oatnet
1 MW
I have wanted a 3D printer for years, but the technology has been advancing so fast, that whatever I'd buy would be obsolete in weeks. I've been drooling over the ebike parts and cases that people here have been building, but I just couldn't pull the trigger.
However, the kit version of the TAZ 4 printer I saw mentioned on nechaus's 3D printer thread (thanks!)
convinced me to buy in. It is open source and modular, so I can upgrade components to keep up with advancements. The heated bed and large print area lets me make big parts, and the printer will use a large variety of materials - not only the standard ABS and PLA, but a range of plastics, stone and wood. It does not come with an enclosure to keep temperatures even for printing large parts, but I can build one.
I saved $400 buying the "kit" version of the printer, $1,600 plus $200 in "upgrade" parts vs $2,200. The factory built TAZ would probably be more precise because it is assembled on jigs, and I could be printing with it much sooner, but building it is a valuable education. I know where/why every nut and bolt goes because I put it there, so I am better prepared to troubleshoot it in the future, and I don't have any fear of dissecting an assembly that I can't get back together. I probably would have taken the factory-built one apart anyhow just to see how everything works, so I am saving tear-down time too.
The kit version comes with a 30 day warrantee, the factory version had one year; the parts are cheap, so I don't mind taking my chances. It also isn't "pre-wired for the dual-extruder nozzle"; that means there is only one extruder cable/plug comes with the kit, but the electronics box has a hole for the plug and a spot on the motherboard for it, so that is a simple cable purchase and 5 minutes of installation. It does not come with the LCD Screen/Enclosure/ cable, but I purchased it separately, which is why the kit only saved $400 instead of $600.
All that aside, I was looking forward to the "puzzle" of assembly. On my Dune Buggy project, an afternoon of final assembly would only happen after weeks or months engineering and trial and error. With this kit, I didn't have to do the engineering, just follow the instructions and have the instant gratification of finished modules.
I planned to post a whole build thread, but
the instruction manual covers it pretty well (click here), so instead I am going to post unboxing pics and some of the milestones along the way.
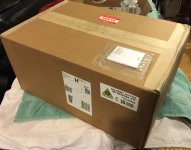
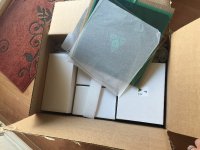
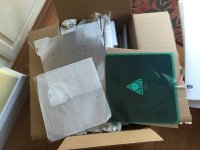
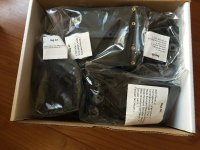
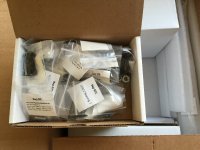
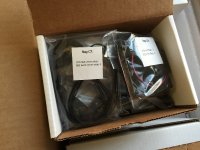
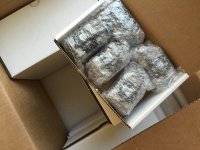
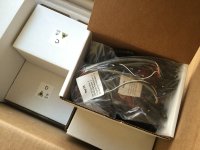
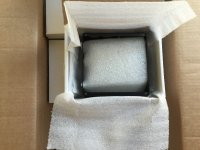
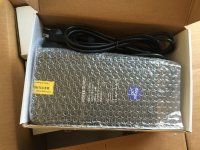
View attachment 6
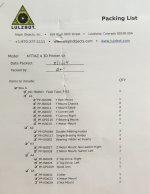
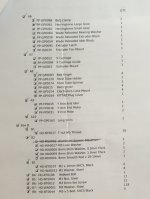
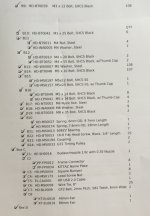
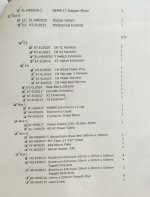
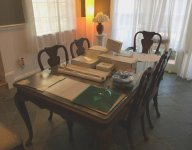
However, the kit version of the TAZ 4 printer I saw mentioned on nechaus's 3D printer thread (thanks!)
convinced me to buy in. It is open source and modular, so I can upgrade components to keep up with advancements. The heated bed and large print area lets me make big parts, and the printer will use a large variety of materials - not only the standard ABS and PLA, but a range of plastics, stone and wood. It does not come with an enclosure to keep temperatures even for printing large parts, but I can build one.
I saved $400 buying the "kit" version of the printer, $1,600 plus $200 in "upgrade" parts vs $2,200. The factory built TAZ would probably be more precise because it is assembled on jigs, and I could be printing with it much sooner, but building it is a valuable education. I know where/why every nut and bolt goes because I put it there, so I am better prepared to troubleshoot it in the future, and I don't have any fear of dissecting an assembly that I can't get back together. I probably would have taken the factory-built one apart anyhow just to see how everything works, so I am saving tear-down time too.
The kit version comes with a 30 day warrantee, the factory version had one year; the parts are cheap, so I don't mind taking my chances. It also isn't "pre-wired for the dual-extruder nozzle"; that means there is only one extruder cable/plug comes with the kit, but the electronics box has a hole for the plug and a spot on the motherboard for it, so that is a simple cable purchase and 5 minutes of installation. It does not come with the LCD Screen/Enclosure/ cable, but I purchased it separately, which is why the kit only saved $400 instead of $600.
All that aside, I was looking forward to the "puzzle" of assembly. On my Dune Buggy project, an afternoon of final assembly would only happen after weeks or months engineering and trial and error. With this kit, I didn't have to do the engineering, just follow the instructions and have the instant gratification of finished modules.
I planned to post a whole build thread, but
the instruction manual covers it pretty well (click here), so instead I am going to post unboxing pics and some of the milestones along the way.
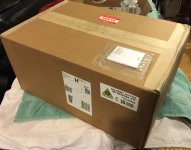
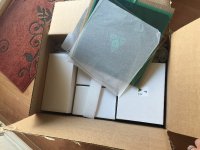
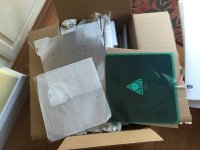
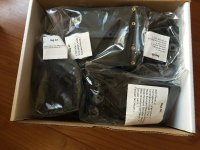
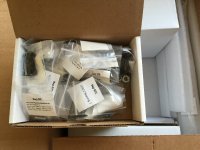
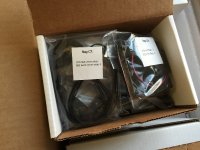
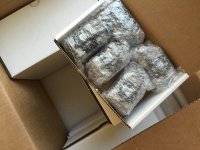
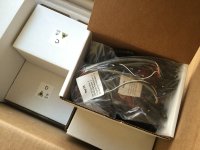
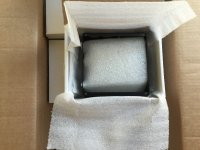
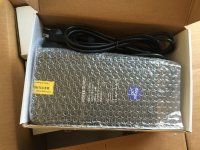
View attachment 6
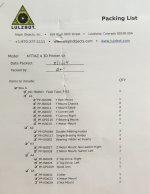
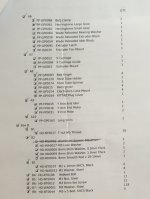
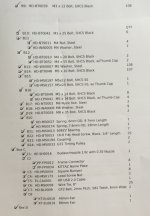
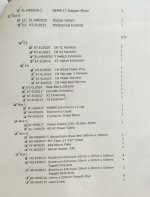
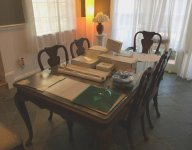