ecat
10 W
- Joined
- Apr 8, 2009
- Messages
- 88
This post is part one of a build log of my electric runabout project. This was a big project, it took about a year to complete. lots of pictures, and the max for a single post on ES is 30, so I will post a part two for the rest.
This boat was built for my sister, I figured she needed a fun runabout that would cost next to nothing to run, and would be environmentally friendly, and would have low maintenance requirements. I also wanted to demonstrate for others that there are other more responsible ways of getting around on a daily basis.
I am hoping that it will have the range and speed to make the 6 nautical mile trip from her water access only home to Deep Cove in North Vancouver in a reasonable amount of time, about 35-45 minutes. It takes about 15-20 minutes by regular speedboat, and costs about $10.00 in gas. Sparky should do it for about $0.15 worth of electricity.
The hulls are from a Hobie 16' sailing catamaran, the motor is a Mercury 9.8 two stroke outboard, with the power head removed, and a Mars 6 HP brush-less permanent magnet electric motor installed in its place.
Batteries are GB 48 volt, 100 amp hour lithium iron phosphate. They weigh about 100 lb. This build would not have been possible with lead acid batteries.View attachment 27
Basic CAD plan. The console may be moved back, not sure yet. As it sits now the throttle and gear shift cables are not long enough to reach the motor as drawn. An on the water trial will give some answers.
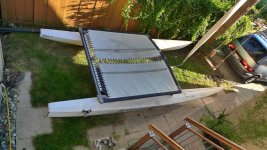
I picked it up at Jericho Sailing Center for $840.00 ready to sail. I then sold the sailing gear , mast and sails for $525.00, so it was cheap. It needed a bit of work, mostly cosmetic. I beefed up the hull bottoms with Kevlar strips, and fared and painted the hulls. This cost more than the boat!
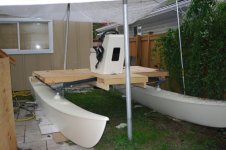
Here the hulls have fresh epoxy paint, and a temporary deck has been built to do an on the water test for weight distribution and motor placement. The steering console was a great find at the local marine consignment store. It has the throttle and steering cables still attached.
View attachment 24
The Merc with engine removed and Lovejoy coupling installed. I cut the end off of the crankshaft, and it fits onto the splined shaft in the outboard leg.
The pic below shows the Lovejoy L090 coupling on the crankshaft stub, sitting on the outboard drive shaft. I had to have the crankshaft stub machined down slightly to .75", and also had the machinist add a key-way in the crankshaft stub to keep the coupling from spinning on the shaft.

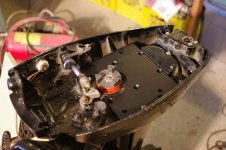
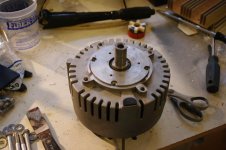
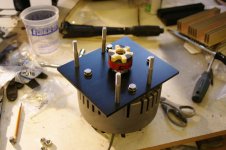
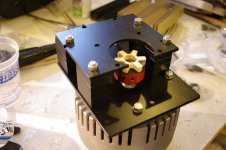
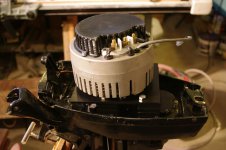
View attachment 17
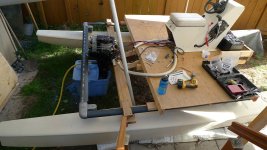
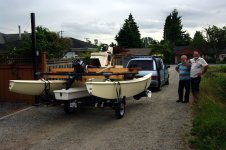
View attachment 14
Batteries at front is slightly faster (0.2 knots) than at the back, at 5.6 knots. with the stock prop. Power draw is 1300 watts at 2500 RPM, which is max speed for this motor controller. The Sevcon controller will do 3500 RPM or more, and we will need a larger prop to get to 5000 watts
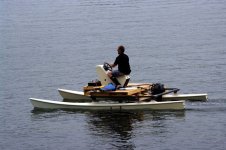
The hulls seem low in the water, should be able to knock some weight off. The temporary lumber deck weighs in at about 130 lb, and the lead acid batteries at 180 lb. I figure the final version may come in 90 lb lighter. Turning radius is too large, I have to play with the steering, and maybe add a larger skeg to the motor
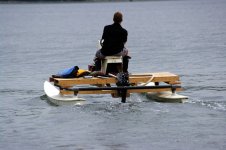
View attachment 10
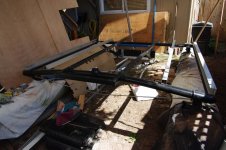
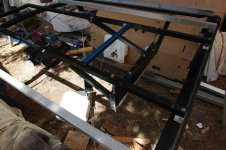
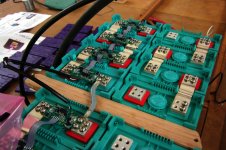
The GBS 100 AH cells. These are an improvement over the Thundersky cells in that they were designed to take BMS boards and they have covers that protect the BMS and electrical terminals. The terminals have four small screws each instead of one large screw, which means that they can not rotate and come loose. I had to replace all of these button head screws with regular tall head screws in order to get enough torque on the connections. At first the connections were heating, and there was lots of voltage drop at high current. The motor can pull 100 amps.
