John in CR
100 TW
When you've got an angle grinder and welding machine along with these raw materials, how can you not want to build an ebike on a beautiful Saturday? Who else can see the ebike in there? 8)
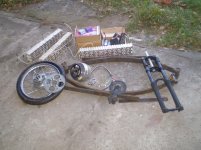
View attachment 3
I've got a structural engineering question. I'm going to use the leaf spring material for much of the frame. Let's Ignore torsional rigidity, which I'll have to address with cross bracing, and talk about rigidity inline with the bike. First, it's seems like putting the springs under pressure would be more rigid. My plan is to create a somewhat oval shape with 2 leafs facing each other like this:
View attachment 2
With the red as a brace there are 3 options.
1. No compression of the springs
2. Compression from the ends which would put the brace under tension
3. Compression of the springs from the top and bottom with would put the brace under compression from the ends.
Which would form a more rigid structure? My gut is telling me put that brace under tension, since I can use a simple thin strip of steel for that brace. I'm going to rip the springs lengthwise to make 2 of these shapes, one for each side, and join the 2 with panels and braces around most of the perimeter. It will get side panels too for something along these lines as a dual suspension high power mid-drive ebike.
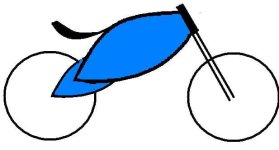
Any suggestions regarding where I'm going wrong on the structural ideas?
Now the big question is to get cranking with the angle grinder, or go pick up that plasma cutter I was eyeballing the other day. As long as a cheap one is reasonably durable it could pay for most of itself just in cutting discs on this one project. Leaf spring steel is tough stuff.
John
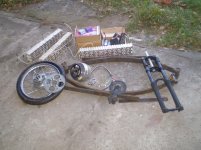
View attachment 3
I've got a structural engineering question. I'm going to use the leaf spring material for much of the frame. Let's Ignore torsional rigidity, which I'll have to address with cross bracing, and talk about rigidity inline with the bike. First, it's seems like putting the springs under pressure would be more rigid. My plan is to create a somewhat oval shape with 2 leafs facing each other like this:
View attachment 2
With the red as a brace there are 3 options.
1. No compression of the springs
2. Compression from the ends which would put the brace under tension
3. Compression of the springs from the top and bottom with would put the brace under compression from the ends.
Which would form a more rigid structure? My gut is telling me put that brace under tension, since I can use a simple thin strip of steel for that brace. I'm going to rip the springs lengthwise to make 2 of these shapes, one for each side, and join the 2 with panels and braces around most of the perimeter. It will get side panels too for something along these lines as a dual suspension high power mid-drive ebike.
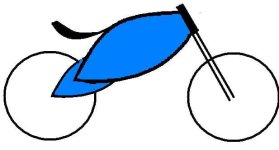
Any suggestions regarding where I'm going wrong on the structural ideas?
Now the big question is to get cranking with the angle grinder, or go pick up that plasma cutter I was eyeballing the other day. As long as a cheap one is reasonably durable it could pay for most of itself just in cutting discs on this one project. Leaf spring steel is tough stuff.
John