snath
100 W
Used Kepler's idea of running the motor on the tire and EV Todd's idea of a sliding mount to build this drive for a Dahon Boardwalk around a 1"X2" piece of 8020 extrusion and an 8020 linear motion guide. A spiral wound piece of a sanding belt held on with carpet tape provides excellent traction and hall sensors ease takeoff.
Here are some pictures.
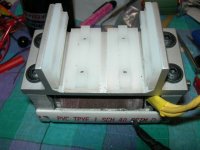
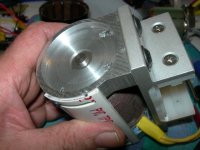
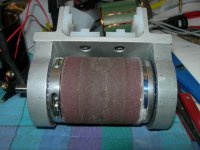
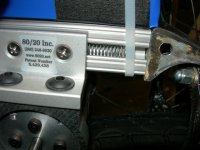
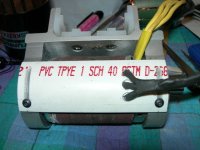
View attachment 1
The outfit works well on my Dahon but doesn't have enough power to assist me up Atlanta hills without my knees hurting so I am working on another drive using a motor similar in size to EV Todd's and, like his rig, hanging off the side. It's almost finished.
It will have halls as well and for those following the fitting process to outrunners, here's a tip.... stuff them edgeways (but oriented the same.. i.e. dots all facing the same direction) into the groove; they don't care.
You can also use three-wire strips torn off ribbon cable to hook them up... makes it easy to keep track of which wire is which. Here's a picture.
Larry Barefield
Here are some pictures.
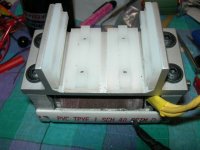
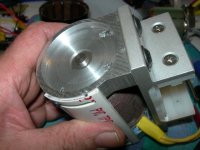
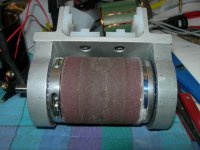
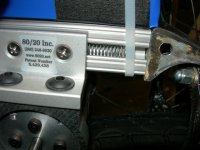
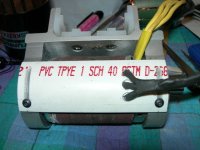
View attachment 1
The outfit works well on my Dahon but doesn't have enough power to assist me up Atlanta hills without my knees hurting so I am working on another drive using a motor similar in size to EV Todd's and, like his rig, hanging off the side. It's almost finished.
It will have halls as well and for those following the fitting process to outrunners, here's a tip.... stuff them edgeways (but oriented the same.. i.e. dots all facing the same direction) into the groove; they don't care.
You can also use three-wire strips torn off ribbon cable to hook them up... makes it easy to keep track of which wire is which. Here's a picture.
Larry Barefield