My Masini Extremo (Erider Thunder) build stages during the last three years.
Bought it without controller, battery and BMS.
Battery
77V 100Ah 21S5P Li-NMC manufacturer Cenat
power pouch cell continous discharge 8C / continous charge 5C.
Battery weight 72kg including 254 M4 Screws and 120mm copper busbars. 13mOhm @20C measured at the controller terminals, including wiring, fuse (175A) and the BMS. Voltage drop at 175A 2,2V.
I even had to lengthen the battery case and the wheelbase by 3cm to fit this battery.
The battery was for free and had only done a few cycles, so why not make efforts to fit it.
Temperature controlled 60W battery heating powered from the battery. Battery fully isolated with Armaflex and foam rubber 10-30mm.
Integrated fanless charger, 2x Meanwell ELG240-42AB wired in series. Sitting under the battery housing, IP67 rated (waterproof)
Charging power adjustable from 10W-500W with a Potentiometer, charging to max 87,5V.
External 2-phase 400V charger 2x Huawei RG4875G5 in series , 7kW charging power current max 85A, controlled with an ESP32 and via Smartphone. Fully adjustable 83-117V 0-85A 0-8kw, max efficiency 97%
External single phase charger 2xVertiv R48-2000E3 in series, charging power up to 3,4kW max 42A, max efficiency 96%
BMS 200A continious and 350A up to 600 seconds, JK-B2A-24S, active balancing current 2A
Motor QS60V5000W with new 205°C 16mm² phase wires and 40mm magnets.
I also have the original Efun 8kw Motor with double 6mm² phase wires and 45mm magnets, but inside only 2/3 copper fill compared to the QS60V5000W
(Now QS273 60H 10000W 72V with 25mm² phase wires)
Started with an SVMC72260 Controller but killed it with feald weakening.
Then until May 2023 Sabvoton SVMC72150 with 175A Peak and 165A continous. Puts out up to 14kw.
Current unlock software does not work with my controller.
Top Speed 103km/h GPS verified without flux-weakening , with 50A Flux-Weakening enabled an 77V I reached 105km/h top speed (all with the QS60V5000W Motor From my previous 73km/h 60V scooter).
Top Speed 96km/h GPS verified with 50A Flux-Weakening enabled (with the original Masini 72V 8kW Motor)
From April 2023 to January 2024 Fardriver ND72680 with up to 350Adc and 680pA , measured 490A RMS phase current with a calibrated current clamp.
(Now with Fardriver ND721800 with up to 400bA and 1400pA.)
Top Speed reduced to 115kph, because the motor got to hot
Acceleration 0-80kph depending on current settings, with 300Adc and 630pA 7,6s
(now 0-100kph 6,6seconds)
Weight, 183kg plus driver 95kg (now 193kg)
A few impressionen during the last three years of modifications.
First battery fitting test
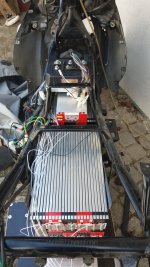
Damaged SVMC 72260 and ANT BMS. They died with a big bang, because I played with field weakening on the main stand.
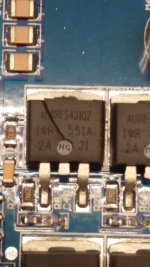
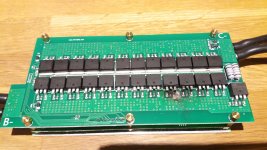
Changed all the fets on a hot plate , then it worked again for a few days, but after that it didn't recognice the halls anymore. Same happend to a SVMC72150 2 months later.
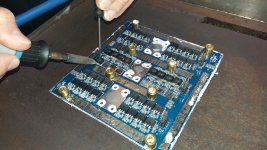
First battery load test with 7kw with an electronic load from 4,17V/celll to 2.8V/cell
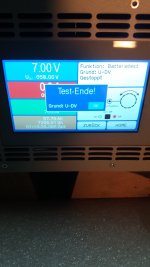
After the SVMC72150 died
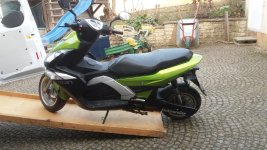
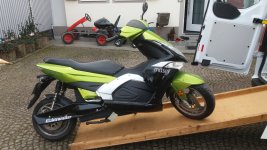
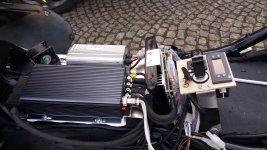
Took the battery out to change the link between the two 10S5P halfs and the 21th cell group. Now 6x6mm²
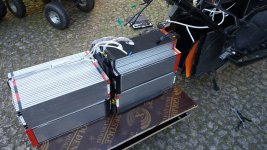
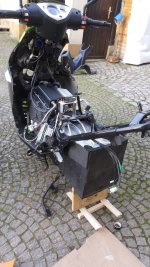
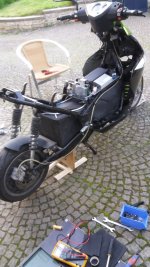
After the installation of the Fardriver ND72680 and the test of the temperature controlled fan, i had to install new phase wires to the QS60V5000W, because I melted and shorted them during my uphill tests. i upgraded from 13,3mm² to 16mm² 205C wires and added a temperature sensor.
