mistercrash
10 kW
It's a father/son project, I want my 12 year old boy to learn to use some tools and do mechanical work in a safe way. It's the blue scooter in front.
And this is what it looks like at the moment.
We have a bunch of parts that we cleaned up and took pictures of, if we are able to sell all of them, including the GY6 engine, we should recuperate the money we spent to buy the scooter.
The motor and controller have been ordered from QS Motors. An 8000W 273 (50H) V3 Hub Motor in a 13X3.5 inch tubeless rim. An APT Programmable Sine Wave FOC AE96600 72V/96V 8kW PM Motor Driver Controller. The battery will be 10 Nissan Leaf modules. The cells will be monitored with the HVA/LVA I built for my other scooter. We are hoping to keep the original odometer/speedometer but it has been difficult to find a 12/13 inch front wheel that would be thin enough to use the worm gear. If we have to ditch the odometer/speedometer we will have to use the CA to replace it.
On the list of things we need to do is:
- weld a bracket for a second rear shock absorber on the right
- weld a couple brackets from angle iron to accept the battery box
- build the battery box
- build and weld a bracket to secure the controller
- have a custom bike shop build a swingarm
- clean up the original electric harness
The only things we found that were damaged on the scooter were the o-rings on the shaft where the rear suspension pivots and the front shock boots. The scooter is in very good shape. We plan to have the battery slip in from the top and rest on the angle irons welded to the frame. This will keep it from moving left or right and front or back. A couple pieces of metal strapping bolted to the frame will keep the battery from moving up or down.
The controller is to big to put in anywhere else than between our feet. We need a bracket to hold it and despite the fact that it is completely waterproof, we want some plastic box to hide it from view and protect it from the elements.
We'll update as the conversion goes along.
Thanks for reading
Ray and Gabriel
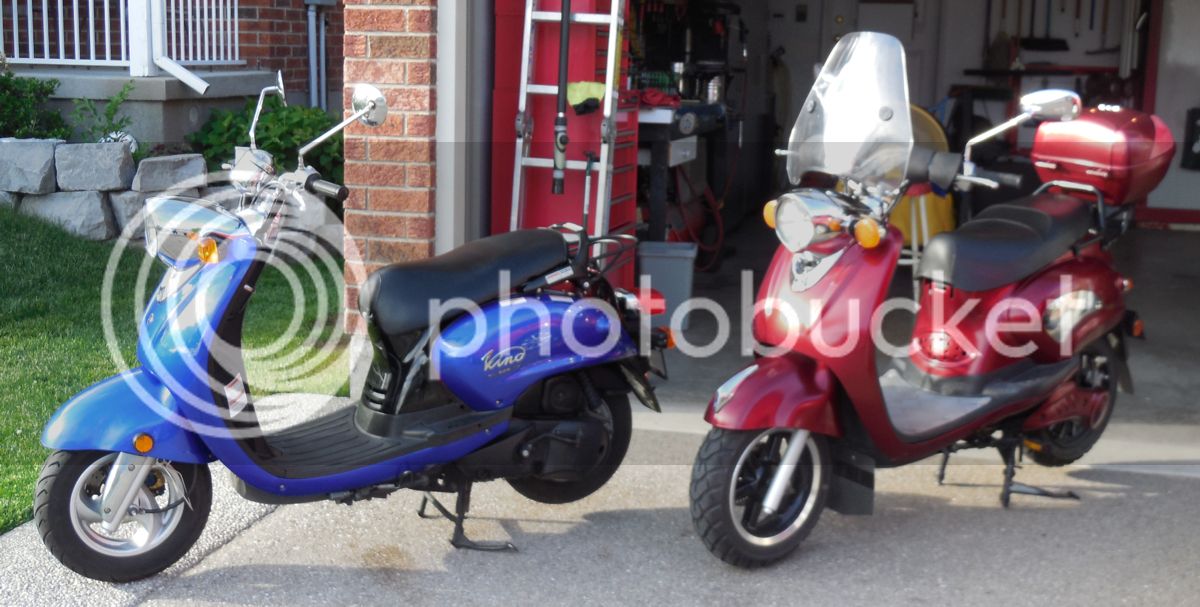
And this is what it looks like at the moment.
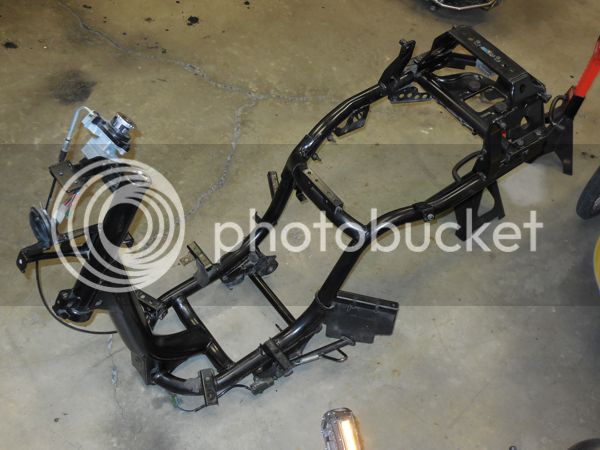
We have a bunch of parts that we cleaned up and took pictures of, if we are able to sell all of them, including the GY6 engine, we should recuperate the money we spent to buy the scooter.
The motor and controller have been ordered from QS Motors. An 8000W 273 (50H) V3 Hub Motor in a 13X3.5 inch tubeless rim. An APT Programmable Sine Wave FOC AE96600 72V/96V 8kW PM Motor Driver Controller. The battery will be 10 Nissan Leaf modules. The cells will be monitored with the HVA/LVA I built for my other scooter. We are hoping to keep the original odometer/speedometer but it has been difficult to find a 12/13 inch front wheel that would be thin enough to use the worm gear. If we have to ditch the odometer/speedometer we will have to use the CA to replace it.
On the list of things we need to do is:
- weld a bracket for a second rear shock absorber on the right
- weld a couple brackets from angle iron to accept the battery box
- build the battery box
- build and weld a bracket to secure the controller
- have a custom bike shop build a swingarm
- clean up the original electric harness
The only things we found that were damaged on the scooter were the o-rings on the shaft where the rear suspension pivots and the front shock boots. The scooter is in very good shape. We plan to have the battery slip in from the top and rest on the angle irons welded to the frame. This will keep it from moving left or right and front or back. A couple pieces of metal strapping bolted to the frame will keep the battery from moving up or down.
The controller is to big to put in anywhere else than between our feet. We need a bracket to hold it and despite the fact that it is completely waterproof, we want some plastic box to hide it from view and protect it from the elements.
We'll update as the conversion goes along.
Thanks for reading
Ray and Gabriel