casainho
10 GW
- Joined
- Feb 14, 2011
- Messages
- 6,058
I put the first 4 cells charging at limited current of 200mA and set the voltage to 16.4V, then I took this picture:
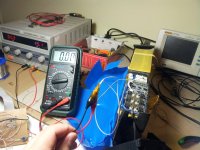
After I limited the current to 500mA and let the cells charge for 2 hours, tested and the battery is back again to life!!!
Then I left the cells charging for 7 hours, tested it and finally placed back on bicycle. I made long ride to discharge the battery a bit and put it again to charge. Now I am using a device to measure the power used by the charger and monitor it, since the green LED doesn't mean it is fully charged... (it needs time on the charge to balance the cells):
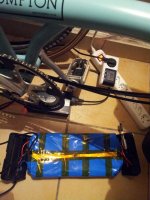
Many thanks to everyone that participated and helped!
Now I am back to focus on my project EBike Smart Controller (OpenSource).
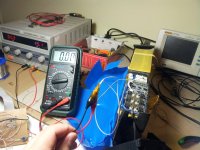
After I limited the current to 500mA and let the cells charge for 2 hours, tested and the battery is back again to life!!!
Then I left the cells charging for 7 hours, tested it and finally placed back on bicycle. I made long ride to discharge the battery a bit and put it again to charge. Now I am using a device to measure the power used by the charger and monitor it, since the green LED doesn't mean it is fully charged... (it needs time on the charge to balance the cells):
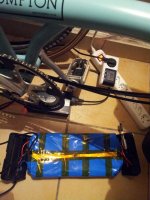
Many thanks to everyone that participated and helped!
Now I am back to focus on my project EBike Smart Controller (OpenSource).