lawsonuw
1 kW
Well it works, so it's time to spill the beans on what I've been cobbling together. First the pictures 
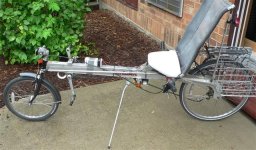
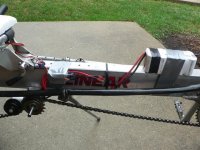
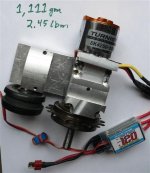
Motor: Cheap Chinese Motor (uses a standard RS-550 mounting bolt pattern)
ESC: Cheap Chinese ESC
Battery: 3.0Ah 12v NiCd battery left over from my first battlebot.
Throttle: AstroFlight servo tester
Gearbox: First Choice; What was actually in stock; What I'll be switching to
Freewheel: a cheap'o Shimono
Freewheel adaptor: Made my own but THIS Stanton-Inc adaptor would work just as well.
MVP: McM# 91458A21 Loctite 609 Retaining compound.
Well I've taken two test rides so far. The system does exactly what I want it to do, kill the two steep hills in my daily commute. The gearbox is rather noisy though it seems to be quieting down a bit. The cadence at maximum assist is about 45rpm, a bit too low for hill climbing. I'm switching to a 25:1 gearbox to up the cadence and improve efficiency by dropping a gearbox stage. I DO wish I could've used the BaneBots 42mm gearboxes, the extra pinions available for these boxes would've been a direct fit for the motor's 5mm shaft. As it is I had to turn down the motor's shaft to fit the pinion. (many inrunners and DC motors use a 3.2mm shaft size though) I've also found the weak spot in my system. Luckily the weak point is the glue joint connecting my freewheel adapter to the gearbox's output shaft, something easy to fix.
Oh yea, 2.45lb for 300-500 watts of assist into my chain
Marty
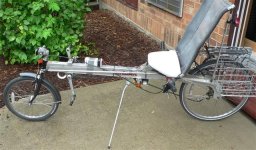
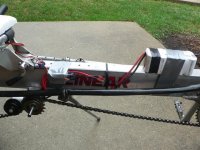
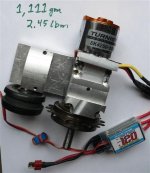
Motor: Cheap Chinese Motor (uses a standard RS-550 mounting bolt pattern)
ESC: Cheap Chinese ESC
Battery: 3.0Ah 12v NiCd battery left over from my first battlebot.
Throttle: AstroFlight servo tester
Gearbox: First Choice; What was actually in stock; What I'll be switching to
Freewheel: a cheap'o Shimono
Freewheel adaptor: Made my own but THIS Stanton-Inc adaptor would work just as well.
MVP: McM# 91458A21 Loctite 609 Retaining compound.
Well I've taken two test rides so far. The system does exactly what I want it to do, kill the two steep hills in my daily commute. The gearbox is rather noisy though it seems to be quieting down a bit. The cadence at maximum assist is about 45rpm, a bit too low for hill climbing. I'm switching to a 25:1 gearbox to up the cadence and improve efficiency by dropping a gearbox stage. I DO wish I could've used the BaneBots 42mm gearboxes, the extra pinions available for these boxes would've been a direct fit for the motor's 5mm shaft. As it is I had to turn down the motor's shaft to fit the pinion. (many inrunners and DC motors use a 3.2mm shaft size though) I've also found the weak spot in my system. Luckily the weak point is the glue joint connecting my freewheel adapter to the gearbox's output shaft, something easy to fix.
Oh yea, 2.45lb for 300-500 watts of assist into my chain

Marty