TylerDurden
100 GW
Well, until we can find opportunity-charging locations across the country, we may need to take our EVs further than they can travel on their own.
I have been towing my EVs on flatbed trailers behind my van, but the trailers have had some issues which I have tried to resolve:
They have been heavier than needed.
They have been single-axle.
The lightweight tandem-axle trailers on the market have been big & heavy and big-bucks (relatively speaking).
I modified a trailer... well, two trailers actually, to make an affordable lightweight tandem. It ain't perfect, but it's moving in the right direction.
I bought two of these 4'x8' weenies from Harbor Fright:
View attachment 9 http://www.harborfreight.com/cpi/ctaf/displayitem.taf?Itemnumber=42709
I had married two of these together before, with fixed axles... similar to trailers used to carry snowmobiles. That trailer gave it's life to protect my Commutacar and my sorry-butt in a recent highway crash. This time I wanted to try having the axles joined with an equalizer, to keep the weight distributed evenly regardless of the pitch of the trailer. To make it even more of a challenge, I intended to make the trailer using common tools and as little additional material as possible.
To add an axle, meant eliminating the folding feature of the trailer. No biggie. It would also mean come creative cutting and shaping of some pieces...
I cut the original spring-hanger/folding-brace to get the steel for the equalizers, leaving the center for the pivot mount:
Cutting the sides first, then grinding the welds without chewing into the workpieces, then cutting across to free the channel.
View attachment 6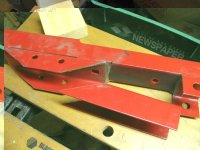
Then I cut the angle into sections that can be bolted to the frame-rails. The channel will be the equalizers.
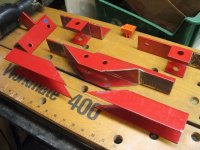
I drilled the pieces for 3/8" hardware (supplied in the kits). I figured it might also be good to smooth the pieces, to reduce sharp corners and edges:
View attachment 2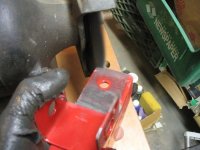
I flattened the fender supports with a BFH. They are heavier steel.
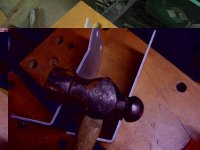
more on the way...
I have been towing my EVs on flatbed trailers behind my van, but the trailers have had some issues which I have tried to resolve:
They have been heavier than needed.
They have been single-axle.
The lightweight tandem-axle trailers on the market have been big & heavy and big-bucks (relatively speaking).
I modified a trailer... well, two trailers actually, to make an affordable lightweight tandem. It ain't perfect, but it's moving in the right direction.
I bought two of these 4'x8' weenies from Harbor Fright:
View attachment 9 http://www.harborfreight.com/cpi/ctaf/displayitem.taf?Itemnumber=42709
I had married two of these together before, with fixed axles... similar to trailers used to carry snowmobiles. That trailer gave it's life to protect my Commutacar and my sorry-butt in a recent highway crash. This time I wanted to try having the axles joined with an equalizer, to keep the weight distributed evenly regardless of the pitch of the trailer. To make it even more of a challenge, I intended to make the trailer using common tools and as little additional material as possible.
To add an axle, meant eliminating the folding feature of the trailer. No biggie. It would also mean come creative cutting and shaping of some pieces...
I cut the original spring-hanger/folding-brace to get the steel for the equalizers, leaving the center for the pivot mount:
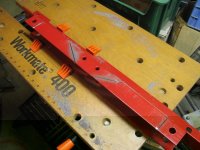
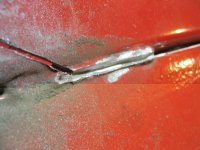
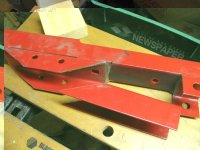
Then I cut the angle into sections that can be bolted to the frame-rails. The channel will be the equalizers.
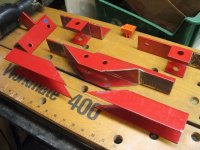
I drilled the pieces for 3/8" hardware (supplied in the kits). I figured it might also be good to smooth the pieces, to reduce sharp corners and edges:
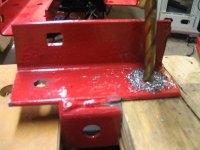
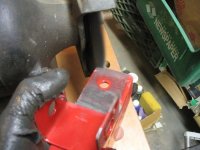
I flattened the fender supports with a BFH. They are heavier steel.
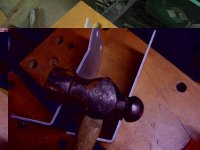
more on the way...