I'm assuming the most typical rear dropout on an MTB is 10mm nominal (mine is 10.4mm actual) and 135mm width. Most hub motors designed for this size have a 12mm axle that is ground down on each side by 1mm.
This is how an actual 12x10 axle will look like in a 10mm dropout (well, 10.4mm in the illustration).
Filing away 0.4mm of material will make it sit flush. But does it really matter?
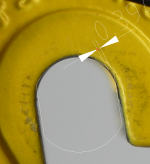
This is how an actual 12x10 axle will look like in a 10mm dropout (well, 10.4mm in the illustration).
Filing away 0.4mm of material will make it sit flush. But does it really matter?
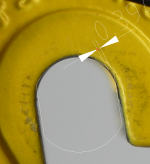