rick_p
100 W
Important note; I picked up this wheel second hand knowing it had a couple of broken spokes at the time I purchased it.
At first I thought it was just a case of lack of maintenance because some of the spokes were loose, so it was logical to me that loose spokes would rub against the hole in the hub and eventually cut through the spoke, or cause it to flex back and forth until it snaps. However, when I replaced the broken spokes, I did so with factory original replacement spokes, properly trued the wheel, and made sure none of the spokes were loose.
I thought for sure this would resolve any issues, it was easy to true the wheel, it didn’t give me any trouble, but not the case, it not only broke more spokes within a hundred miles, one of the broken spokes was a new one, and they all break at the same location every time. So, something else has to, or had to be wrong.
What I did next was to completely disassemble the wheel so I could get a really good look at things and check the condition of the rim, I was concerned that maybe the rim was way out of whack, and thus causing undo stress on the spokes to pull it into true, but no, it’s flat and round within a 64th of an inch with no spokes. I do see a little wear on a few spokes at the location where others had snapped, but nothing extreme. I also see a little wear at a couple of the holes in the hub, but again, nothing severe.
I’m kind of perplexed and hence the reason for the post, I’d love to hear what others think. The only idea I have left is maybe it was poorly or incorrectly assembled, and maybe the issue will resolve itself when I lace and true it correctly.
Here’s are a few pictures, which might help with diagnosis.
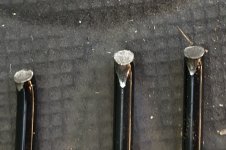
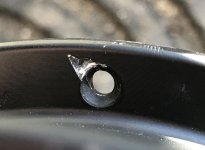
At first I thought it was just a case of lack of maintenance because some of the spokes were loose, so it was logical to me that loose spokes would rub against the hole in the hub and eventually cut through the spoke, or cause it to flex back and forth until it snaps. However, when I replaced the broken spokes, I did so with factory original replacement spokes, properly trued the wheel, and made sure none of the spokes were loose.
I thought for sure this would resolve any issues, it was easy to true the wheel, it didn’t give me any trouble, but not the case, it not only broke more spokes within a hundred miles, one of the broken spokes was a new one, and they all break at the same location every time. So, something else has to, or had to be wrong.
What I did next was to completely disassemble the wheel so I could get a really good look at things and check the condition of the rim, I was concerned that maybe the rim was way out of whack, and thus causing undo stress on the spokes to pull it into true, but no, it’s flat and round within a 64th of an inch with no spokes. I do see a little wear on a few spokes at the location where others had snapped, but nothing extreme. I also see a little wear at a couple of the holes in the hub, but again, nothing severe.
I’m kind of perplexed and hence the reason for the post, I’d love to hear what others think. The only idea I have left is maybe it was poorly or incorrectly assembled, and maybe the issue will resolve itself when I lace and true it correctly.
Here’s are a few pictures, which might help with diagnosis.
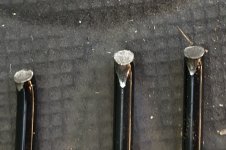
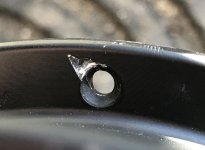