SniperGaulois
10 kW
After 3000 miles and very many curbs and mountains, the bike did this:
I forced the bracket out wide when i fitted the motor. Do you think i should leave the 2mm gap in the crack to have more welding space and to account for the width of the motor? should i weld in the same alignment?
If i don't align the crack when i weld it, it will be stronger?
I want to go to a garage to have it TIG welded with an extra triangle as a reinforcement. I have a trashed ALU bike to salvage some alu as a triangle, maybe i should add a tube joint instead of a flat one.
It's a centurion backfire LRS 1, the versions 2 and 3 changed to a stronger layout:
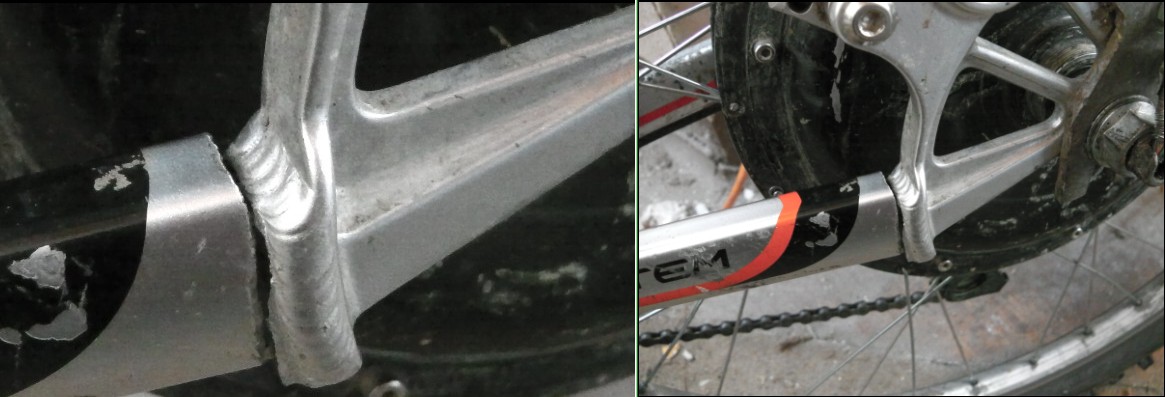
I forced the bracket out wide when i fitted the motor. Do you think i should leave the 2mm gap in the crack to have more welding space and to account for the width of the motor? should i weld in the same alignment?
If i don't align the crack when i weld it, it will be stronger?
I want to go to a garage to have it TIG welded with an extra triangle as a reinforcement. I have a trashed ALU bike to salvage some alu as a triangle, maybe i should add a tube joint instead of a flat one.
It's a centurion backfire LRS 1, the versions 2 and 3 changed to a stronger layout:
