OK well, it's the end of a sweet wet dream.
I had a try at winding yesterday and now I realize just how clueless I was. Fell quickly from the mount of stupidity right down to the valley of despair!
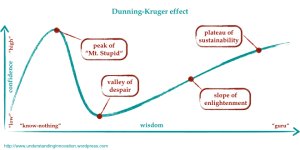
Winding is hard.
Like really, really hard.
I wasn't expecting it to be easy, but I sure wasn't expecting it to be that difficult.
So, I tried first with the 3mm wire. Made one bend, immediately scratched the insulation + realized that the bend radius is just way too big: epic fail.
Then I moved directly to the other extreme with the 1mm wire. I think I've put 15 wires in parallel, not sure anymore. This is around 11mm2 which is pretty much what was originally installed in the motor by QS.
I had a hard time, it is not pretty but I did manage to make two full coils. I can definitely confirm it is a lot easier when you are able to fit the wires through the opening on top of each pole.
But I can also pretty much also confirm that there is no way I can double the copper fill. The slot is already full and I don't see how I could cram more wires in there. At least certainly not twice this amount!
All my assumptions regarding copper fill came from using the wire and stator calculator tool:
But while this is a great tool in theory, well in practice I don't think I can trust it at all, at least not for this particular application.
The main problem is that you just can't fill slots as much because the wires have to cross each other while going from one coil to the other, so that wastes a lot of slot space. Kinda hard to explain, but basically I can't rely on this tool and will have to find the maximum copper fill by trial and error.
Also, while I successfully managed to wind these two coils physically, I did scratch them a lot. About 1/3rd of the wires were shorted to the core. The insulation paper is not nearly as tough as I expected, that's another big disappointment: it is thick so it takes a lot of space, but it isn't very tough. Also the wire insulation seem to be easily scratched, it is not very tough either.
After this mediocre success, I went trying the 1.5mm wire, 9 wires in parallel, which is 16mm2. Unfortunately this wire doesn't fit through the slots so I had to feed it by the sides. It is a lot more difficult this way, but it started well:
I gave a number to each wire in order to keep them aligned:
But it took only two turns to lose the nice alignment:
The worst part is: that's only 2 turns! Still have one to go, and then the other coils next to it.... Absolutely no way at all that this would fit into the slots.
Plus I had one wire shorted to the core, I really need to find a way not to scrath the insulation. What a PITA.
So... yeah, big disappointment.
The only positive thing in all this mess is that the tool I've built to hold the stator works very well. I can pull like a maniac and the thing doesn't move a bit.
Anyway, it is now time to be a little more humble and to get back to earth. At that point the objective is not to put more copper than QS: it is to actually manage to put as much as they did... Lame, I know, but I guess that's the difference between a good idea on paper and the actual reality of things.
I'll keep experimenting to find better ways to wind, especially dealing with the entry/exists of each coils which seem to affect the slot fill a lot, but I believe I will go with thinner wire eventually, at least something that fits the slots since it's a lot easier. Just like you suggested
@Hummina Shadeeba
Working with large wires is too difficult for the home gamer, the wire never stays straight no matter how hard you pull on it, you have to push it with some kind of stick, but even then it's not totally flat so that creates lots of empty spaces. Also my slots aren't square, they have very rounded edges so the coils tend not to want to conform at the top and the bottom of the slots, they all want to go to the middle. That makes packing neatly even harder.
I think I could do it relatively easily if it was only a single wire, but having the wires in parallel makes the things 10 times harder.