The motor with less copper is the Masini 72V 8kW Motor.
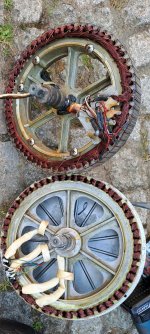
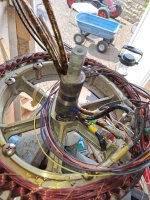
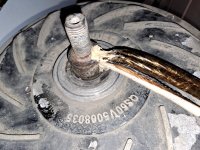
Added a 150A charge plug.
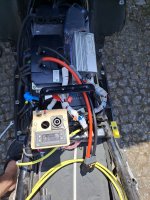
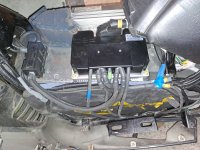
The 7kw charger 2xHuawei R4875G5 connected in series controlled with an ESP32.
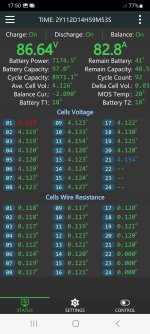
Terminal program on the phone to set values.
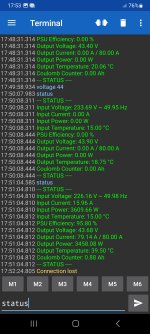
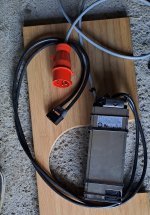
Bought it without controller, battery and BMS.
Battery
77V 100Ah 21S5P Li-NMC manufacturer Cenat
power pouch cell continous discharge 8C / continous charge 5C.
Battery weight 72kg including 254 M4 Screws and 120mm copper busbars. 13mOhm @20C measured at the controller terminals, including wiring, fuse (175A) and the BMS. Voltage drop at 175A 2,2V.
I even had to lengthen the battery case and the wheelbase by 3cm to fit this battery.
The battery was for free and had only done a few cycles, so why not make efforts to fit it.
Temperature controlled 60W battery heating powered from the battery. Battery fully isolated with Armaflex and foam rubber 10-30mm.
Integrated fanless charger, 2x Meanwell ELG240-42AB wired in series. Sitting under the battery housing, IP67 rated (waterproof)
Charging power adjustable from 10W-500W with a Potentiometer, charging to max 87,5V.
External 2-phase 400V charger 2x Huawei RG4875G5 in series , 7kW charging power current max 85A, controlled with an ESP32 and via Smartphone. Fully adjustable 83-117V 0-85A 0-8kw, max efficiency 97%
External single phase charger 2xVertiv R48-2000E3 in series, charging power up to 3,4kW max 42A, max efficiency 96%
BMS 200A continious and 350A up to 600 seconds, JK-B2A-24S, active balancing current 2A
Motor QS60V5000W with new 205°C 16mm² phase wires and 40mm magnets.
I also have the original Efun 8kw Motor with double 6mm² phase wires and 45mm magnets, but inside only 2/3 copper fill compared to the QS60V5000W
(Now QS273 60H 10000W 72V with 25mm² phase wires)
Started with an SVMC72260 Controller but killed it with feald weakening.
Then until May 2023 Sabvoton SVMC72150 with 175A Peak and 165A continous. Puts out up to 14kw.
Current unlock software does not work with my controller.
Top Speed 103km/h GPS verified without flux-weakening , with 50A Flux-Weakening enabled an 77V I reached 105km/h top speed (all with the QS60V5000W Motor From my previous 73km/h 60V scooter).
