Hi All,
I'm new to the EV world and this will be my first build. My intent is to build an electric 4-wheel skid steer vehicle to transport bins of fruit around an orchard (see attached CAD images). In terms of functionality, the vehicle is sort of a cross between an e-bike, fork lift, and a stand-up skid steer. The steel frame and fork lift designs are mostly complete, but I need some help specifying the optimal hub motors, controllers, braking components, batteries, and throttles. Here are the specs for the vehicle:
Thanks in advance for any help, guidance, and recommendations!

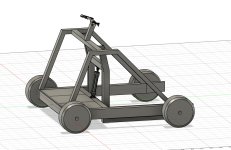

I'm new to the EV world and this will be my first build. My intent is to build an electric 4-wheel skid steer vehicle to transport bins of fruit around an orchard (see attached CAD images). In terms of functionality, the vehicle is sort of a cross between an e-bike, fork lift, and a stand-up skid steer. The steel frame and fork lift designs are mostly complete, but I need some help specifying the optimal hub motors, controllers, braking components, batteries, and throttles. Here are the specs for the vehicle:
- Total load is 2000 lbs (750 lb vehicle, 1000 lb fruit bin, 250 lb vehicle operator)
- Operator stands on the back deck of the vehicle, with controls attached to bicycle handlebars (or similar)
- One hub motor in each of the four wheels
- Motors need to be high torque with relatively low speeds (max speed would be 7-10 mph, and most of the time the operating speed would be 1-3 mph).
- Terrain is mild with mostly grass, hard pack dirt, and some concrete/asphalt with a max slope grade of 20%.
- Vehicle must be able to spin 360 degrees on a single axis when fully loaded, hence the skid steer configuration
- Motors and throttles must have foward and reverse functionality
- Right side motors must be controlled separately from left side motors
- Approximately 16" tire size
- Ideally I'd like just one controller to handle both right wheels, and a second controller to handle both left wheels. Or if there was a controller that could handle all four wheels and still achieve the desired functionality, that would be even better.
- Ideally the throttles would be dual-function twist throttles where you twist forward to go forward, and twist backward to go in reverse. If such throttles aren't available, I'm OK with thumb throttles with a second button or switch on each throttle for reverse.
- Braking system must include a parking brake to prevent movement when parked on a slope.
- I'm thinking the batteries would either be 36V or 48V.....something that is readily available and commonly used in similar-sized vehicles like golf carts. I need enough power storage to accommodate a full day of use without having to recharge, so anywhere from 2 to 6 batteries will probably be necessary.
- Clearance between bottom of frame and ground (when forks are fully raised) would be 5-6 inches.
Thanks in advance for any help, guidance, and recommendations!

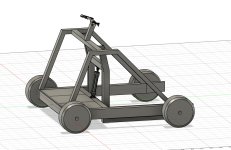
