hello, I have a question about a 12v contactor rated for at least 200amps, perhaps 450 amps. it is a large black cylinder with two large threaded posts (assumed positive) and a single small post near the bottom, the base plate is steel and ground. To test the operation and hookup, no labels on the housing, I used a 7.4v lipo battery, switch, and a light bulb. I hit the switch heard a click and the bulb lights up, so it works!
to test in the operation under load, I hooked it up again with a 48v ebike battery, a 1500 watt speed control 200amp breaker, and bldc motor and switch. turned it on, and pushed the throttle just a little bit. tires move.... immediately I noticed a smell and the body of the connector was getting very hot. I didn't take the time to get a temp reading, and i'm not sure what a dangerously high temp would be. given the low load, I thought it prudent to unhook everything. I noticed the heat remained for some time.
if the connector is activated, it must be hooked up properly right? was I overly concerned without cause? I assume the 12v rating is the issue but it is a little surprising it started heating up so quickly to the point I was worried it might start melting down. what is going on here? how do these connectors work, they use a coil and spring right? why would it get so hot so fast?
I thought the main issue with connectors or switches at higher voltage is the arc causing damage to the internal pads, when the connection is made. beyond this, if the load is small, like a small light, it should be ok. is this wrong? this is why you use anti-spark resistor, to slow the charge across the circuit, for example when capacitors charge. I did not have such a resistor hooked up and assumed with the high amp rating and low load it would be ok. I don't think the connector is necessary for this controller but for a different controller, it will be necessary to understand this properly.
if i have a need for accessories that operate at high voltage but low amps what type of switch is suitable? and is the anti-spark resistor the best way to protect the switch from premature wear?
the picture is not the same unit. mine has three posts was originally purchased for another project from a robotics website.
to test in the operation under load, I hooked it up again with a 48v ebike battery, a 1500 watt speed control 200amp breaker, and bldc motor and switch. turned it on, and pushed the throttle just a little bit. tires move.... immediately I noticed a smell and the body of the connector was getting very hot. I didn't take the time to get a temp reading, and i'm not sure what a dangerously high temp would be. given the low load, I thought it prudent to unhook everything. I noticed the heat remained for some time.
if the connector is activated, it must be hooked up properly right? was I overly concerned without cause? I assume the 12v rating is the issue but it is a little surprising it started heating up so quickly to the point I was worried it might start melting down. what is going on here? how do these connectors work, they use a coil and spring right? why would it get so hot so fast?
I thought the main issue with connectors or switches at higher voltage is the arc causing damage to the internal pads, when the connection is made. beyond this, if the load is small, like a small light, it should be ok. is this wrong? this is why you use anti-spark resistor, to slow the charge across the circuit, for example when capacitors charge. I did not have such a resistor hooked up and assumed with the high amp rating and low load it would be ok. I don't think the connector is necessary for this controller but for a different controller, it will be necessary to understand this properly.
if i have a need for accessories that operate at high voltage but low amps what type of switch is suitable? and is the anti-spark resistor the best way to protect the switch from premature wear?
the picture is not the same unit. mine has three posts was originally purchased for another project from a robotics website.
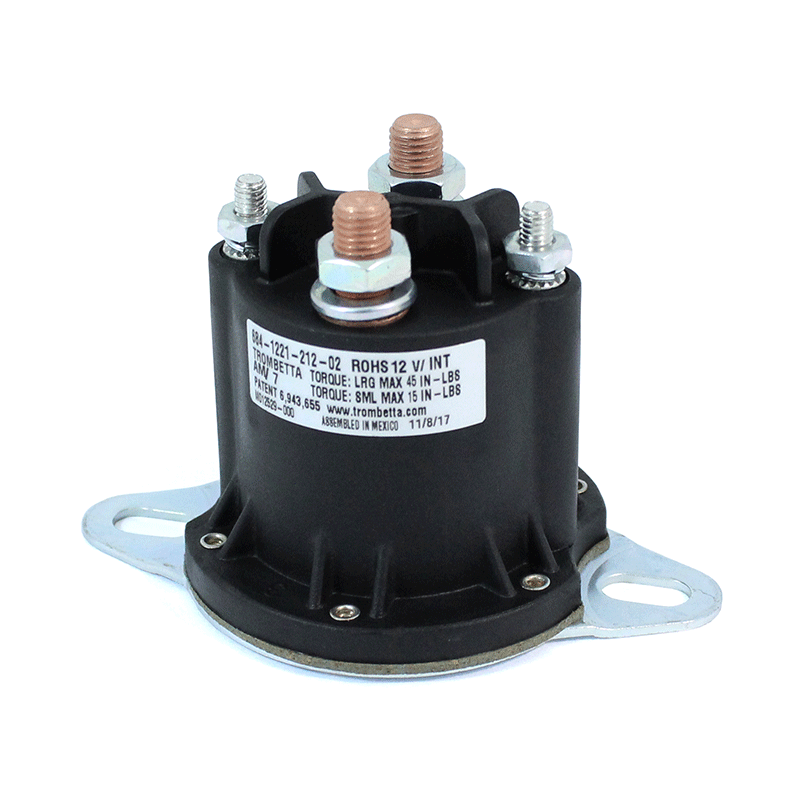