More build pics on the way, stay tuned...
Installing the batteries. These are the 16 GB 100AH 3.3 V Lithium cells. Nominal voltage is 52.8 V for the pack, with a capacity of 5280 watt hours. So in theory I can draw 500 watts for 10 hours, or 5000 watts for an hour. They come in groups of four strapped together. Total weight is about 98 lb. If I used the lead acid car batteries that were used in initial testing there would be 12 batteries at a total of 550 lb to equal this energy storage. 6 of the 16 BMS circuit boards are mounted in this shot. They keep the cells in balance, and to warn of under or over voltage. I keep the yet to be mounted boards in a plastic bag so as to avoid a short circuit.
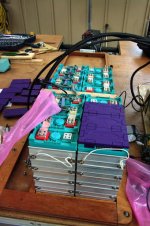
The batteries are held in place by a groove in the oak frame, which is epoxied to the deck. The groove interfaces with the aluminum extrusion on the ends of the batteries. The oak piece across the top keeps the batteries pressed into the grove at the front and back, and holds the middle down. The cables going through the deck are steering, motor control, and shifter.
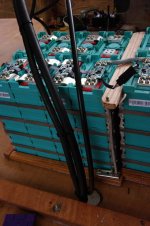
I bought the batteries in an "application kit" which includes a video display that shows volts, amps, approximate capacity, and individual cell voltages. The kit also comes with the BMS boards. as well as the black box computer that monitors the system and generates the video for the display, and a 15 amp charger.
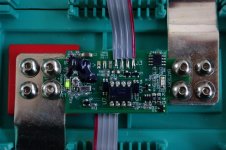
View attachment 3
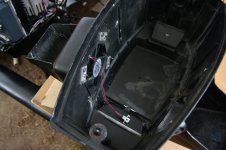
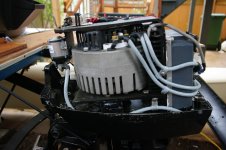
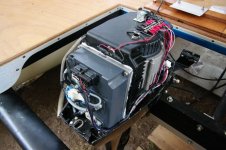
For more build photos and final results, see part the part two post.
This boat was built for my sister, I figured she needed a fun runabout that would cost next to nothing to run, and would be environmentally friendly, and would have low maintenance requirements. I also wanted to demonstrate for others that there are other more responsible ways of getting around on a daily basis.
I am hoping that it will have the range and speed to make the 6 nautical mile trip from her water access only home to Deep Cove in North Vancouver in a reasonable amount of time, about 35-45 minutes. It takes about 15-20 minutes by regular speedboat, and costs about $10.00 in gas. Sparky should do it for about $0.15 worth of electricity.
The hulls are from a Hobie 16' sailing catamaran, the motor is a Mercury 9.8 two stroke outboard, with the power head removed, and a Mars 6 HP brush-less permanent magnet electric motor installed in its place.
Batteries are GB 48 volt, 100 amp hour lithium iron phosphate. They weigh about 100 lb. This build would not have been possible with lead acid batteries.View attachment 27
Basic CAD plan. The console may be moved back, not sure yet. As it sits now the throttle and gear shift cables are not long enough to reach the motor as drawn. An on the water trial will give some answers.
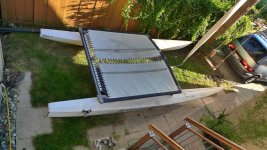
I picked it up at Jericho Sailing Center for $840.00 ready to sail. I then sold the sailing gear , mast and sails for $525.00, so it was cheap. It needed a bit of work, mostly cosmetic. I beefed up the hull bottoms with Kevlar strips, and fared and painted the hulls. This cost more than the boat!
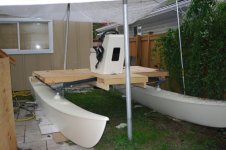
Here the hulls have fresh epoxy paint, and a temporary deck has been built to do an on the water test for weight distribution and motor placement. The steering console was a great find at the local marine consignment store. It has the throttle and steering cables still attached.
View attachment 24
The Merc with engine removed and Lovejoy coupling installed. I cut the end off of the crankshaft, and it fits onto the splined shaft in the outboard leg.
The pic below shows the Lovejoy L090 coupling on the crankshaft stub, sitting on the outboard drive shaft. I had to have the crankshaft stub machined down slightly to .75", and also had the machinist add a key-way in the crankshaft stub to keep the coupling from spinning on the shaft.

