chvidgov.bc.ca
10 kW
I have a Conhis pack...
http://www.conhismotor.com/ProductShow.asp?id=456
The externally facing keyswitch fails to turn off the main power leads from the pack to the ebike. They are locked in the "on" position, even in "off" on the keyswitch, producing power whether the key is turned or not.
The keyswitch is connected to a relay which cuts the main (+) output...you can see the two thicker red wires going to the relay.
Here is the picture...
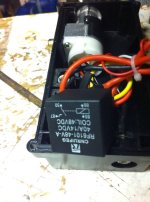
After email with Conhis, they told me to open the relay cover and "see if the switch moves" when the key is turned. It does! So it wasn't the keyswitch I don't think.
Suddenly now it works - the system is back to normal - the keyswitch turns off the power in the Off position.
I'd like to understand why the relay wasn't working, and now is, after the cover is removed. It was not burned or welded shut, the inside of the relay.
I could just wire around the relay, leaving the pack "always on" powerwise which is ok, although it is nice to turn off the controller this way.
Do I need a replacement relay? Will an alternative automotive relay aquired here do the job if it can handle 40 amps?
The switch wouldn't be affecting the BMS operation I imagine, meaning there would be quiescent drain of the BMS, even when the pack is normally "off".
So, other than removing quiescent drain from the controller, the on/off switch doesn't do much, other than inactivating the throttle - should be ok is bike is left on charger when away.
Defaulting to "on" works the same. The bike works normally.
Is this just a "jammed" relay or weak spring?
Thanks, Chris.
http://www.conhismotor.com/ProductShow.asp?id=456
The externally facing keyswitch fails to turn off the main power leads from the pack to the ebike. They are locked in the "on" position, even in "off" on the keyswitch, producing power whether the key is turned or not.
The keyswitch is connected to a relay which cuts the main (+) output...you can see the two thicker red wires going to the relay.
Here is the picture...
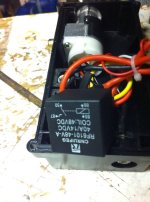
After email with Conhis, they told me to open the relay cover and "see if the switch moves" when the key is turned. It does! So it wasn't the keyswitch I don't think.
Suddenly now it works - the system is back to normal - the keyswitch turns off the power in the Off position.
I'd like to understand why the relay wasn't working, and now is, after the cover is removed. It was not burned or welded shut, the inside of the relay.
I could just wire around the relay, leaving the pack "always on" powerwise which is ok, although it is nice to turn off the controller this way.
Do I need a replacement relay? Will an alternative automotive relay aquired here do the job if it can handle 40 amps?
The switch wouldn't be affecting the BMS operation I imagine, meaning there would be quiescent drain of the BMS, even when the pack is normally "off".
So, other than removing quiescent drain from the controller, the on/off switch doesn't do much, other than inactivating the throttle - should be ok is bike is left on charger when away.
Defaulting to "on" works the same. The bike works normally.
Is this just a "jammed" relay or weak spring?
Thanks, Chris.