trackebike
10 mW
- Joined
- Sep 6, 2020
- Messages
- 24
I'm having trouble with an ebike pack that I have built. Cells are Samsung 3500ma. The problem is that the charger light shows green but the individual cell groupings all measure 3.64-3.65V. The pack is balanced but I would have expected a higher voltage for a fully charged pack.
The charger is an inexpensive 2A unit I purchase off of ebay, it was advertised as an ebike 36 volt charger. It's open circuit voltage is ~42 volts. If I bypass the BMS the charger light goes red indicating it is charging.
I believe the problem is my BMS who's label is indicated below. I think this BMS is intended for a LIPO battery and not for LION. I can't read the Chinese, but I see the 3.7 volt check mark. Is my hunch correct? a LIPO BMS?
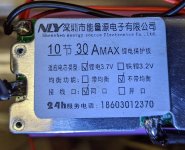
The charger is an inexpensive 2A unit I purchase off of ebay, it was advertised as an ebike 36 volt charger. It's open circuit voltage is ~42 volts. If I bypass the BMS the charger light goes red indicating it is charging.
I believe the problem is my BMS who's label is indicated below. I think this BMS is intended for a LIPO battery and not for LION. I can't read the Chinese, but I see the 3.7 volt check mark. Is my hunch correct? a LIPO BMS?
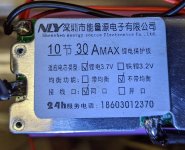