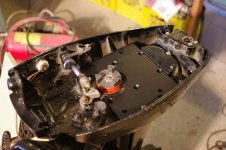
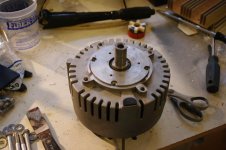
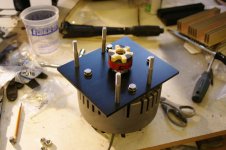
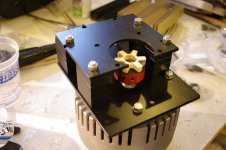
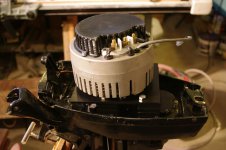
View attachment 17
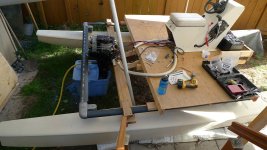
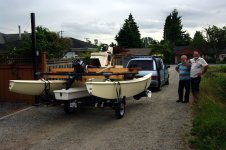
View attachment 14

Batteries at front is slightly faster (0.2 knots) than at the back, at 5.6 knots. with the stock prop. Power draw is 1300 watts at 2500 RPM, which is max speed for this motor controller. The Sevcon controller will do 3500 RPM or more, and we will need a larger prop to get to 5000 watts
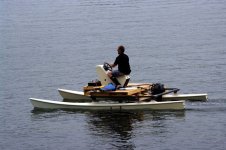
The hulls seem low in the water, should be able to knock some weight off. The temporary lumber deck weighs in at about 130 lb, and the lead acid batteries at 180 lb. I figure the final version may come in 90 lb lighter. Turning radius is too large, I have to play with the steering, and maybe add a larger skeg to the motor
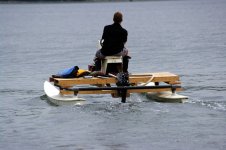
View attachment 10
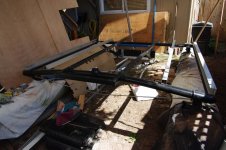
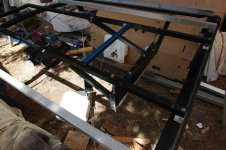
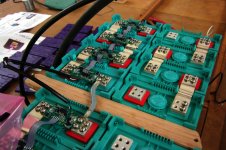
The GBS 100 AH cells. These are an improvement over the Thundersky cells in that they were designed to take BMS boards and they have covers that protect the BMS and electrical terminals. The terminals have four small screws each instead of one large screw, which means that they can not rotate and come loose. I had to replace all of these button head screws with regular tall head screws in order to get enough torque on the connections. At first the connections were heating, and there was lots of voltage drop at high current. The motor can pull 100 amps.
More build pics on the way, stay tuned...
Installing the batteries. These are the 16 GB 100AH 3.3 V Lithium cells. Nominal voltage is 52.8 V for the pack, with a capacity of 5280 watt hours. So in theory I can draw 500 watts for 10 hours, or 5000 watts for an hour. They come in groups of four strapped together. Total weight is about 98 lb. If I used the lead acid car batteries that were used in initial testing there would be 12 batteries at a total of 550 lb to equal this energy storage. 6 of the 16 BMS circuit boards are mounted in this shot. They keep the cells in balance, and to warn of under or over voltage. I keep the yet to be mounted boards in a plastic bag so as to avoid a short circuit.
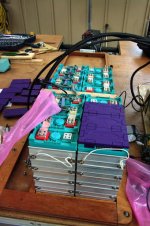
The batteries are held in place by a groove in the oak frame, which is epoxied to the deck. The groove interfaces with the aluminum extrusion on the ends of the batteries. The oak piece across the top keeps the batteries pressed into the grove at the front and back, and holds the middle down. The cables going through the deck are steering, motor control, and shifter.
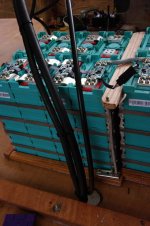
I bought the batteries in an "application kit" which includes a video display that shows volts, amps, approximate capacity, and individual cell voltages. The kit also comes with the BMS boards. as well as the black box computer that monitors the system and generates the video for the display, and a 15 amp charger.
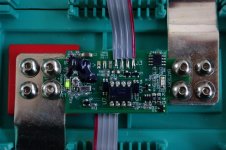
View attachment 3
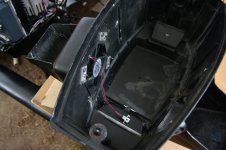
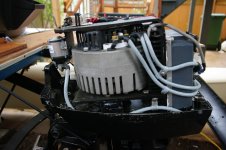
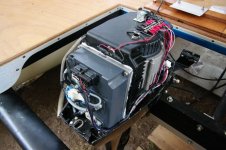
For more build photos and final results, see part the part two post.