oatnet
1 MW
Stevil_Knevil said:Success!!
Here is the color-coding to connect the Shenzhen controller to a 400 series C-lyte motor:
Hall sensors-
BlkBlk
RedRed
YelYel
GrnBlu
BluGrn
Phase-
BluYel
GrnGrn
YelBlu
Wow Stevil, you just saved me a lot of re-work on my x5 install with this - THANK YOU!
I used Fechter's directions (THANK YOU TOO!) to install a CycleAnalyst connector (minus speedo/hall). I have to think these through each time I do them, so I though some pics might help if anyone else is as dumb as me. The colors on my connector are different, so I include a pic to show you that. I really appreciated the grommet setup on the Shenzhen - each wire has its own individual hole, somewhat sealed, and there were 6 free holes
-JD
View attachment 4
View attachment 3
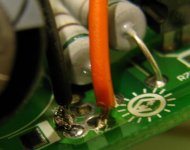
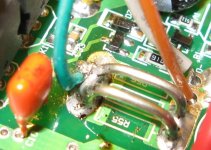
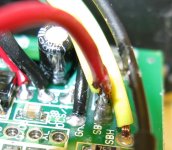