a front hub motor with an aluminum suspension fork.
So here's the bike update info. Front hub motor is still an NC2806. I have been running this with a RST191 cheapo steel suspension fork and a v-brake for quite a while. The v-brake has been an issue for me for a while. When running 21s LiPo and reaching speeds exceeding 50 mph the margin for error was narrow. The fork recently developed a rust problem and became a solid fork so it was time to replace it. It has been replaced with a Rockshox XC32TK with 100mm travel, adjustable damper and rebound with a remote lockout. The drop outs are aluminum. Also replaced was the v-brake. I now have an Avid BB7 disc unit installed on the front. (looking for a bracket to do the same out back) This weeks rides were conducted using a Ping 48V15A pack (really 51.2 volts nominal and 57 volts hot from charger) as a low power base. Top speeds have been less than 40 mph. I'll up the power as time goes on and confidence is complete. Not ready to push 3Kw thru it yet, but I'll hopefully be here to let you know how that goes. To satisfy my safety requirements I have installed dual torque arms and added what I call a steel pinch point washer to go with the c-washers.
View attachment 1
Notice what I call the pinch washers on the inside of the drop outs of both sides as stated. My intent is to keep the aluminum drop outs as stable as possible and not allow them to spread. I have also carefully placed the torque arms so that they are turned as far to the initiation point as possible to keep the axle from ever contacting the drop-out. Also, the rotor had to be spaced from the hub 1.7mm to allow the caliper to clear the inside of the motor. Washers were methodically machined (using a file) to do so. The torque arm support on the disc brake side was ground to fit the shape of the caliper.
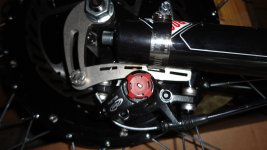
The total time spent on this was between 16 and 18 hours. Happy to share more photos and info for thise interested.
D
Just wanted to share info on my installation of a front hub motor with an aluminum suspension fork.
So here's the bike update info. Front hub motor is still an NC2806. I have been running this with a RST191 cheapo steel suspension fork and a v-brake for quite a while. The v-brake has been an issue for me for a while. When running 21s LiPo and reaching speeds exceeding 50 mph the margin for error was narrow. The fork recently developed a rust problem and became a solid fork so it was time to replace it. It has been replaced with a Rockshox XC32TK with 100mm travel, adjustable damper and rebound with a remote lockout. The drop outs are aluminum. Also replaced was the v-brake. I now have an Avid BB7 disc unit installed on the front. (looking for a bracket to do the same out back) This weeks rides were conducted using a Ping 48V15A pack (really 51.2 volts nominal and 57 volts hot from charger) as a low power base. Top speeds have been less than 40 mph. I'll up the power as time goes on and confidence is complete. Not ready to push 3Kw thru it yet, but I'll hopefully be here to let you know how that goes. To satisfy my safety requirements I have installed dual torque arms and added what I call a steel pinch point washer to go with the c-washers.
View attachment 1
Notice what I call the pinch washers on the inside of the drop outs of both sides as stated. My intent is to keep the aluminum drop outs as stable as possible and not allow them to spread. I have also carefully placed the torque arms so that they are turned as far to the initiation point as possible to keep the axle from ever contacting the drop-out. Also, the rotor had to be spaced from the hub 1.7mm to allow the caliper to clear the inside of the motor. Washers were methodically machined (using a file) to do so. The torque arm support on the disc brake side was ground to fit the shape of the caliper.
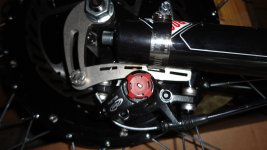
The total time spent on this was between 16 and 18 hours. Happy to share more photos and info for thise interested.
D