re: JB weld.
Not laughing................hard anyway!!! :lol: 8)
But seriously...
If you make an accurate pattern, you can take an inexpensive router table, a carbide pattern following bit, the ones with
bearings on the end and machine aluminum with it.
An accurate pattern can produce dovetails for example with accuracy better than 5 thousandths
of an inch....seriously....
1. Copy: Pull the shape with the Contour Gauge
2. Template: Transfer the shape to your template material.. 1/4 to 3/8 ply, masonite, solid wood, plastic whatever.
Cut the oval hole in your template. This step needs to be as accurate as possible because it is the master pattern.
Sneek up on the cut slowly. A scroll saw would be the best thing for this. A suitable jig and a router table
would also allow you to freehand the cut. Of course, all this takes some skill.
3. Machine Mounts : Trace the template onto the mount. Cut the ragged holes undersized using the hole saw.
Overlay and clamp the template to the mount. Slide the assembly over the pattern bit and machine to the pattern.
The bearing will follow the template and you will have exact replica of the pattern (empasize the importance of step 2)
Even if you have CNC capability, the contour gauge will make easy to copy the profile directly off the tube.
You can then scan the drawing, convert to CAM file and now you have the profile. May require a little tweaking,
but you can zero in much faster. kinda of like a poor boys coordinate measuring machine or CMM.
Tapered tubes would with compound curves would be really hard, and the mold method would be easier.
You could make a template with the mold method....no high accuracy machine steps required in making the template
because the mold would be a perfect fit...(saran wrap would be easier than card stock).
router template machining is well documented....
Here's an example for a dremel router, probably better suited for plywood. It uses a collar instead of bearing for
following the template.
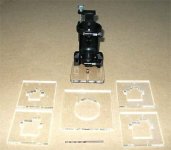