Top Speed 96km/h GPS verified with 50A Flux-Weakening enabled (with the original Masini 72V 8kW Motor)
From April 2023 to January 2024 Fardriver ND72680 with up to 350Adc and 680pA , measured 490A RMS phase current with a calibrated current clamp.
(Now with Fardriver ND721800 with up to 400bA and 1400pA.)
Top Speed reduced to 115kph, because the motor got to hot
Acceleration 0-80kph depending on current settings, with 300Adc and 630pA 7,6s
(now 0-100kph 6,6seconds)
Weight, 183kg plus driver 95kg (now 193kg)
A few impressionen during the last three years of modifications.
First battery fitting test
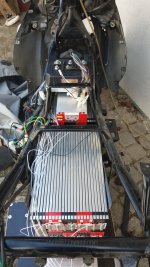
Damaged SVMC 72260 and ANT BMS. They died with a big bang, because I played with field weakening on the main stand.
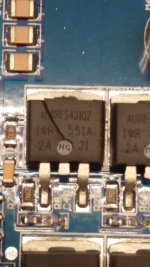
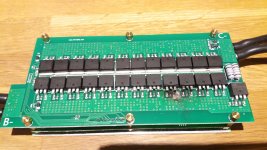
Changed all the fets on a hot plate , then it worked again for a few days, but after that it didn't recognice the halls anymore. Same happend to a SVMC72150 2 months later.
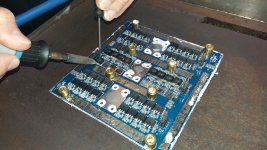
First battery load test with 7kw with an electronic load from 4,17V/celll to 2.8V/cell
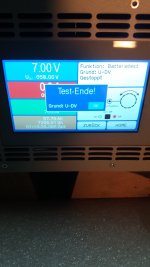
After the SVMC72150 died
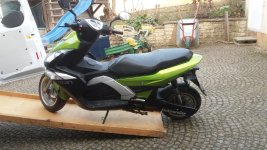
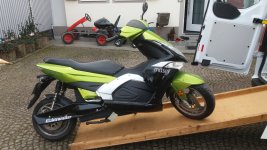
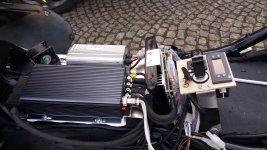
Took the battery out to change the link between the two 10S5P halfs and the 21th cell group. Now 6x6mm²
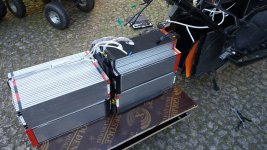
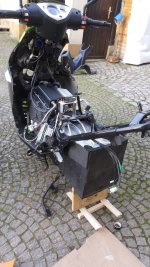
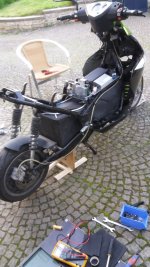
After the installation of the Fardriver ND72680 and the test of the temperature controlled fan, i had to install new phase wires to the QS60V5000W, because I melted and shorted them during my uphill tests. i upgraded from 13,3mm² to 16mm² 205C wires and added a temperature sensor.
The motor with less copper is the Masini 72V 8kW Motor.
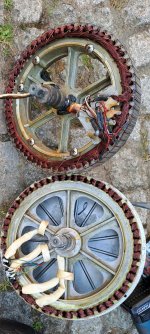
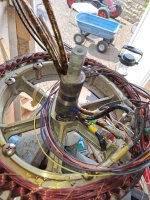
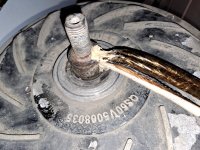
Added a 150A charge plug.
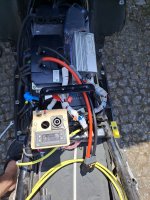
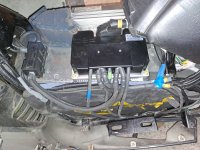
The 7kw charger 2xHuawei R4875G5 connected in series controlled with an ESP32.
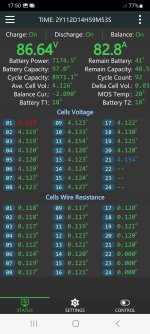
Terminal program on the phone to set values.
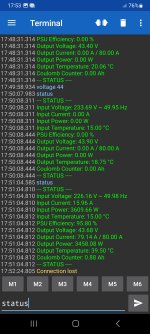
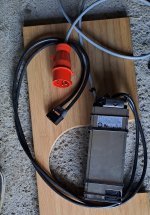
Last edited: